lead applications engineer
Trane Technologies
An air-handling unit (AHU) is a major component of the HVAC system in many large commercial properties, providing ventilation and moving treated air throughout the building for occupant comfort.
But an AHU, designed properly, run strategically, and equipped with the right accessories, can also be a focal point for HVAC system energy conservation, say engineers at major manufacturers.
“You can have a high-performing air-handling system without sacrificing comfort and without sacrificing energy usage,” said Eric Sturm, a lead applications engineer at Trane.
The Right Design
Engineers should start, experts said, by understanding the building or building expansion in question and its intended uses as well as characteristics such as its size, the R-value of its insulation, the amount of air leakage, and the climate in its location, before designing an air-handling system for it.
“What the engineer does is take a look and understand the building, understand what the usage of the building is, and then also understand ... the expectations of the owner,” said Derrick Paul, a mechanical engineer and director of commercial sales at Fujitsu General America. “Are they looking for individual control? Are they looking for large areas, with very little individual control throughout the space?”
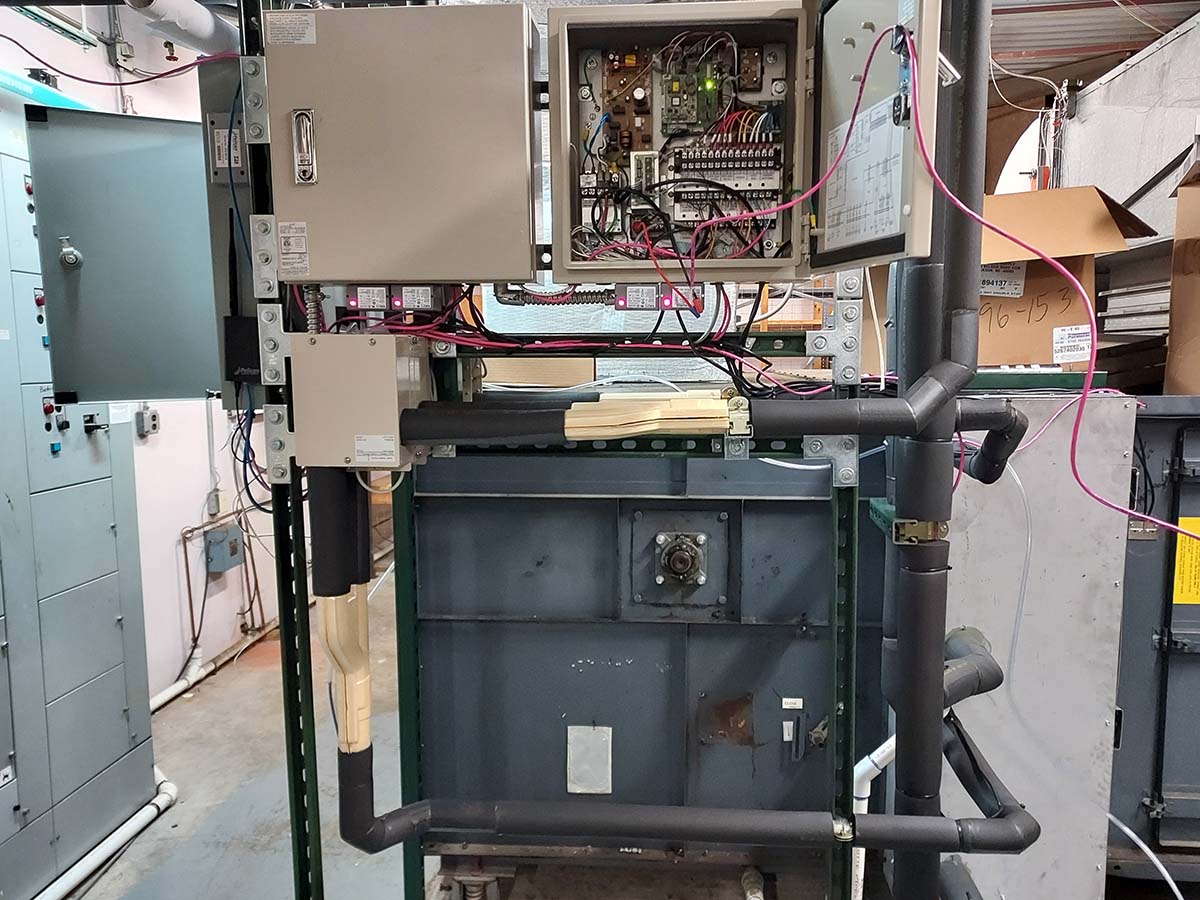
DIRECT EXPANSION: A Fujitsu DX kit, and associated controls, for the adaption of a 20-ton air handler to work with Fujitsu heat pumps. (Courtesy of Fujitsu General America Inc.)
Sturm said that the use of whole-building energy-analysis software could help.
“It really comes down to the design engineer,” said Maria Acosta, a commercial engineer at Rheem Manufacturing Co.
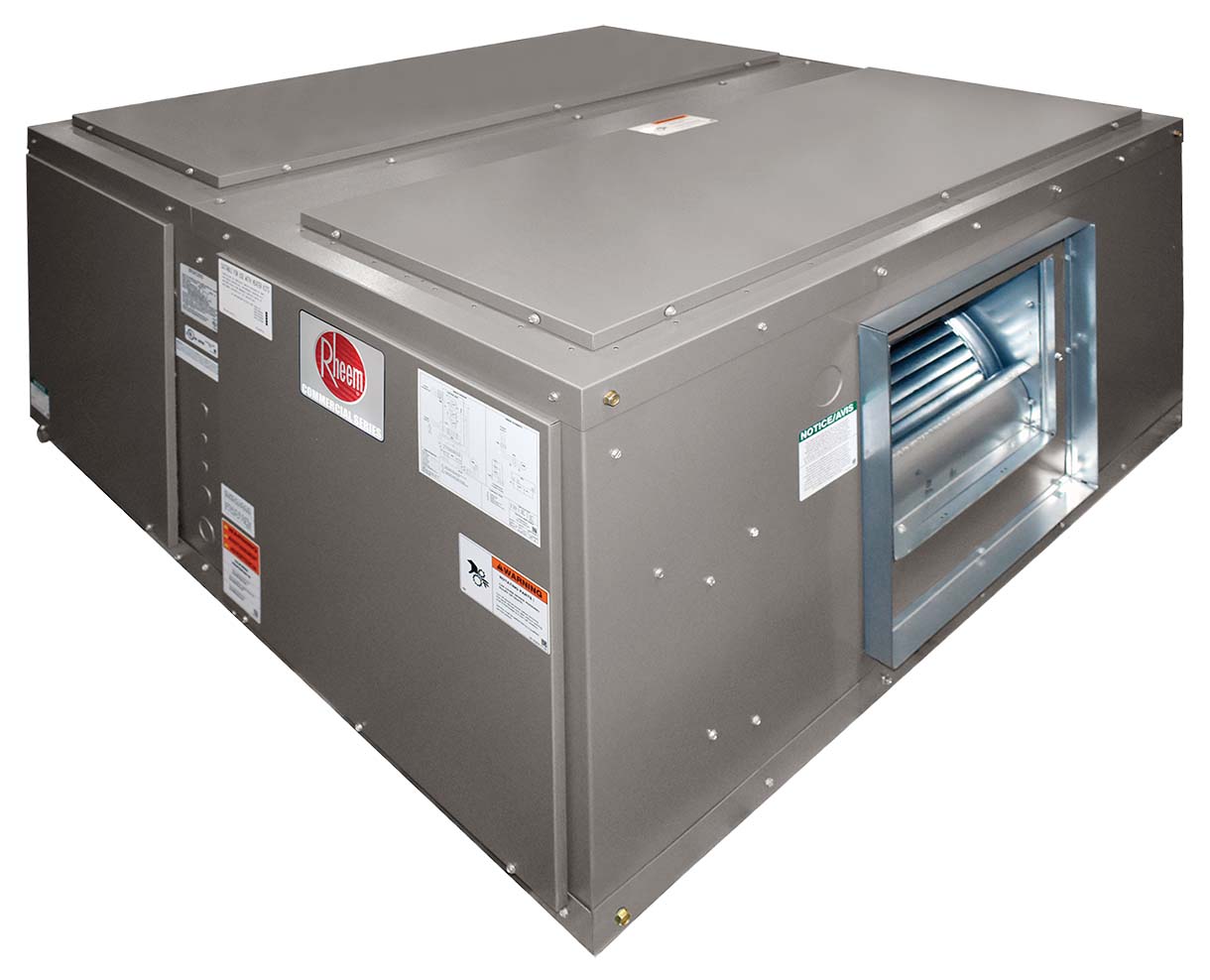
THE HEART OF FORCED-AIR HVAC: A Rheem commercial air handler with heat-pump operation and a centrifugal fan. (Courtesy of Rheem Manufacturing Co.)
ASHRAE Standard 90.1, first introduced in 1975 and updated many times since, sets out minimum requirements for the energy-efficient design and construction of most types of commercial buildings and their systems, as well as for the expansion of commercial buildings and the replacement of existing HVAC equipment in older buildings. Best practices, said Sturm, call for meeting or exceeding those minimums.
“My recommendation is always to look at the entire system when making energy-efficiency choices,” Sturm said. “Sometimes it makes more sense to run one piece of equipment harder and use more energy on that equipment because it’s more efficient compared to a different piece of equipment.”
A system with multiple zones, Paul said, could allow for energy savings by giving building managers and occupants a greater degree of control, allowing them to shut down or set back conditioning in unoccupied areas or when less of it is needed. Employing variable air volume, which customizes air distribution in different building zones, can also save energy, he said.
“This is good technology when the air-handling unit is sourcing more than one zone,” Acosta said.
Building owners and managers looking for maximum energy efficiency should be prepared to pay for it.
“It’s proportional,” said Acosta. “The more efficient you want your system, the more expensive it’s going to be. Efficiency costs money.”
Controls Count
The right AHU controls can make all the difference, factoring in occupant needs, occupancy levels at different times of the day, weather conditions, the various uses of the building, and other factors in controlling how and when to run an AHU.
“High-performance control algorithms can make a significant impact on energy savings,” Sturm said. Such controls might employ tactics such as optimal stop and start, fan-pressure optimization, or, when outdoor conditions are favorable, a night purge, he said.
A night purge, Sturm said, is a type of airside economizing that brings cooler nighttime air into a building in which the temperature has risen during its unoccupied hours. This free-cooling strategy essentially pre-cools the building, without having to start up cooling equipment, before the building opens for business again.
“In preparation for the following day, we can use night purge to get the temperature in the space from 80 back down to 75. Or probably even a little bit cooler, maybe like 73°,” Sturm said.
“It’s over-ventilating, but it’s over-ventilating for a purpose,” Sturm added. “And the purpose is to reduce or eliminate the mechanical refrigeration energy.”
A night purge should be used judiciously, however; Sturm noted that if the outside air is humid, a night purge would bring moist air into the building, which could affect the comfort of the daytime occupants.
“When it gets very humid, then we become uncomfortable,” he said.
The Right Equipment
Picking the right fan for the application is also a consideration when looking at AHU energy efficiency, Acosta said. Fans, she said, are the largest point of energy consumption in AHUs.
Variable-speed fans can save energy by running only at the speed needed, and are also less prone to mechanical wear and tear because they stop and start less frequently than constant-speed fans, limiting the number of jolts that come with being turned on and off, she said. Centrifugal fans are the most mechanically efficient, she said.
“When we talk about energy efficiency ... there are so many fan choices,” Acosta said.
Commercial AHUs can be connected to several types of heating and cooling technologies, but Paul said an air-source heat pump with a variable-speed compressor could be a good tool for energy savings.
“When you move to that inverter-driven, variable-speed compressor, that’s where you’re going to pick up those higher efficiencies,” he said.
Energy Recovery
Air-to-air energy recovery, which captures heat energy from the air being expelled from a building in order preheat or precool the incoming fresh air, could also play a role in system efficiency, experts said.
“Using air-to-air energy recovery allows the cooling and heating system to be downsized while also saving cooling and heating energy,” Sturm said.
Accessories for air-to-air energy recovery include the thermal wheel, which rotates between the incoming and outgoing airstreams to transfer energy; the fixed-plate heat exchanger, in which fresh and exhaust air crossflows in adjacent sealed channels; and the coil loop, which uses two or more coils in separate airstreams, with a circulating fluid to transfer heat.
“When you have the ability to recover energy from the exhaust, it makes a lot of sense to be able to pretreat that makeup air,” said Paul.
Air-to-air energy recovery, Sturm said, provides the biggest benefit during extreme outdoor weather conditions — extreme heat or extreme cold. That’s because there’s an energy cost to running the equipment — a motor for the energy wheel, a pump for the coil loop, the increased fan power needed to overcome the air pressure drop that comes with an additional accessory inside the AHU — that the recovered energy will justify.
“The system controller should be able to determine when it makes sense to use an air-to-air energy recovery device,” Sturm said.
Report Abusive Comment