This article is intended to clarify and explain the operation of X13 ECM Motors that are currently being used in some HVACR equipment. Generally speaking, there are three motor types being used in air moving equipment.
- Permanent split capacitor (PSC) motors — constant speed motors;
- Electronically commutated motors (ECMs) 2.3 variable-speed motors — constant airflow motors; and
- X13 ECMs — Constant Torque Motors.
PSC motors rely on the rotating magnetic field that is generated by the applied alternating voltage and corresponding alternating current to turn the rotor. The magnetic field rotates at 3,600 rpm (60 cycles per second). The rotor speed is determined by the number of poles or windings in the motor field.
Rotor Speed = 3,600 / number of poles x 2
This equation defines the applied speed of the rotating magnetic field, also known as “synchronous speed.” Because of mechanical losses and the load applied to the rotor, it’s impossible for the rotor to spin as fast as the magnetic field, thus the operating speed of the motor is something less than synchronous speed. For instance, the synchronous speed of a 6-pole motor is 1,200 rpm, while the actual rotor speed may be 1,075. This difference is referred to as “slip.” A blower moving more than the rated amount of airflow (more load) will cause the rotor to spin somewhat slower than the rated 1,075 rpm. Blocking air (raising the static pressure) to the blower results in less load on the blower. Reduced load applied to the rotor allows the rotor to try to catch up with the rotating magnetic field resulting in greater speed (less slip). Thus the PSC motor varies its speed a small amount with respect to load. The resulting speed change experienced by the rotor needs not be considered in this discussion. In fact, PSC motors are commonly referred to as constant speed motors because the speed is primarily determined by the number of poles in the windings.
PSC motor summary: These are constant speed motors and react to changes in static pressure as follows.
Low static pressure equals more airflow. More static pressure equals less airflow. Because the motor can’t respond to changes in static pressure, too much static pressure results in such a drastic loss of airflow that problems can be expected. Refer to the PSC motor curve (Figure1) showing the wide variations in airflow that occur related to changes in static pressure.
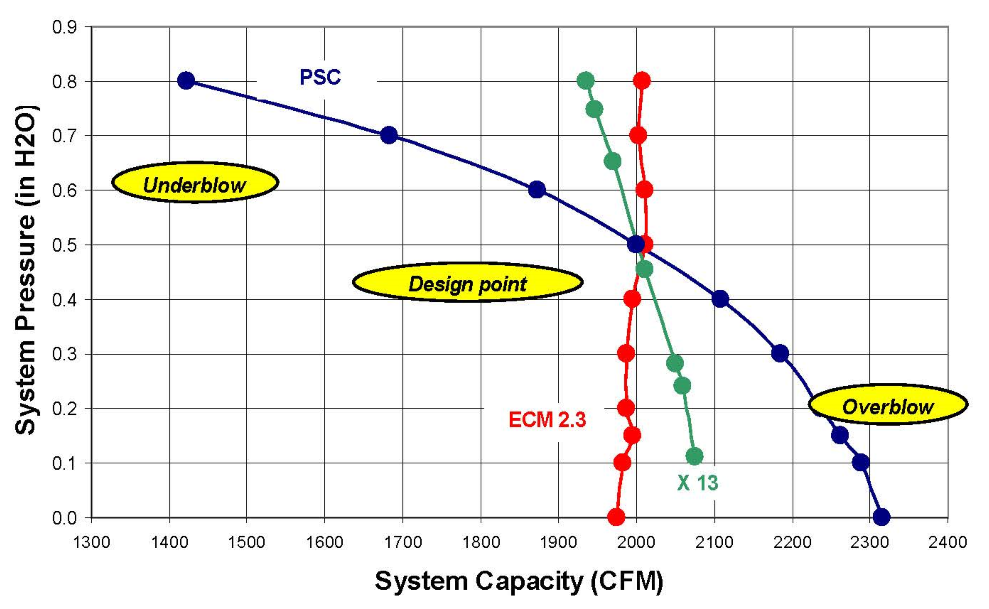
Figure 1, click to enlarge.
PSC MOTOR CURVE: A PSC motor curve showing the wide variations in airflow that occur related to changes in static pressure. (Courtesy of cfm Distributors
The ECM 2.3 variable-speed motor is also known as a constant airflow motor. It is a direct current (DC) 3-phase motor that is programmed with specific information related to the air-handling unit (furnace or air handler) within which it is operating. It looks at torque, rotor speed, and power to determine how much air it is moving and is able to compensate for slip. The rotating magnetic field is commutated electronically, can be increased or decreased as needed to maintain correct airflow, and is able to do so over a wide range of static pressures. As static pressure increases, airflow decreases. This reduction in airflow results in less work.
Since the motor is looking for a specific amount of work to do (airflow), it increases its speed until the correct amount of work is being done. This operation has resulted in the term “variable speed” because the motor varies its speed as needed to maintain the expected amount of work (airflow) it’s programmed to do.
Because it’s electronically commutated, it can start slowly and ramp up gradually to its operating speed and ramp down slowly when shutting off which contributes to very quiet operation. Because of its extensive programming capabilities and its ability to respond to multiple inputs and deliver a wide range of airflows based on those inputs, this motor must be used in equipment requiring wide ranges of airflow, such as modulating furnaces. There is other unique programming that won’t be addressed in this discussion.
ECM 2.3 variable speed constant airflow motor summary: As static pressure increases, airflow decreases. Because the motor is programmed to move a specific amount of air, it increases its speed to overcome the static pressure until the correct amount of air is moving. This is possible because of the extensive amount of programming placed into the motor module and its unique ability to actually determine how much work is being done by the rotor. ECM 2.3 variable-speed motors are able to continually move the correct amount of air by varying their speed regardless of static pressure up to their operating limit of 0.8 inch wc.
In addition, an ECM 2.3 variable-speed motor can respond to many different inputs to vary its airflow as required. Refer to the ECM 2.3 motor curve in the attached graph showing cfm remains constant over a wide range of static pressures.
The X13 ECM constant torque motor is a DC 3-phase ECM and generally operates as efficiently as an ECM 2.3 variable-speed motor. Because it’s an ECM, the X13 can ramp slowly up or down like the ECM 2.3 variable-speed motor. It doesn’t have nearly as much programming capability, thus it can’t respond as drastically to changes in static pressure. It is only programmed to look at torque and can’t fully compensate for slip. There are five possible speed commands available to the motor. These are preset at the time of manufacture and are easily changed in the field if necessary. Each of those five speeds has a specific torque value programmed into the motor for each speed selection. Torque is programmed based on an average expected static pressure of 0.5 inch wc. As static pressure increases, airflow decreases, resulting in less torque on the rotor. Because it’s an ECM, it can increase the speed of the rotating magnetic field, which results in the rotor turning faster. The motor responds only to changes in torque and increases its speed accordingly but can’t respond to speed or power thus it isn’t able to maintain full airflow such as the ECM 2.3 variable-speed constant airflow motor would.
X13 ECM constant torque motor summary: As static pressure increases, airflow decreases, resulting in less torque on the rotor. The speed of the rotating magnetic field is increased until programmed torque is achieved.
The X13 ECM responds only to changes in torque; thus it can’t vary its speed as much and can’t maintain the constant airflow exhibited by the ECM 2.3 variable-speed motor over the wide range of static pressures. Since it’s limited to five inputs, the X13 ECM can’t be used in air-moving equipment requiring wide ranges of airflow, such as modulating furnaces. In addition to lower initial costs versus the ECM 2.3 variable-speed motor, the X13 ECM provides very efficient operation and works very well in single stage- and two-stage equipment, where specific operating speeds (high, medium high, medium, medium low, low) can be selected to achieve required airflow.
Report Abusive Comment