The commercial refrigeration industry is in the process of transitioning away from high-GWP refrigerants, such as R-404A and R-134a, to low-GWP alternatives, such as CO2 (R-744) and propane & (R-290), as well as A2L refrigerants. Few people know more about this transition than Tristam Coffin, who played a pivotal role in steering Whole Foods Market toward the integration of natural refrigerants and eco-friendly solutions within their stores — well ahead of current federal and state regulations.
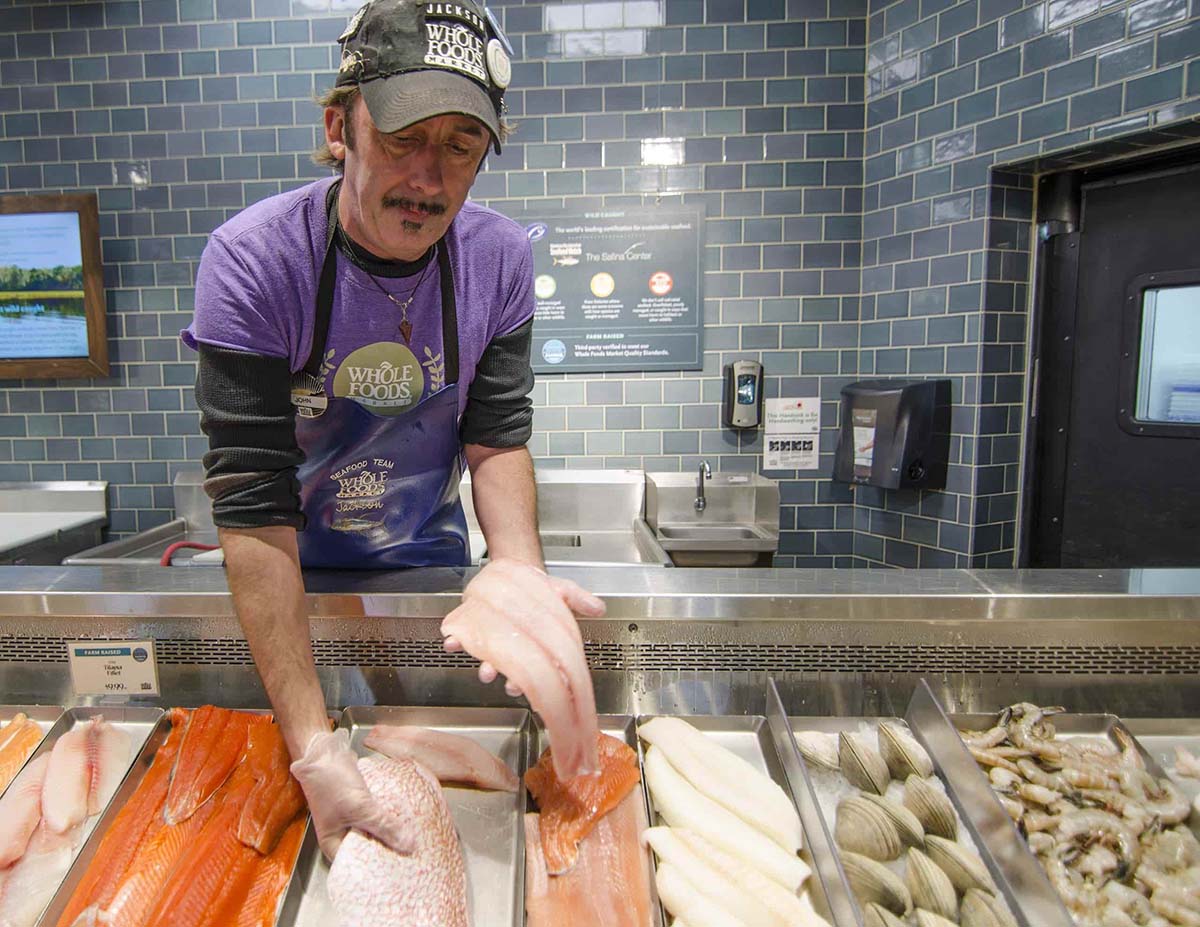
LOW-GWP SOLUTIONS: Whole Foods has retrofitted many of its stores with energy-efficient and low-GWP solutions. (Courtesy of Whole Foods Market)
After leaving Whole Foods in 2020, Coffin helped found êffecterra inc., a sustainability and engineering solutions group based in Reno, Nevada, that is dedicated to “developing, commercializing, deploying, and scaling climate solutions.” Given his wide-ranging expertise in sustainable solutions, The ACHR NEWS asked Coffin to share some of his knowledge about what contractors and end users need to know about transitioning to low-GWP refrigerants.
ACHR NEWS: Briefly describe your tenure at Whole Foods, including the changes you brought about regarding their refrigeration systems.
Coffin: I spent over a decade at Whole Foods, which sees environment stewardship and protection as a core value. This was an enabling environment for impact, as I came to understand that refrigeration was — and remains today — the industry’s single-biggest lever for climate action. These opportunities included retrofits with energy-efficient and low-GWP solutions and rigorous maintenance to prevent refrigerant leaks. But it also included blank-slate opportunities, such as a ground-up development in Brooklyn. Opened in 2013, it was the first U.S. retail grocery to operate without synthetic refrigerants. Dozens of similar projects followed utilizing mainly natural refrigerants, many of them firsts of their kind. This helped lay the groundwork in the U.S. on the industry’s necessary transition to alternative, ultra-low GWP system architectures.
ACHR NEWS: What does êffecterra specialize in, and what is your role there?
Coffin: I am the co-founder and president of the sustainability, policy, and technical services practice at êffecterra, which is a Public Benefit Corporation that provides sustainability technical support to companies and investors, as well as state and local governments. We apply a technical problem-solving mindset and deep expertise to solve our partners’ net zero and circular economy challenges. From social to corporate environmental goals, including niche expertise in refrigerant management and advanced refrigeration, air conditioning, and heat pump (RACHP) systems, we help clients set meaningful targets, then develop, integrate, and deploy successful action plans.
ACHR NEWS: At Whole Foods, how did you educate yourself about the alternative refrigerants and refrigeration architectures?
Coffin: Thankfully, my education was interdisciplinary, spanning natural sciences, social sciences, and engineering. I came to this with a good base of knowledge, but was by no means an expert. And so I surrounded myself with people more knowledgeable than I — but not necessarily on alternative refrigerants — from service, to design, to manufacturing. Then I asked a lot of questions, developed some great partnerships, and began testing numerous system architectures that aligned with our environmental, operational, and financial objectives. Many were my concepts informed by our expert partners and made a reality by various OEMs, controls experts, contractors, and others. Some were more successful than others, but all provided valuable lessons and positioned Whole Foods as a leader — far ahead of what was to become the regulatory standard in the grocery industry.
ACHR NEWS: Were there any challenges that arose when transitioning to natural refrigerants? Did anything surprise you about the new systems?
Coffin: There are going to be challenges and lessons to learn, whether it’s the first or 100th time through any process. That’s why with systems that showed promise (e.g., CO2 transcritical), we didn’t do just one system, we did many. Along the way, we had charges being blown, system optimization and commissioning taking more time than anticipated, and the need to bring service providers up to speed, but all involved were invested in making the projects a success. It was imperative to ensure everyone had a seat at the table early in the process; that kind of integrated process is critical. Honestly, the biggest surprise was that despite people saying it couldn’t be done, we continued to do it — thanks largely to my team’s leadership and the trust of our partners and providers — and do it quite well, in retrospect.
ACHR NEWS: What role can refrigeration contractors play in helping their food retail customers transition to low-GWP and/or natural refrigerants such as CO2, ammonia, and propane? How should they address existing HFC (or HCFC) equipment?
Coffin: Educate yourself; do whatever it takes to get trained; land jobs working on natural refrigerant projects; and ensure knowledge transfer in your organization. For example, send the superintendent from California who has done a few CO2 projects to another state when they get their first contract. Arguably, contractors have the most critical role in the transition to advanced low-GWP systems. Without the proper workforce, this transition doesn’t happen. This is truly an all-hands-on-deck initiative. I applaud the North American Sustainable Refrigeration Council (NASRC), which has chosen to address this challenge — not just because they see the transition to alternative refrigerants requiring it, but because maintaining legacy HFCs/HCFCs systems is equally important to addressing emissions and cost burdens to food retailers.
ACHR NEWS: What factors need to be considered when choosing a low-GWP refrigerant/refrigeration architecture? Should synthetic options be considered as well?
Coffin: At êffecterra, we don’t believe there is a one-size-fits-all approach to choosing a low-GWP system architecture. The scale of the challenge necessitates a plethora of solutions. That said, there is a need to further standardize and drive efficiencies in design and manufacturing. To have sustainable cooling and heating, we must adopt alternatives that do not cause collateral environmental damage — such as destroying the stratospheric ozone layer, trapping insane amounts of heat in the atmosphere, or polluting our water bodies with “forever chemicals” or PFAS. The only category of alternative refrigerants available today that meets all those criteria are natural refrigerants. Substances like CO2, ammonia, and hydrocarbons that occur naturally in our environment and can be leveraged as refrigerants or heat transfer fluids due to their great thermodynamic properties.
Co-founder and president
Êffecterra
ACHR NEWS: What obstacles are preventing food retailers from transitioning to low-GWP refrigeration systems?
Coffin: End-uses such as commercial/industrial refrigeration, cold storage, and ice rinks are well on their way to switching to naturals. However, they need greater incentive funding to help achieve economies of scale, retrofit existing buildings, and address service workforce readiness challenges. We need more training, more talent entering the industry, more players in the U.S. market (e.g., leaders in non-U.S. geographies), and — most importantly — we need the naysayers to get out of the way. The writing is on the wall: the only way we get close to our climate objectives is by transitioning to low-GWP systems — namely, naturals. An excellent resource I would recommend for anyone seeking more information is the report we recently authored for the New York State Department of Environmental Conservation on this very topic.
ACHR NEWS: What do you know now that you wish you knew during your first natural refrigerant equipment installation?
Coffin: So many things! I’ve been fortunate to learn from many talented partners over the years, and I am still learning. I’ve found that when you take a collaboration-forward approach to your work, this enables continuous learning and development. Getting back to the heart of the question: if I had to say one thing, I would say controls. We have advanced our control knowledge such that if the industry knew then what we know now, everyone’s lives would’ve been easier. Too often, the industry lets the controls dictate the system versus the system dictating the controls. That must change in order for us to advance efficiently and effectively with the transition to natural refrigerants.
Report Abusive Comment