
That explains why their jewel, the Orange County Convention Center, is undergoing a massive expansion project which will increase the total square footage to 6 million, making it the second largest convention center in the world, next to Chicago’s McCormick Place. But that status could be up in the air, according to Joe Head, hvac supervisor for the convention center.
“We might be fighting for second with the Las Vegas Convention Center, depending on what they are doing now,” he joked.
Head, who has been in charge of the hvac department for the past 10 years, and his staff of 22 technicians currently maintain the building facilities, which have changed continually since Phase 1 was completed in February 1983. Since then, three more phases have been added, and Phase 5, titled the North/South Complex, the newest generation, is scheduled for completion in March 2003.
Head has worked and lived in Orlando since before the opening of its biggest attraction — Disney’s Magic Kingdom — and he is awed by the growth.
“I have seen amazing growth,” he said. “The traffic is a nightmare around here, in particular the truck traffic around the construction sites. But you learn to deal with it.”
Head said that the current convention center is cooled with 17,000 tons of a/c equipment. In contrast, the average home is cooled by three tons. There are 15 chillers, ranging in size from 600 to 1,200 tons, and over 500 air handlers. For a/c purposes, the convention center uses approximately 19 million gallons of water each month.
The complexity of the systems requires constant monitoring and service.
“We run three shifts during each 24-hour period,” said Head. “Because of the building’s automated system, I have operators and service technicians.
“The technicians run from Level 1, basic maintenance mechanics, to Level 4 technicians, who are actually electronics technicians. It’s important to have skilled electricians because we will be upgrading our building management systems with the next Phase 5.”
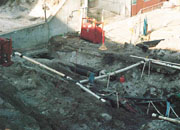
MANUFACTURER HELP
Head is also happy with help beyond what his staff can provide, namely from his chiller manufacturer. “Trane has been very big for us,” he said. “I’ve been a big fan of Trane. They have been a good supporter, even when I have needed them at 2:00 or 3:00 a.m.”Head said his staff needs to supply 24-hour a/c for conventions, which feature food and computer equipment — equipment that requires lower ambient temperatures and constant monitoring. In the event of an emergency power failure, there are seven generators in the dock area.
Head said there have been a few memorable “incidents” that have required special attention from his staff. One such event occurs on an annual basis.
A floor covering trade show comes to Orlando every year. During the show, tile-cutting equipment is demonstrated. The dust raised from the cutting is thick and potentially dangerous to breathe, so the hvac crew has the air handlers and filters working overtime to clean and clear the air.
Speaking of filters, there are over 15,000 in the building.
Fortunately, the air handlers are covered by a preventive maintenance program called MAXIMO, and regular maintenance is scheduled on a weekly or monthly basis.
BUILDING SECURITY
The hvac staff also monitors the building security equipment, including the more than 10,000 sprinklers and 6,500 smoke detectors. Head said that the center averages 10 to 15 alarms per month, often because “someone will inevitably strike a sprinkler head.”He added that building security has beefed up dramatically since Sept. 11, and he is happy with the presence of more security personnel. But the building’s design causes problems.
“The dilemma is that the building is so wide open and there are lots of accesses to the building. That’s how it was designed.”

FUTURE PLANS
With the addition of another 2 million sq ft of convention floor space, the staff of 22 will be taxed to keep up with demand for its services. Head said that currently his staff performs approximately 110 work requests each month. The additional equipment will require a bigger staff.“We are looking at 101 new air handlers in Phase 5,” added Head. “And these aren’t the small fancoil types, either.”
To meet the staffing demands, Head will again turn to the local votech schools for students and professionals from other businesses in the area.
“It’s tough to get real good people because of the government guidelines we must follow,” he said. “We are limited to what we can offer [in salaries and benefits] compared to the private sector. But our people like the benefits we offer.
“We are looking at challenges to staffing the new building, especially since Disney is always hiring in this area.”
The convention center’s expansion plans include a unique partnership with the Orlando Utilities Commission (OUC) in the creation of a chilled water district. The projected participants in the district include both the North/South and West Complexes of the Center, Lockheed Martin’s Facility and three planned high-rise hotels.
OUC contracted S.I. Goldman Inc./Comfort Systems USA of Orlando to install 36-in. supply and return lines from the existing center’s central energy plant to the Martin plant. This involved several miles of piping, some of which had to be run through the center’s existing parking garage and across busy roadways — not an easy task. Goldman is also constructing a 16 million gallon aboveground storage facility, which will be an integral part of OUC’s plan.
Head said that one unique problem involving the many different phases is the actual design work. He noted that different design architects were used for the various additions, creating a challenging problem of tying all of the systems together under similar controls. But he hopes that future building management systems will alleviate the problem — along with well-trained service technicians.
Head said that his staff strives to keep a constant, comfortable temperature in the buildings. He knows that there will be special requests, noting that some shows begin at 5:00 a.m. and run through 11:00 p.m. And he can also expect a degree of job security — some bookings have been taken for 2025 — which explains some of his job satisfaction.
“The job is a real challenge; there is always something happening,” he said.
Publication date: 05/13/2002