When refrigeration systems are exposed to low outside air temperatures, the condensing pressure will fall, and if the head pressure gets too low, the metering device will not have enough pressure drop across it to operate properly. The metering device will then underfeed the evaporator, and a low pressure will result in the evaporator, which can cause refrigeration systems to short-cycle from the low-pressure control opening prematurely. Also, once the refrigeration system is off, it may never turn back on again, because the evaporator pressure may never reach the cut-in pressure of the low-pressure control.
Condensing units that are exposed to low ambient conditions must have some sort of low ambient control installed on them to prevent their head pressures from falling too low. However, before getting into the low ambient controls for condensers, let’s review the functions of a refrigeration system’s condenser.
Condenser Functions
One of the main components of any refrigeration or air conditioning system is the condenser, which condenses refrigerant vapor that is sent to it from the compressor. However, the condenser has other functions, including desuperheating, condensing, and subcooling.
The first passes of the condenser desuperheat the discharge line gases sent from the compressor. This prepares these high-pressure, superheated vapors coming from the discharge line for condensation — or phase change — from a vapor to a liquid. Remember, these superheated gases must lose all of their superheat before reaching the condensing temperature for a certain condensing pressure.
Once the initial passes of the condenser have rejected enough superheat and the condensing temperature has been reached, the gases are referred to as saturated vapors. The refrigerant is then said to have reached the 100% saturated vapor point.
As mentioned earlier, one of the main functions of the condenser is to condense the refrigerant vapor to liquid. Condensing is system dependent and usually takes place in the lower two-thirds of the condenser. Once the saturation or condensing temperature is reached in the condenser and the refrigerant gas has reached 100% saturated vapor, condensation can take place if any more heat is removed.
As more heat is taken away from the 100% saturated vapor, it will force the vapor to become a liquid, or to condense. When condensing, the vapor will gradually phase change to liquid until 100% liquid is all that remains. This phase change — or change of state — is an example of a latent heat rejection process, as the heat removed is latent heat and not sensible heat. This phase change will happen at one temperature, even though heat is being removed. This one temperature is the saturation temperature corresponding to the saturation pressure in the condenser. This pressure can be measured anywhere on the high side of the refrigeration system, as long as line and valve pressure drops and losses are negligible. (Note: An exception to this is a near-azeotropic refrigerant blend or ASHRAE 400-series blends of refrigerants. With the 400-series blends, there is a temperature glide or range of temperatures when the blend is phase changing.)
The last function of the condenser is to subcool the liquid refrigerant. Subcooling is defined as any sensible heat taken away from 100% saturated liquid. Technically, subcooling is the difference between the measured liquid temperature and the liquid saturation temperature at a given pressure. Once the saturated vapor in the condenser has phase changed to saturated liquid, the 100% saturated liquid point has been reached. If any more heat is removed, the liquid will go through a sensible heat rejection process and lose temperature as it loses heat.
The liquid that is cooler than the saturated liquid in the condenser is subcooled liquid. Subcooling is an important process because it starts to lower the liquid temperature to the evaporator temperature. This will reduce flash loss in the evaporator so that more of the vaporization of the liquid in the evaporator can be used for cooling of the product load.
Low Temperature Control
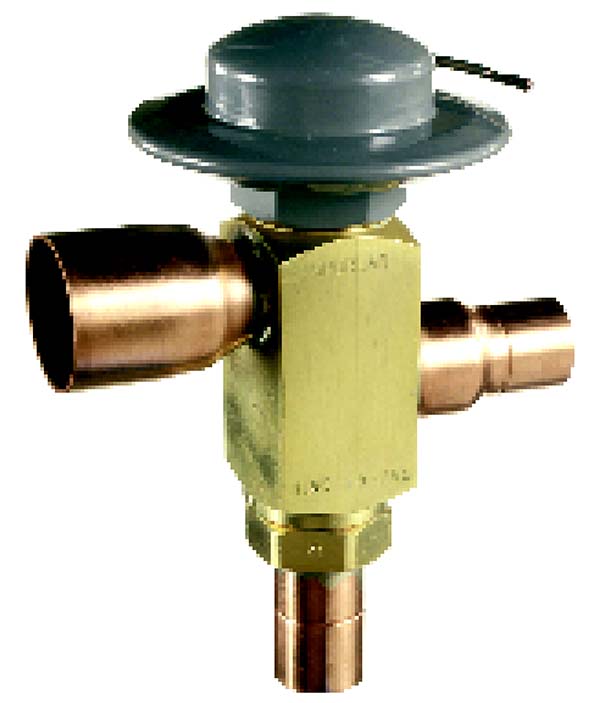
FIGURE 1: A head pressure control valve for low ambient conditions. Courtesy, Sporlan Division, Parker Hannifin Corp.
Figure 1 shows a head pressure control valve for low ambient conditions. Notice that the valve has a round pressurized dome at its top, which is charged with a proprietary charge from the manufacturer. The dome has a crimped capillary tube protruding from its body, which was used to introduce the proprietary charge when it was manufactured. This dome charge is separate from the system’s refrigerant charge.
Figure 2 (top) shows an internal cut-away of the same valve. Notice that here the charged dome acts on a flexible diaphragm as the outside ambient temperature changes. The action of the moving diaphragm will change the porting of the valve, which will be explained in following paragraphs.
This valve is often referred to as a low ambient control (LAC) valve. Figure 3 illustrates the LAC valve in a refrigeration system. As mentioned earlier, the dome charge of the LAC is independent of the refrigerant charge that is in the refrigeration system. The dome charge will expand and contract in volume as the outside ambient changes. This expansion and contraction action will act on the internal diaphragm, which in turn, will move the diaphragm. This action will move a piston in the valve and modulate the valve either in a more open or closed position. The dome charges can be custom ordered from the manufacturer to meet specific system or outside ambient requirements.
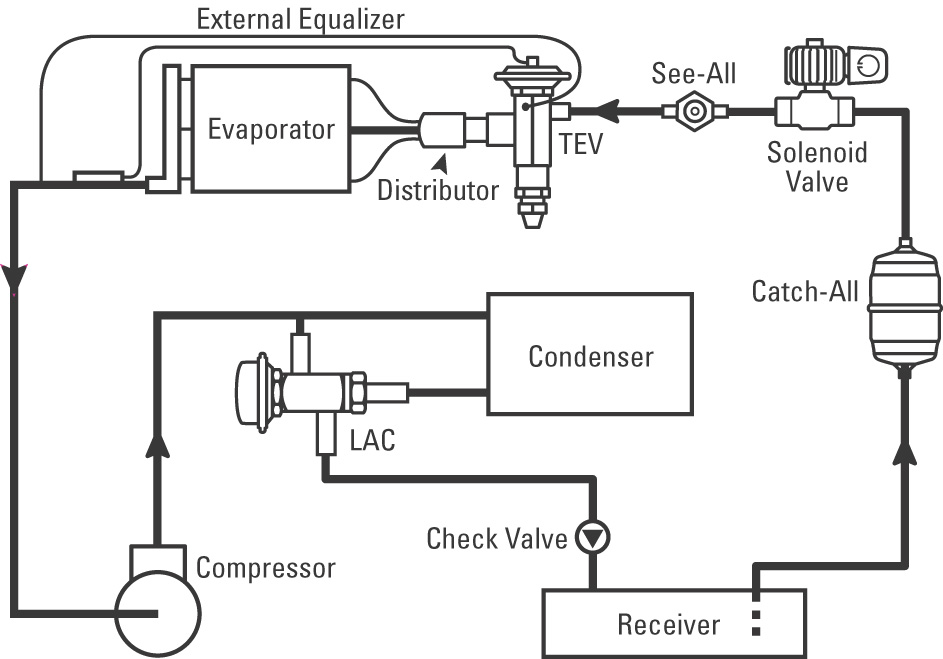
Click diagram to enlarge
FIGURE 3: The low ambient control valve shown in a refrigeration system. Courtesy, Sporlan Division, Parker Hannifin Corp.
When the ambient temperature is above 70°F, the refrigerant flow from the compressor’s discharge is directed through the condenser and into the receiver. When the outside ambient temperature drops below 70°F, the condensing pressure will fall, and the pressure of the liquid coming from the condenser will also fall to a point below that of the pressure of the bellows in the dome of the valve. This causes a piston to move in the valve and partially restrict the flow of refrigerant leaving the condenser. The condenser will now partially flood with liquid refrigerant at its bottom to maintain a condensing pressure for that certain ambient. The colder the ambient, the more condenser flooding there will be.
At the same time, some hot discharge gas from the compressor will bypass the condenser and flow directly to the receiver through the LAC valve. This hot, superheated discharge gas going to the receiver mixes with liquid refrigerant coming from the bottom of the condenser, thanks to the LAC valve. This action helps keeps the receiver pressure high enough to keep the metering devices fed with refrigerant.
The receivers on systems having head pressure control valves must be sized large enough to hold the normal operating charge, plus the additional charge that is necessary to totally flood the condenser in wintertime operations. In fact, the receiver should be sized so that they are about 80% full when they contain the entire system charge. This allows for a 20% vapor head for safety when pumping the system down. Any refrigeration system’s receiver should be able to hold all of the system’s refrigerant charge and still have a 25% vapor head for safety.
Manufacturers publish charts and tables on system charge recommendations showing the service technician how much refrigerant to add to systems having head pressure control valves designed to flood the condenser in colder weather.