Recent advancements in smart technology have enabled HVAC equipment serving the indoor agriculture industry to optimize the conditions for crop growth. Grow rooms now can anticipate load changes and find the right balance between humidity and energy. Using cloud-based technologies, growers and HVAC technicians can take advantage of sensors to monitor humidity, carbon dioxide, light, and more.
Looking ahead, advancements in the HVAC side of indoor agriculture technology will only increase the ability to provide the hyper-precise control necessary for profitable crops.
vertical market manager
Daikin Applied
Get Smart
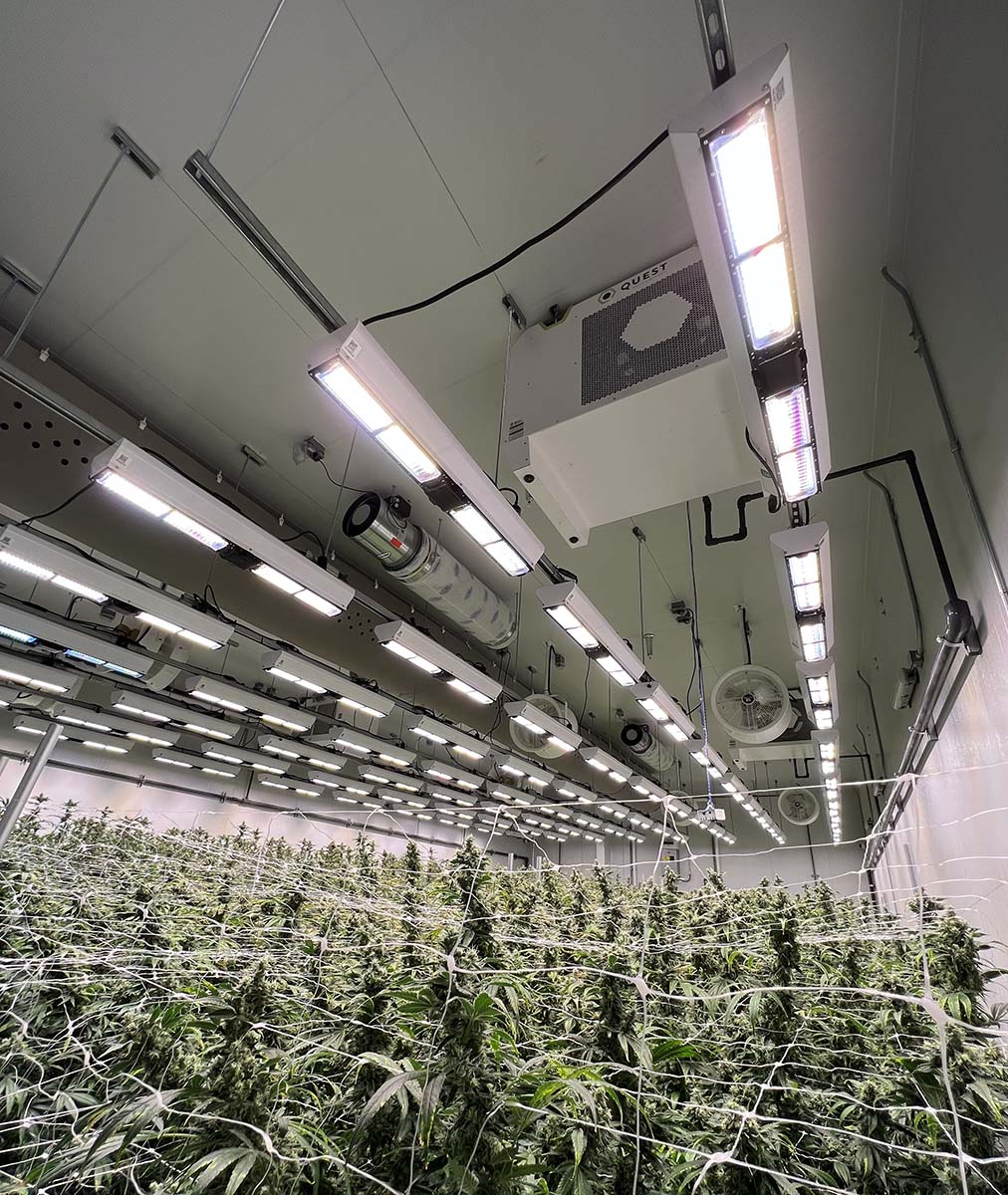
OPTIMAL: Smarter HVAC systems today allow for more optimal control of grow rooms. (Courtesy of Quest Climate)
Much of the advancement in this market can be attributed to the growth of the cannabis industry. The widespread legalization of marijuana and the cash it has generated has led to more money being poured into the market, creating the environment for equipment to be developed with more optimal control in mind.
“When indoor agriculture was in its infancy, proper HVACD systems did not exist to handle the unique and highly variable loads the application generates,” said Chip Seidel, controlled environment agriculture (CEA) brand manager, Desert Aire LLC. (The D in HVACD stands for dehumidification.)
That isn’t the case today.
“The CEA industry now has the resources to invest in better space conditioning equipment and the means to properly control it,” said Dan Dettmers, senior application engineer at Quest Climate.
Manufacturers have heavily invested in understanding indoor agriculture in order to develop these systems that help grow rooms thrive.
“We're adding features to allow the equipment to better meet the growth space needs, and anticipate drastic load changes in real time,” said Brian Rodeghier, vertical market manager with Daikin Applied. “It’s very different from comfort cooling applications — this is a process application. We need to manage load swings as best as possible with our equipment in the operation.”
From a smart HVAC standpoint, that’s something equipment is able to do now that it once wasn’t. Another advancement is the ability growers now have to meet or change the off coil temperature, resulting in more effective control of humidity without consuming more energy than necessary.
“That’s a key thing because I can force my equipment to work really hard and bring a lot of moisture up, but it's going to consume a lot of energy in doing that,” Rodeghier said.
There has to be the right balance between moisture removal and energy consumption, and smarter equipment today can achieve that.
“We're basically dynamically changing the equipment settings based off of the feedback that we're getting of what the grow space is doing, or changes that are coming, so we can make it more effectively control the space and do it with a minimal amount of energy,” Rodeghier said.
Equipment today has also been developed to be smart enough to plan ahead for those abrupt load changes it’ll have to handle.
“The ‘smarter’ controllers have added proportional, integral, derivative (PID) loops to automatically change system configuration to maintain control in an ever-changing environment,” Seidel said. “Just consider the impact of lights on vs. lights off on the internal load. Without PID loops, tight control is not possible.”
Cloud-Based
Since hyper-precise control of grow rooms is ideal, real-time, cloud-based control platforms — especially those that can track multiple variables and multiple rooms — have become an important feature of the grow industry, especially considering how many pieces of HVAC equipment is needed to maintain the perfect conditions.
An example of this is Desert Aire’s HVACD systems that are monitored through their AireGuard system.
“AireGuard allows authorized users visibility to all relevant room conditions, as well as the internal operation of the units themselves,” Seidel said. “This cloud-based visibility allows factory technicians to make system adjustments and tuning remotely to fully dial the equipment in for the most stable control and efficient operation.”
Whatever the smart control system, the type most beneficial to growers will be simple and able to provide easy to understand feedback on the conditions of the room.
“It needs to show conditions real-time with the ability to control the room remotely to respond to upset conditions, but it should also allow them to pre-program the controls to repeat their best practice growing conditions,” said Dettmers. “The smart controls systems that succeed … are developed through a collaboration of controls engineers and horticulturalists that understand the needs of plants.”
Dettmers said unless an HVAC tech has extensive experience working in other high latent load environments, they likely have not seen HVAC operating conditions like those in a CEA.
“A control system that records operating conditions and equipment run times can show an HVAC tech what the farmer wants out of their space conditioning equipment,” Dettmers said.
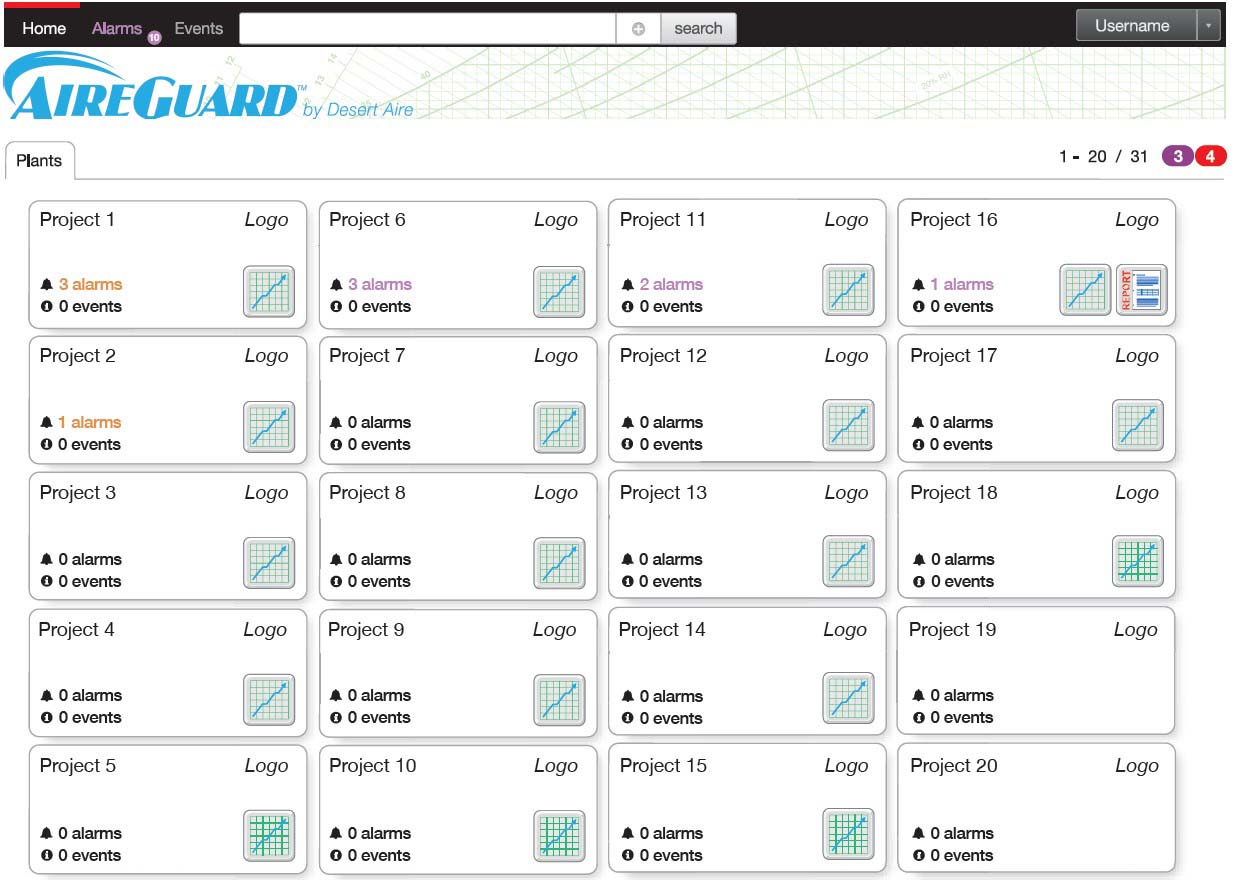
Click chart to enlarge
CLOUD-BASED: Desert Aire’s dehumidifiers can interface with a BMS that will control other key facility systems like lighting and irrigation and provide the cultivation team with a full facility system dashboard. (Courtesy of Desert Aire)
Benefits for All
While cloud-based systems are not all created equal, highly functioning systems might allow for technicians to reduce downtime through giving them the ability to perform diagnostics on differing parts of the system remotely.
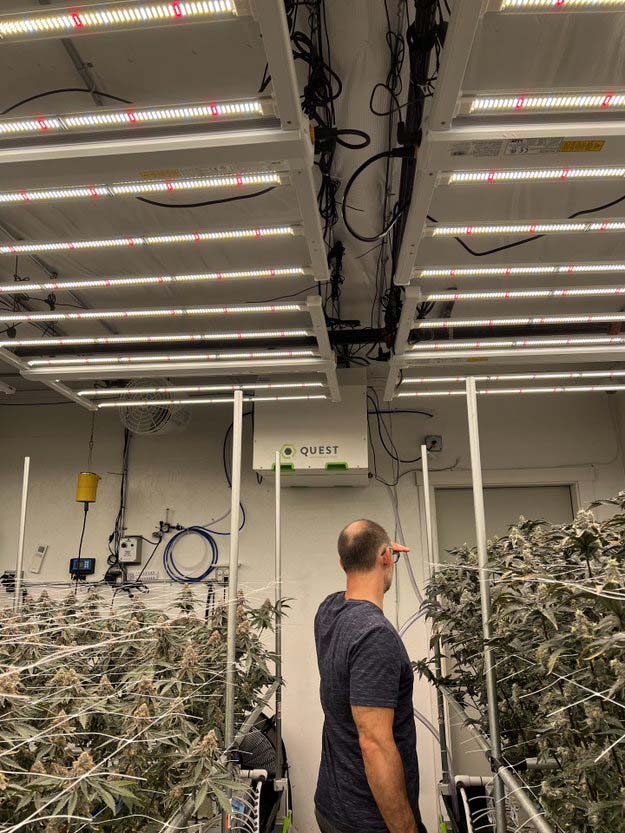
BENEFITS: Advancements in indoor agriculture benefit both growers and HVAC technicians. (Courtesy of Quest Climate)
“The technician can interface with the factory to obtain advice and recommendations for what to do for best control and operations,” Seidel said. “In addition, AireGuard allows for remote system tuning, right down to specific valve positioning, which is very helpful when working with cultivators to maintain the most stable environments possible.”
Even when the plants aren’t grown in coil, CEA is a dirty business, Dettmers said.
“Filters quickly load up, coils experience biologic growth, and ductwork can be coated in dust.”
This led Quest to design their new generation of equipment to monitor filter life, increase fans speed to offset a loaded filter, and notify the HVAC technician when the filter needs to be changed.
“Output from equipment like this helps the technician maintain the space conditioning equipment in optimal shape for the CEA operation,” Dettmers said.
What benefits the technician ultimately benefits the grower, too.
“It gives [growers] more precise conditions if we’re able to anticipate load changes, and also better able to maintain the equipment and make sure it's operating the way it should,” said Rodeghier.
Growers are able to not only increase yields but also control energy consumption with purpose-built integrated HVACD systems with cloud-based control systems.
“The cloud-based AireGuard system brings the cultivator, field technician, and the factory together to ensure the most stable control of both temperature and humidity levels and thus VPD. Stable VPD translates into higher yields and overall crop quality,” said Seidel.
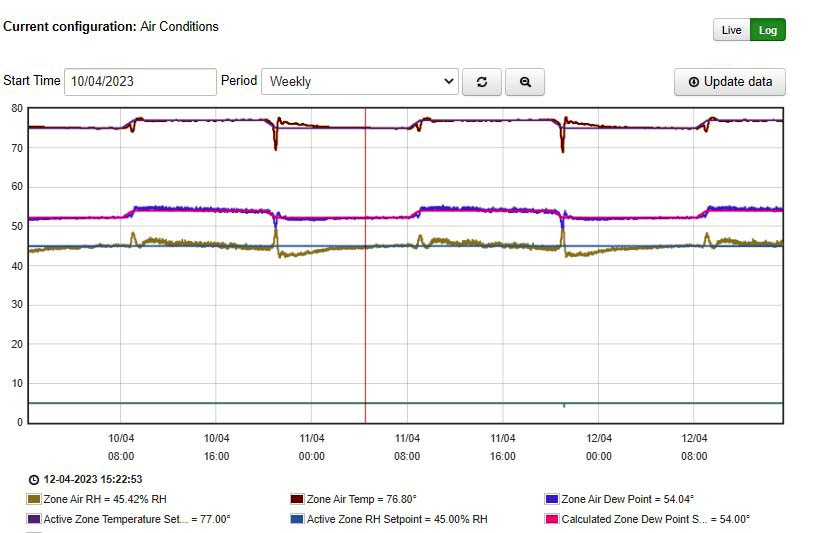
Click chart to enlarge
VPD: AireGuard brings the cultivator, field technician, and the factory together to ensure the most stable control of VPD: meaning higher yields and overall crop quality. (Courtesy of Desert Aire)
Improving
Looking forward, Rodeghier thinks there is still opportunity for growth with energy monitoring and how to reduce energy consumptions. While that information may already be provided, many growers may not be using it as effectively as they could.
Water, along with energy, plays a big role in the future the smarter technology and indoor agriculture.
“Both have a substantial impact on the profitability and sustainability of the sector,” Seidel said. “Many existing facilities are looking to upgrade their aging, inefficient, and hard-to-control equipment with purpose-built equipment controlled via cloud-based systems to bring all aspects of the grow operation together in one system, in an effort to improve their yields and reduce costs.”
And there’s opportunity for water and HVAC controls to work together.
“Under-watering is detrimental to survival of a plant, but over-watering adds humidity to the space and wastes a precious resource,” Dettmers said. “The next generation of smart control systems will monitor light levels to adjust watering rates, which will then adjust the HVAC system to only remove the water necessary to maintain optimal conditions.”
Something else manufacturers are already working on, Daikin included, is to include predictive analytics.
“In that case, the system has built-in fault protection and can make recommendations for any predictive maintenance, which might include what condition the air filters are in, if the cooling coil is getting dirty, anything that will keep the system up and running as efficiently as possible that the system can check and do some diagnostics … and alert the person ahead of time if they see any unusual conditions,” Rodeghier said.
Report Abusive Comment