As mandated by the AIM Act, the commercial refrigeration industry is transitioning away from high-GWP refrigerants, such as R-404A and R-134a, to low-GWP alternatives, such as CO2 (R-744) and propane (R-290). A2L refrigerants will also soon be part of the mix, thanks to Environmental Protection Agency’s (EPA’s) proposed Significant New Alternatives Policy (SNAP) Rule 26, which would allow the use of some of these mildly flammable alternatives in certain kinds of new refrigeration equipment.
Manufacturers have been gearing up for this transition to low-GWP refrigerants for a number of years and are now introducing an extensive range of innovative commercial refrigeration technologies. This wave of innovation is poised to help refrigeration contractors guide their food retailer clients to choose the optimal low-GWP solution — one that meets their specific needs as well as complies with the regulatory requirements.
New Solutions
In Heatcraft’s transition to low-GWP equipment, the emphasis is on enhancing the performance, application robustness, reliability, and quality of new commercial refrigeration solutions, while keeping costs as low as possible, said David Bolaños, head of product management at Heatcraft Refrigeration Products. And because equipment using these new refrigerants can be more complex, the company is designing systems that simplify the application, installation, and service of these new units.
“Controls and control algorithms, including those for defrost, are being updated to make sure that when a refrigerant is chosen, the system will operate properly without any more effort or attention than has been historically required of installers and servicers,” said Bolaños. “Technology advancements are also being employed to sense refrigerant leaks and execute mitigation actions as required by new safety standards for flammable refrigerants.”
At Danfoss, a wide range of products are available today to address systems designed around natural refrigerants with zero or very low GWP, as well as HFO-A2L refrigerants with low GWP, such as R-454A, R-454B, R-454C, R-455A, and others, said Christopher Gangemi, regional segment marketing manager of refrigeration solutions at Danfoss.
“These products range from mechanical and electrical controls that are compatible with both flammable and nonflammable refrigerants, compressors, heat exchangers, and sensors,” he said. “The sensors include leak detectors for CO₂ and the flammable refrigerants that are going to be required on some refrigeration equipment. Semi-hermetic compressors for both CO₂ and HFO-A2L refrigerants are the latest addition to the Danfoss lineup after the acquisition of BOCK earlier this year.”
For over a decade, Copeland has been advancing technologies suitable for lower-GWP refrigerants, beginning with compression platforms optimized for CO2 and R-290, said Kurt Knapke, vice-president solution strategy at Copeland. He noted that recent regulatory changes have also paved the way for lower-flammability A2L refrigerants and larger charges of R-290 in specific commercial refrigeration end uses.
“In anticipation of the imminent approval of these lower-GWP alternatives, Copeland has been optimizing our compressor platforms to meet market demand,” he said. “Copeland continues to lead in the development of state-of-the-art, fully integrated CO2 compression, system, and case system controls technologies, as well as essential high-pressure valves and components. Our commitment to innovation has resulted in improvements in reliability, performance, and energy efficiency — while simplifying the application of CO2 in commercial refrigeration.”
Copeland currently offers subcritical CO2 scroll compressors, transcritical CO2 semi-hermetic compressors, and subcritical CO2 semi-hermetic compressors. The CO2 transcritical and subcritical semi-hermetic compressors are equipped with on-board electronics to enable communication with the E3 supervisory control, designed specifically for CO2 systems, said Knapke. In addition, the company offers scroll compressors, hermetic reciprocating compressors, condensing units, drives, and electronic componentry rated for use with R-290. Copeland is also expanding its high-horsepower, R-290, scroll platform from .75 to 4 HP, supporting charges up to 500 grams.
Finally, Copeland scroll, semi-hermetic, hermetic reciprocating, and condensing unit platforms are being optimized for use with R-455A (146 GWP), R-454C (148 GWP), and R-454A (238 GWP).
“We’re integrating our leading-edge compression technologies, leak detection sensors, and E3 supervisory control platform to create next-generation solutions designed to maximize A2L application safety and refrigeration reliability,” said Knapke. “Copeland is also optimizing its variable-speed compression technologies for use with lower-GWP refrigerant alternatives, such as CO2, R-290, and A2Ls.”
Zero Zone manufactures refrigerated display cases, as well as commercial and industrial refrigeration systems, that cover a wide range of applications utilizing low-GWP refrigerants. For example, their Genesys Natural Refrigeration Solutions, CO2 (R-744), and ammonia (R-717) systems, not only meet regulatory demands, but present the end user with unique options to seamlessly fit their business needs and sustainability goals, said Jason Harren, industrial sales manager-Central at Zero Zone.
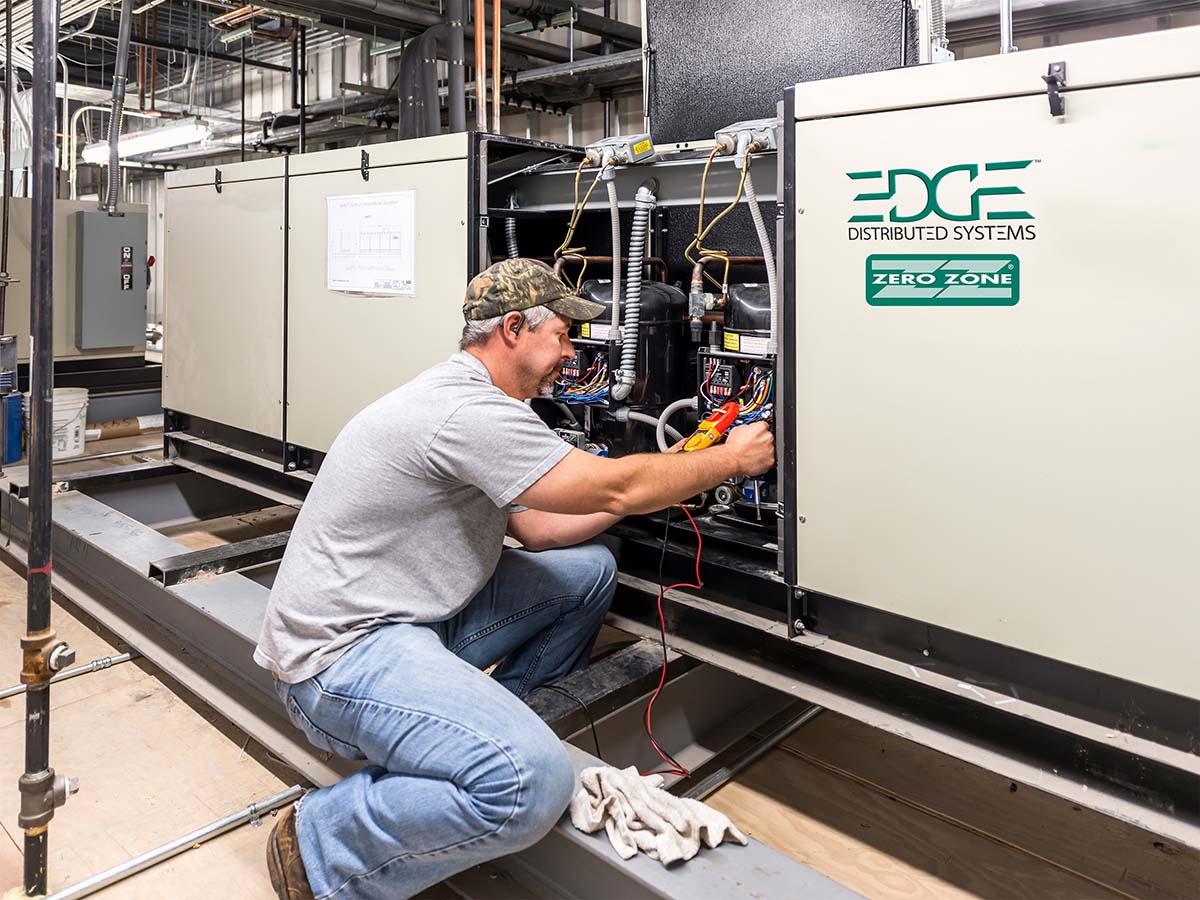
DAUNTING TASK: Making a mechanical change from HFCs to low-GWP alternatives can be a daunting task for food retailers. (Courtesy of Zero Zone)
“The Genesys product line presents a complete solution — a package system ready to install and commission,” he said. “Keeping service in mind, Zero Zone is currently designing systems that are better for service, while offering support and training to technicians and customers transitioning to the use of low-GWP refrigerants. Our reputation is built on over 60 years of innovation, quality, and responsiveness, and we intend to continue down the path as the world transitions to low-GWP refrigerants.”
Regional segment marketing manager of refrigeration solutions
Danfoss
Making the Change
That said, making a mechanical change from HFCs to low-GWP alternatives can be a daunting task for food retailers — especially because each of the alternatives has different cost impacts, whether upfront or in the future, said Harren.
“One major factor that food retailers need to consider is the energy efficiency and operating costs of some of the alternatives,” he said. “In addition, store owners will have to consider whether there are local contractors who can service the new equipment, as well as the status of local codes and service part availability. These factors could drive owners to repair rather than replace their equipment, but the decision cannot be made without weighing all options.”
Gangemi agrees that food retailers must look at first cost, budgets, and availability of properly trained technicians when considering low-GWP systems. Regardless of the choice made, any existing HFC equipment and systems will need to be decommissioned and replaced by new equipment designed specifically for the low-GWP refrigerants, he said. That’s because there is not a drop-in, low-GWP replacement refrigerant available today for existing equipment. However, new low-GWP systems will benefit end users in several ways.
“For food retailers with a facility management program, leak detection technologies can provide early detection of leaks as they emerge and allow for appropriate actions to be taken to prevent the leak from spreading too far,” said Gangemi. “Overall, leak detection can help mitigate the potential of a refrigeration system running inefficiently, reduce service costs, and eliminate food loss.”
The advancement of low-GWP technologies will also provide opportunities for food retailers to achieve energy-efficiency, performance, and sustainability improvements, said Knapke. For example, he noted that Copeland variable-speed compression technology can modulate capacity from 25% to 180% and deliver 20% to 30% energy-efficiency gains over their fixed-speed counterparts.
“From a refrigeration performance perspective, this enables precise load matching, tighter temperature control, and improved food quality and safety,” he said. “When compared to fixed-speed compression, our lab testing shows that variable-speed technology reduces compressor cycling by 90% — eliminating excessive compressor wear and tear, lowering maintenance costs, and extending equipment lifecycles.”
Knapke added that food retailers are also maximizing the sustainability potential of CO2 by deploying heat reclamation strategies in their facilities for a variety of purposes, such as HVAC, hot water, and concrete slab heating.
Contractors can help their food retail customers make the right choice of low-GWP equipment by having a full understanding of the refrigerants and regulatory landscape, said Bolaños. This includes understanding the latest updates to facilitate an effective, comprehensive discussion with customers to make sure they are clear on the options available, what the advantages and disadvantages are for each, and how to best think through selecting the right refrigerant and technologies for today, tomorrow, and the foreseeable future.
“In addition, lean on a company like Heatcraft to whatever extent you need, whether it is simply for a quick update or in-depth scenario reviews where it may even make sense for us to join in the conversation,” he added. “And be sure you fully consider federal, state, and municipal regulations, codes and standards to avoid any surprises.”
Contractors and technicians should also be fully trained on how to work with the alternative refrigerants, as safety is the top priority, said Bolaños. “Whether working with the mildly flammable A2Ls, the quite flammable A3s like propane, or the higher pressures of CO2, all of us must be experts in handling refrigerants and installing, servicing, repairing, and maintaining equipment.”
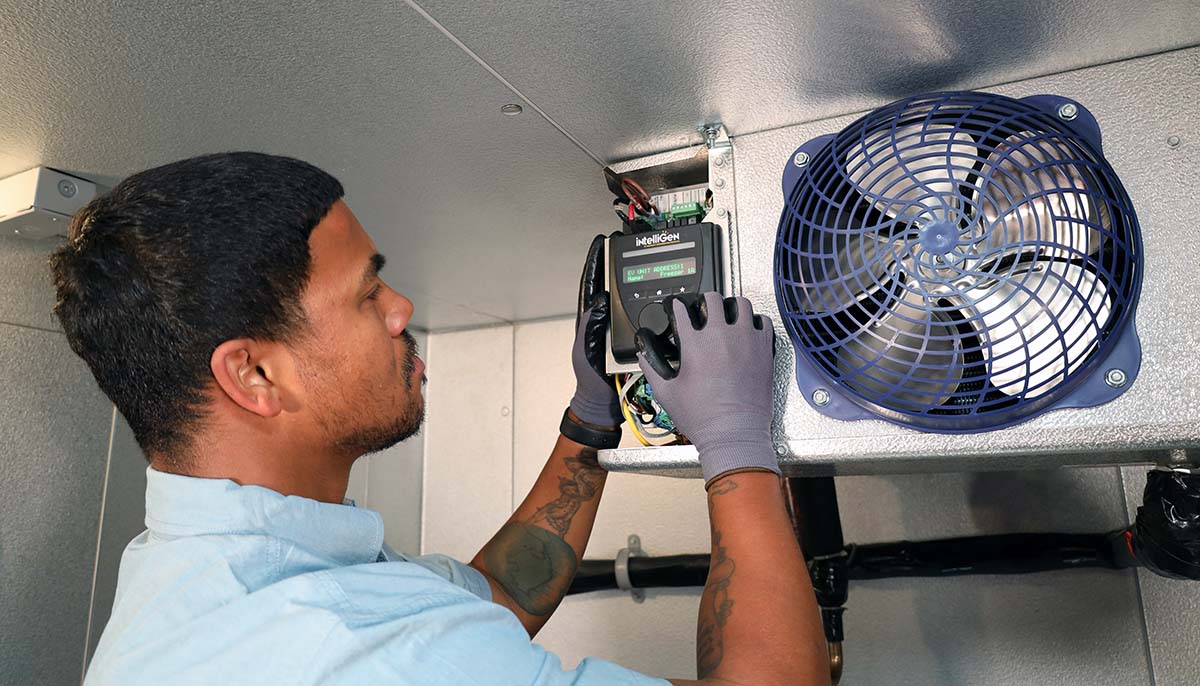
SAFETY FIRST: Contractors and technicians should be fully trained on how to work with alternative refrigerants, as safety is the top priority. (Courtesy of Heatcraft)
Future Technologies
Looking toward future advancements, Copeland anticipates that lower-GWP systems will take the lead as the primary technologies in the commercial refrigeration sector. In making this refrigerant transition, said Knapke, it is likely that manufacturers will conduct evaluations for full-system improvements, which could include energy-efficient, variable-speed compression technologies, which have been underutilized in commercial refrigeration.
“Connected technologies that leverage the internet of things (IoT) will also likely become more commonplace — simplifying system complexities, automating performance management, and opening opportunities for grid interactivity and load shedding,” said Knapke.
Danfoss also believes that IoT connectivity, along with cloud technologies, remote monitoring, and artificial intelligence are trends that will change the industry, said Gangemi. He noted that these technologies are expected to lend to better equipment performance, faster responsiveness to failures, and predictive maintenance.
“Capturing and reusing heat created as a byproduct of refrigeration systems is a trend that is also expected to grow,” he said. “Heat recovery units that capture this heat can be deployed and then used to heat water and space heating needs.”
As the industry continues to develop new and improved energy-efficient technologies — especially for CO2 — Harren expects to see advancements in parallel compression, adiabatic gas coolers, ejectors, and pressure exchangers. “Zero Zone is also exploring alternative low-GWP solutions utilizing propane units that offer more of a plug-and-play approach,” he said.
Heatcraft believes that the increased popularity of CO2 and propane will likely come about as regulations tighten and standards start allowing larger charge amounts of flammable refrigerants.
“Consider the possibility of CO2 becoming the norm, particularly in food retail, in the coming five to 10 years,” said Bolaños. “Nobody has a crystal ball, but watch for developments in federal and state laws and regulations that provide compelling indicators one way or the other.”
Contractors Are Key In Refrigerant Transition
When it comes to helping food retailers manage their existing refrigeration systems, as well as choose new low-GWP systems, Kurt Knapke, vice-president solution strategy at Copeland, has the following advice:
Contractors need to be prepared to help their retail customers evaluate their end-of-life equipment strategies and prioritize which systems need to be replaced or remodeled first. For legacy systems that will be in operation for many years to come, contractors will need to make sure to follow refrigerant management best practices. This starts by making the most of their existing HFC supplies by properly recovering and reclaiming refrigerant when working on legacy systems. In addition, it will require making sure that proper leak detection devices are installed on legacy equipment to minimize leaks, reduce greenhouse gas (GHG) emissions, and ensure peak system performance. Contractors play an integral part in helping to lower the food Retailer Scope 1 emission by finding and eliminating refrigerant leaks.
Contractors will also need to help their retail customers decide whether to repair their existing systems or replace them with new, lower-GWP systems. Lower system charges are driving the move away from large, centralized architectures toward more distributed systems. As a result, contractors and system designers may begin the transition by looking for underperforming sections of existing systems and gradually replacing them with a new, lower-GWP system, such as an A2L remote condensing unit. If a complete store remodel is in order, then a CO2 transcritical booster system may serve as a full-system replacement. Standalone R-290 units will continue to provide flexibility in retailers’ refrigeration portfolios, with the prospect of larger charges supporting even higher-capacity units.
What is important to note is that unlike legacy refrigeration technologies, there is no one-size-fits-all architecture for the next generation of food retail refrigeration. Although retailers will need to balance all factors in the decision-making process when selecting their next-generation system replacements or remodels, total cost of ownership is not always the deciding factor. Sustainability initiatives and operational preferences must be considered for the long term.
Report Abusive Comment