
Overall, one of the first considerations, stated Mike Markarian, vice president and director of education of the New England Fuel Institute (NEFI) and also director of education for the National Oilheat Research Alliance (NORA), is that “You need sufficient combustion air. From a safety standpoint, that is most important.”
He noted, “Since homes are much tighter now, this is much more critical today. A lot of companies are bringing in outside combustion air.”
Ron Beck, manager of training, Burnham Corp., Lancaster, PA, remarked, “Size the boiler properly with a heat loss calculation. I personally do not like the connected load calculation for hot water boilers because it really does not matter how much radiation is connected to the system. The radiation works on water temperature. If the boiler size is smaller than the radiation output, it will only improve comfort but must be piped with a boiler bypass. This will allow lower radiation temperatures on warmer days and the water temperature to the system to reach high limit as the weather gets colder.”
According to Scott Dam, technical service for ECR International, Utica, NY, manufacturer of Dunkirk, Pennco, Ultimate, and Utica brand boilers, “I like to suggest a double oil filter, whether it is on a new install or a replacement unit. Older oil tanks are a problem in the field, and it makes a better application to install two oil filters on the system.
“Install a filter at the tank (felt or a micron style) and another at the burner. My suggestion is a good quality micron-style filter at the burner location. A double filter will catch items that could get through a standard felt filter at the tank. For a few extra dollars and the few fittings to install it into a system, it helps keep the nozzle free from foreign material.”
Peter Desens, corporate technical service manager for ECR International, added that it’s important for installers and technicians to “follow manufacturers’ instructions.”

KNOW YOUR CODES
Regarding clearance for a boiler and piping, Desens said, “Clearances for boilers vary by manufacturer; there is no typical dimension. Clearance for pipes is one inch.”As for clearances from combustible material, such as proximity of a fuel tank to an oil burner, Markarian cautions that local codes are different around the country. “You should check with local inspectors,” he recommended.
Looking at piping installation, Dam notes that it’s important to properly size piping and provide “a clean, neat, professional installation.”
“Most manufacturers today will want the circulator mounted on the supply pumping away from the compression tank,” Beck related.
Should you use a low-water cutoff? This also can be a matter of code.
“Low-water cutoffs are currently required by at least two states, New Jersey and New York,” said Desens, “and should be used in others (per manufacturers’ instructions) if the boiler is installed above any of the heating elements, i.e., baseboard or radiant tubing.”
Rich Simons, residential oil/hydronic business director, Honey-well Automation and Control Solutions, Golden Valley, MN, stated, “The low-water cutoff is being mandated state by state and its requirement is increasing. We would recommend it in any installation.”
Markarian said that low-water cutoffs should definitely be used on all steam boilers and that, over time, he believes states will adopt their use on forced hot water systems. “If you’re going to err, err on the side of overprotection,” he declared.

PROPER VENTING
When it comes to venting, Desens commented, “The oil-fired industry unfortunately is behind the gas-fired industry in this regard. The National Fuel Gas Code (NFGC) for gas equipment installations has specific guidelines for proper venting of gas products. The oil industry relies on NFPA 211 (Standard for Chimneys, Fireplaces, Vents, and Solid Fuel-Burning Appliances) and NFPA 31 (Standard for the Installation of Oil-Burning Equipment), neither of which are as specific as the NFGC for gas appliances.”To ensure proper venting, Beck indicated, “Slope the smoke pipe uphill at least 1¼4 inch per foot and make sure each oil appliance has its own barometric draft regulator mounted in excess of 18 inches from the boiler. It should always be mounted in the path of flue gases.”
To avoid condensation, “Make sure the unit has the proper firing rate,” said Markarian. “Some people think they gain efficiency by using a lower firing rate. If you under fire, you can run into condensation problems.”
For boiler start-up, “Check all the safeties, make sure there are no oil leaks, and watch the electrical priority. Always do a complete combustion test and set draft and CO2 to manufacturer specifications,” Beck said.
“For oil-fired equipment, always set the burner using instruments,” stated Desens.
Markarian concurred that for burner adjustment, “You have to use instruments. You cannot set burners by eye.” He explained that for flame retention burners, when you try to set it up by eye, you can have smoke that can’t be spotted visibly. “All burner manufacturers will tell you that you need instrumentation.”
Beck noted that the technician should “check the burner head adjustments, pump pressure, and pump vacuum if in a lift situation.” Also, he said, verify that the system pressure and the air charge in the diaphragm tank match. “The system pressure should not change more than 5 psi from a cold start to high limit. Set the aqua-stat settings to match the application you have.”
“The system should be run through several operational cycles at start-up,” pointed out Simons.
“A lot of information can be inferred from the temperature/pressure gauge. For instance, if the temperature increases too fast, then insufficient water flow exists. With a portable thermometer, the technician should see between 20 and 30 degrees of temperature drop between the boiler inlet and outlet and across any radiation device. Failure to observe this condition indicates insufficient water flow or air entrapment.”
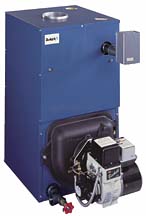
A CLEAN MACHINE
To provide a clean boiler system, “Clean the system with an appropriate compound per the manufacturer’s instructions,” said Beck. “Check for a neutral pH level when done. Pipe the boiler to ensure good air elimination. Oxygen will cause the interior walls of the boiler to corrode and cause early failure.”For a steam boiler, a clean system is essential. “You will want to make sure the piping system (steam pipes and all returns along with the radiators) are flushed out prior to connection to the boiler,” Dam said. “Proper cleaning of the boiler’s interior needs to be done to ensure removal of oils and residue from inside the boiler for proper steam production.”
For residential applications, Markarian stated, water treatment chemicals are normally not used. “A clean system filled with fresh, clean water is usually the best,” agreed Desens.
For more information, visit these websites:
Publication date: 12/16/2002
Report Abusive Comment