The HVACR industry is currently undergoing another significant refrigerant transition. In contrast to the prior transition from nonflammable (A1) HCFCs like R-22 to also nonflammable HFCs, notably R-410A, the latest generation of refrigerants includes mildly flammable alternatives such as R-32 and R-454B, categorized as A2Ls.
Fortunately, the compressors utilized in these A2L systems closely resemble those found in A1 systems, which means that contractors and technicians won't face a steep learning curve when dealing with these components. And if they are already utilizing best practices during the service and installation of A1 systems, they are not likely to see many differences when it comes to working on A2L systems.
Senior technical trainer
Copeland
Compressor Design
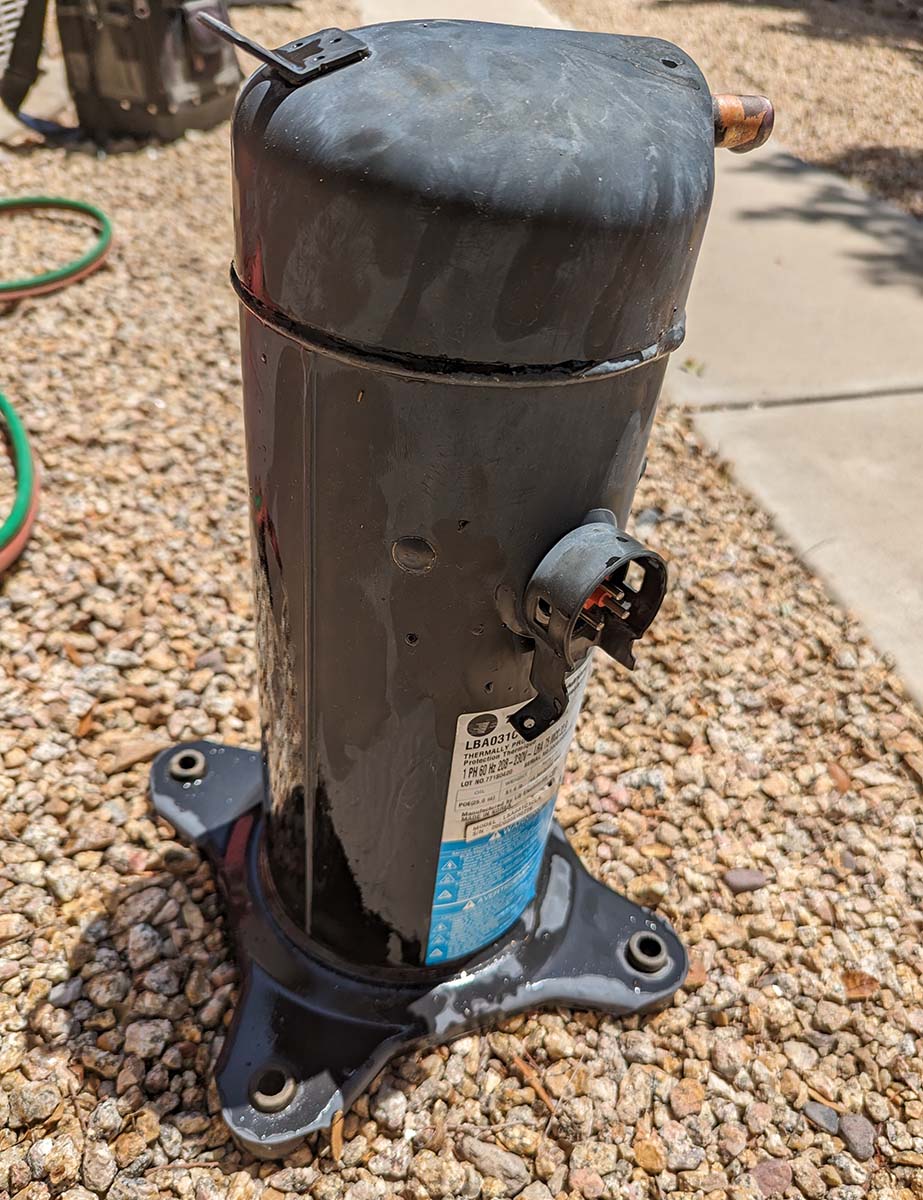
SIMILAR COMPONENTS: The compressors utilized in A2L systems closely resemble those found in A1 systems. (Staff photo)
Most of the internal mechanisms and materials used in A2L-optimized compressors are very similar to legacy A1 units, said Jeff Kukert, senior technical trainer at Copeland. While A2L-based systems offer improved leak mitigation and detection capabilities, the primary distinctions in design pertain to electrical components, including those found in compressors and condensing units, such as:
- Relays/contactors and/or devices used for switching electrical currents on/off;
- Controllers;
- Variable frequency drives (VFDs); and
- Electrical enclosure (box) within which a full system may be contained.
“When using lower-flammability A2L refrigerants, electricity sparks or charges could be potential sources of ignition upon contact with a flammable concentration of gas,” said Kukert. “Compressor manufacturers must qualify electrical componentry for safe use with A2L refrigerants per applicable testing procedures and safety clauses, such as those defined in the Underwriters Laboratories (UL) 60335-2-89, 2nd edition product safety standard.”
In order to comply with those safety standards, technicians will notice that A2L compressors will be marked with warning labels and additional markings, said Michael Taras, senior director of engineering at Daikin Comfort Technologies North America. He noted that compressor oil composition and characteristics can be another design consideration.
“While A2L compressors employ the same type of oils as used by R-410A compressors, material compatibility of the refrigerant-oil mixtures with the compressor construction materials is one of the critical design considerations,” he said.
As for behavioral traits, compressors used with R-410A and the A2L refrigerant R-454B are quite comparable, said Jerry Edwards, senior manager of the sales engineering team at LG’s component solutions business unit.
“R454B has a lower refrigerant density, so to maintain capacity targets, the compressor's displacement must be increased by about 5% as compared to R-410A,” he said. “The discharge temperature rises by about 7℃ under high load conditions, which must be monitored during system-level testing, but the higher discharge temperature does not create a problem in the general operating range. These refrigerant properties lead to a demand for additional motor torque, which required all motors to be redeveloped, along with their matching internal overload protectors.”
The system level performance improvement of the A2L refrigerant, R-32, is on the order of 3% to 6%, in comparison to a similar system using R-410A refrigerant, said Taras. He added that R-32 is a single-component refrigerant, so the R-32 charging, reclamation, and recycling processes are often more straightforward than for the refrigerant blends.
Service and Repair
When it comes to installing or servicing A2L systems, HVACR contractors and technicians can still use many of their current tools. In general, tools that don't touch the refrigerant circuit — such as scales and non-electric hand tools (e.g., wrenches, pipe cutters) — can usually be used for both A1 and A2L systems. However, most of the electronic tools and testing equipment must be rated for use with flammable refrigerants, as this prevents the possibility of a spark during operation.
For example, all the refrigerant in an A2L system must be recovered utilizing equipment designed for this refrigerant and for this purpose, with no sources of ignition, said Sanghyeon Ji, senior manager of the research and development team at LG component solutions business unit.
“In addition, the service area should be well ventilated as a precaution against any refrigerant that may have leaked into the area. Never braze on a charged system,” he said. “And because A2L refrigerant is flammable, there is a risk of fire or explosion, so only personnel with qualifications or specialized training in the safety of flammable refrigerant should install the air conditioning system or perform service. These are all rules that should be followed anyway, but technicians need to be diligent with A2Ls.”
The same service rules also apply when dealing with compressor burnout, which can occur in any A1 or A2L system when the compressor operates outside its operating envelope for a prolonged period of time, said Sriram Venkat, senior director of engineering at Daikin Comfort Technologies.
“There are several reasons for this to occur, which include low charge due to refrigerant leaks, charging systems above the manufacturer’s guidelines, blocked heat exchangers, and outdoor fan motor failure,” he said. “Proper installation and periodic maintenance are the key to avoiding some of these situations. The consequences of compressor burnout are similar between the A2L and A1 refrigerants, and the general practices for cleaning and component replacement for A1 and A2L based systems are also similar.”
When faced with a potential compressor burnout, an acid test kit should be used to confirm the presence of acid in the system oil. Because the types of oil may differ among A2L-optimized compressors and systems, Kukert advises technicians to only use a manufacturer-recommended acid test kit that is designed for the type of oil used in that specific A2L compressor.
“Once a burnout is confirmed, the most important thing to do is to make sure that the acidic oil has been removed from the system to protect against damage to the replacement compressor, said Kukert. “Copeland recommends following the manufacturer’s recommended procedures as outlined in their application bulletin, which includes using only approved additives to remove acid from oil in the system.”
When selecting a replacement compressor for an A2L system, Kukert said technicians should make sure that it is optimized for use with the specific A2L refrigerant for which the system was designed and to ensure any modifications to the system necessary for A2L refrigerants are completed. When installing a new A2L-optimized compressor, Kukert suggests following the charging sequence as outlined below:
- Safely remove the A2L refrigerant, following local and national codes;
- Purge the system with an inert gas (e.g., oxygen-free nitrogen) to evacuate any traces of the A2L refrigerant remaining in the lines;
- Repeat the purge step an additional time for five minutes to ensure full evacuation;
- Check for refrigerant in the air using an A2L-certified leak detector;
- After ensuring all A2L refrigerant is out of the system, braze and open the circuit to make any repairs;
- With repairs completed, purge the system again with nitrogen;
- Pressure test the system to ensure that it is free of leaks per manufacturer recommendations;
- Evacuate the system again to remove any moisture, air, or non-condensable gas per manufacturer recommendations; and
- Charge the system per manufacturer recommendations and the system’s designated charge limit.
The bottom line is that when it comes to working with A2L compressors, technicians will find a reassuring similarity to the guidelines applied to A1 systems. The key is to follow industry best practices and heed the manufacturer's recommendations to guarantee that the system operates safely and as intended.
Report Abusive Comment