Servicing CO₂ Refrigeration Systems
CO₂ systems operate under much higher pressures than HFC systems, and contractors must be aware of and prepared for this when charging these systems

Carbon dioxide (CO2) is a very efficient, nontoxic, and nonflammable refrigerant, earning it an A1 rating. The gas has a global warming potential (GWP) of 1, making it a highly desirable solution in society’s quest for sustainability.
Suddenly in high demand, HVAC contractors must quickly acclimate themselves with the gas and its unique characteristics and service attributes, which differ from traditional hydrofluorocarbon (HFC)-based systems.
Charging the System
CO2 systems operate under much higher pressures than HFC systems, and contractors must be aware of and prepared for this when charging these systems.
“If a system is charged with liquid CO2 below the triple point pressure of 60.4 psi, it will turn into dry ice,” said Peter Savage, project manager, controls division, AAA Refrigeration Service Inc., which has built, remodeled, or designed nearly 50 stores equipped with CO2 refrigeration since 2015. “At specific pressures, contractors must charge a system with vapor to minimize the formation of dry ice.”
Savage said technicians should first introduce the gas as a vapor before slowly building toward that key number of 60.4 psi.
“Aside from the pressure, the flash gas bypass valve and high pressure valve (HPV) are really the only two main components that are different from an HFC system,” he said. “Though, when adjusting pressure or temperature, it’s important for techs to understand that changing one set point will likely affect numerous aspects of the system.”
Under Pressure
Even when a CO2 system is shut off, the system maintains high pressures, thus technicians must be aware of the risks involved.
Tracking the state of the refrigerant is especially challenging within high-pressure CO2 systems.
Once CO2 hits a certain point, there's no correlation on a traditional pressure-temperature (PT) chart, which can be confusing for techs, said Brett Wetzel, manager of technical troubleshooting and training, CoolSys Midwest.
“As techs, we often don’t know whether the refrigerant is a liquid or a gas,” said Wetzel. “We either have to open up the system or take scientific measurements to figure that out.”
Once the refrigerant reaches 87°F saturated temperature, it’s in a plasma-like state, he said. The use of high pressure valves (HPVs) can help to alleviate some of these PT challenges.
“Theoretically, if you have 75° saturated temperature, the HPV is trying to control 5° of subcooling, although the flash tank will go all the way down to 38° saturated pressure," Wetzel said. “And if the liquid is warmer than 38°, it’s expected to flash off to a vapor, but that doesn’t always hold true with CO2.”
Once the refrigerant is used transcritically, the liquid production does reduce to as low 50/50. During subcritical mode, it's more like 70% liquid production and 30% vapor, Wetzel said.
“Once it hits transcritical, that extra mass of vapor has to be compressed by something, such as parallel compression, to pull the gas down to the 38° saturated point that’s typically appropriate for the flash tanks,” he said.
Conclusion
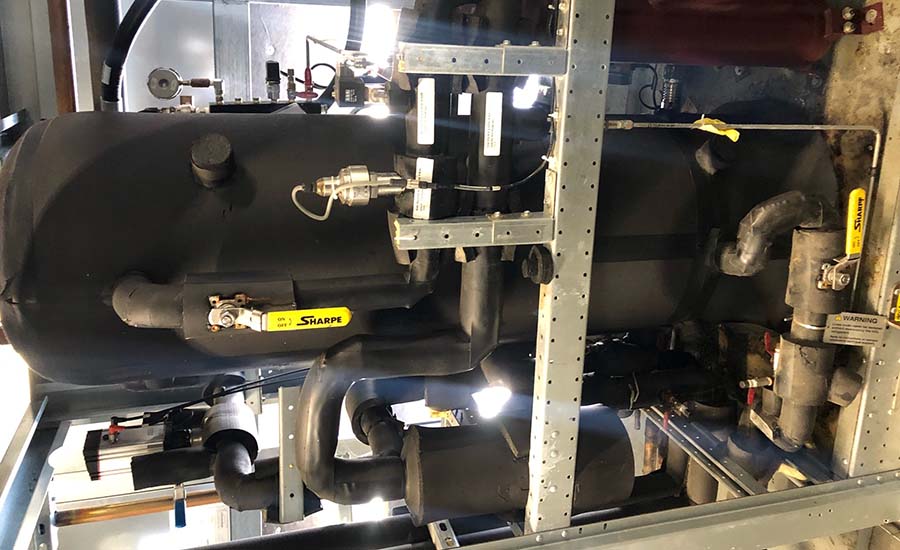
SIMILAR SERVICE: While CO2 systems are not without their anomalous features, for the most part, servicing a CO2 rack is no more challenging than any other piece of HVAC refrigeration equipment. (Courtesy of CoolSys)
While CO2 systems are not without their anomalous features, for the most part, servicing a CO2 rack is no more challenging than any other piece of HVAC refrigeration equipment, said Savage.
“Provided a proper startup is performed and proper piping practices are followed, the leak rates should be no different than a similar system utilizing R-448A,” he said. “There are safety reliefs in place that will vent should the pressure get too high, but there are also ways to mitigate that such as utilizing a generator backed auxiliary unit that will maintain the flash tank pressure during power failures.”
Experienced refrigeration techs should not be fearful of CO2 systems, said Wetzel.
“In order to be safe, techs need to understand the sequence of operation, so that they’re shutting down the proper shut off valve in order to access specific oil separators or other components,” he said.
If they haven’t already, Wetzel encourages commercial refrigeration companies to begin educating themselves on the nuances of CO2 today.
“There are 47,000 CO2 systems operating in Europe right now, and that’s just the rack-type systems, which doesn’t include the single-condensing units,” added Savage. “The U.S. is next in line, so if you haven’t started to work with these systems, it’s only a matter of time before you do.”