With the U.S. phasing down HFC production as part of the AIM Act, a lot of pressure is being put on the HVACR industry to better manage these refrigerants in order to prevent possible shortages. This primarily entails recovering and reclaiming refrigerants, which the Environmental Protection Agency (EPA) is relying upon to maintain existing equipment in the face of dwindling supplies of new refrigerant.
The problem is that the amount of reclaimed refrigerant isn't enough to meet the demand. Indeed, the rate at which HFCs are being reclaimed has only gone up by 6% since 2017, and in 2020, a tiny 1.6% of the HFCs sold were actually recycled and ready for reuse.
But there's some good news. To encourage more recovery, many reclaimers are no longer charging for mixed refrigerants, and they're paying more to those who bring in recovered refrigerants. This could actually turn into a nice money-making opportunity for contractors — but they can only cash in on these new terms if they recover the refrigerant in the first place.
Vice president of sales and marketing
Hudson Technologies Co.
Overcoming Barriers
Even though it’s the law, there are lots of reasons why HVACR contractors and technicians may not recover refrigerant at a job site. Possible reasons include not having the necessary equipment on-hand or lacking training on proper recovery procedures — or simply not understanding the regulations requiring refrigerant recovery. The most oft-cited reason for not recovering refrigerant, however, is that it takes too long. Technicians working on tight schedules may feel that the added time needed to recover refrigerant will affect their ability to finish the job quickly and move on to the next one.
Additional concerns include insufficient financial incentives for recovered materials and the imposition of fees for mixed refrigerants. However, this is starting to change, as reclamation companies are revising their policies concerning the acceptance of recovered refrigerants.
“Now that there are greater economics relative to the value of the recovered refrigerant, many of the financial barriers — including fees — have been removed, so contractors can turn recovery activities into a profit center and not a cost,” said Kate Houghton, vice president of sales and marketing at Hudson Technologies Co. “For example, contractors should significantly benefit from Hudson’s pay-for-all refrigerants approach, which is a more profitable buyback program than in years past.”
And while contractors may have been charged a fee for mixed refrigerants in the past, it’s important for them to know that every pound of recovered refrigerant has value now, and they should not pay disposal fees anymore, said Houghton.
“We pay for mixed refrigerants and have no disposal fees,” she said. “We have sophisticated fractional distillation that allows us to separate nearly all mixed refrigerants that we receive, allowing Hudson to provide payment to contractors even for low purity refrigerants.”
National Refrigerants also accepts all non-flammable refrigerants recovered from air conditioning or refrigeration systems, said Maureen Beatty, executive vice president of National Refrigerants. She added that they will also accept the new A2L refrigerants, as soon as AHRI Guideline K is updated for flammable recovery containers.
“National has generous acceptance specifications for recovered refrigerants, because we know that the contractor may not always know the type of refrigerant in the system they are servicing,” she said. “Many of these mixtures can be separated but, admittedly, some mixtures are a challenge. We believe that used refrigerants are a resource and rely on technological solutions, not destruction, when it comes to mixed refrigerants.”
Like many reclaimers now, National Refrigerants also does not have minimum return requirements for received refrigerant. Ideally, recovery cylinders should be filled to at least 50% capacity to maximize their utilization, said Beatty, but the quicker recovery cylinders are returned, the quicker they can be put back into contractors’ hands so they can keep recovering.
While the recommendation is to never mix refrigerants — indeed, it can be a safety risk — the reality is that refrigerants can and do get mixed for a variety of reasons, said Taylor Ferranti, commercial vice president of refrigerant management at A-Gas. When that happens, A-Gas works to process these mixed refrigerants back to the AHRI-700 standard to then be resupplied into the market to support the current install base.
“Once a refrigerant can no longer be reclaimed and reprocessed, we destroy the products in our PyroPlas plasma arc destruction units,” said Ferranti. “This technology is a United Nations-approved, TEAP-certified technology that delivers the industry’s highest guaranteed destruction efficiency (99.9999%). Contractors should not have to pay for refrigerant destruction services.”
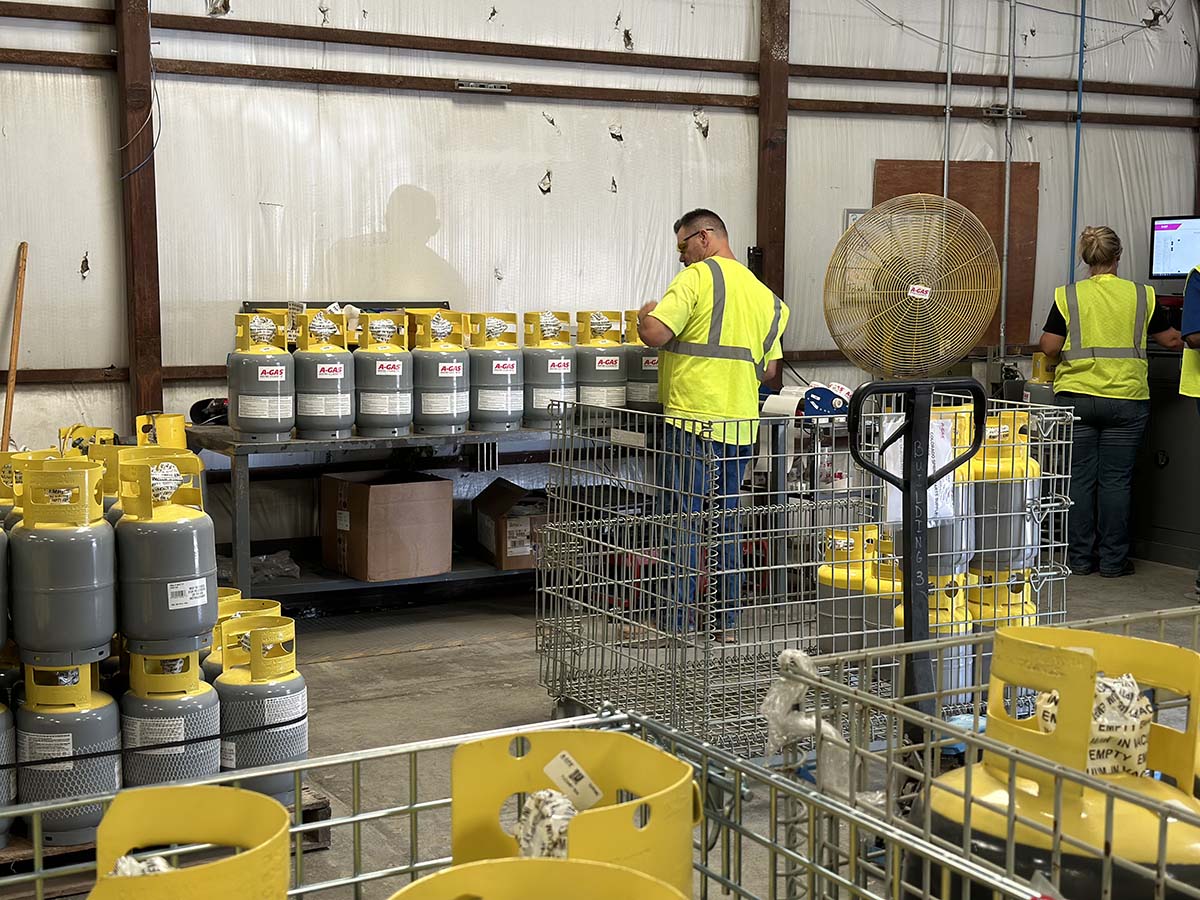
CYLINDER PREP: Reclaim cylinders are prepped for shipment to Refri-Claim partners. (Courtesy of A-Gas)
Offerings
Reclaimers are also making it easier for contractors to return recovered refrigerant. A-Gas, for example, accepts recovered refrigerants from both contractors and supply houses to ensure every pound of refrigerant possible is recovered and reclaimed for future reuse, said Ferranti.
“Across the country, we work with wholesale distributors to support their reclaim programs by making it easy and profitable for both the wholesaler and their customers to properly handle recovered refrigerants,” he said. “Distributors are collecting recovered refrigerant from their customers, and then it is picked up by our team and transported to our facilities for processing back to the AHRI-700 standard. In working with us to deliver recovered refrigerant, we provide product assurance for our partners.”
A-Gas also offers the Rapid Recovery and Rapid Exchange network, where EPA-certified technicians work with contractors — as well as grocery stores, hotels, schools, and medical facilities, etc. — to recover refrigerant on-site. The Rapid Exchange service is a simple swap program that provides contractors with empty, refurbished, vacuumed, and in-date hydro-tested cylinders ready to receive recovered refrigerant in exchange for their full recovery tanks. A-Gas also provides EPA documentation for every transaction, which protects technicians, as well as businesses, from potential liability, said Ferranti.
“Another benefit to contractors is speed: Our AHRI-certified recovery equipment is up to 10 times faster than traditional equipment,” he said. “This is especially helpful on large chiller or demolition jobs, or in the grocery and food retail sector when time and efficiency matter. Our Rapid Exchange service is also the fastest way to ensure a contractor’s fleet has vacuumed, in-date cylinders available to continue providing service to customers.”
At National Refrigerants, contractors can return their used refrigerant to one of their authorized distribution locations and get a receipt for the estimated weight returned. With over 400 locations throughout the U.S., Beatty noted that contractors can easily find a location to drop off their recovered refrigerant cylinder and pick up an empty one so that they can continue recovering refrigerants.
National Refrigerants also offers a reclaimed refrigerant banking program. The program started as an effort to support refrigeration and air conditioning equipment owners with the ongoing servicing needs of their CFC-containing equipment while they transitioned away from those refrigerants, said Beatty.
“What we didn’t know back then was just how important a role banking would become to the successful management of refrigerants as the industry transitioned from HCFCs to HFCs and now from HFCs to lower-GWP HFOs,” she said. “The program works similar to a bank — a customer deposits their used refrigerants at any of our 400 distribution locations and, after National reclaims it, they can withdraw it any at any of those same locations. This program provides them with the flexibility needed to efficiently and economically manage their refrigerant needs, while giving them the confidence in the quality of the reclaimed refrigerant.”
The recovery/reclaim process at Hudson Technologies is also simple and easy, said Houghton, as the company provides all the paperwork and makes pick-up arrangements for contractors.
“Once we receive a contractor’s cylinders, we refurbish and maintain them and return them empty, in hydro test date, cylinders within two business days of receipt to ensure contractors have cylinders to continue to perform recovery work,” she said. “This helps contractors avoid having to carry extra cylinders in their fleet. In addition, Hudson pays for the recovered refrigerant and all the shipping costs of the two-way freight. So hopefully we are achieving our goal of making everything easy and pay for all recovered gas so that the contractor wants to perform more recoveries.”
In addition, Hudson takes its proprietary reclamation equipment into the field to do recoveries and system remediation and retrofit work. This facilitates contractors and end users maximizing recovery and reclamation of refrigerant and preservation of system charges, while also helping restore energy efficiency and optimal system performance, said Houghton. The company also performs all types of refrigerant management services, including banking and cylinder maintenance services.
As HFCs are phased down and contractors step up recovering refrigerants, they may be looking anew at the various programs that reclaimers offer. In selecting a reclaimer, Beatty advises looking for those that are fully insured and will properly handle and dispose of the wastes, like oil and water, that are removed from their used refrigerants. She also suggests checking EPA’s website to make sure the reclaimer is certified: www.epa.gov/section608/epa-certified-refrigerant-reclaimers.
By working with a certified reclaimer, contractors will recognize the benefits that reclamation programs can offer to their business, both in terms of sustainability and their bottom line, said Ferranti.
“The AIM Act highlighted to the entire industry that we all need to work together to protect, safely recover, and reclaim refrigerants to ensure there is enough supply to service our customers and industry,” he said.
Report Abusive Comment