Throughout the past month, as the COVID-19 crisis has filled hospitals with new patients and scratched deep into the American economy, HVAC manufacturers have provided a much-needed flood of good news. Many manufacturers have stepped up and are actively using their facilities and technologies to help fight the spread of COVID-19.
HVAC and Temporary Shelters
Some manufacturers, like Johnson Controls and Aaon, have worked to meet the HVAC needs of temporary hospitals being built to deal with an influx of coronavirus patients. Some of these field hospitals will use existing buildings, such as convention centers or large tents. The quick timeline for these buildings requires fast production of HVAC equipment to fill them.
In order to meet the demand for the equipment, the Johnson Controls ducted systems team, in collaboration with its residential manufacturing facility located in Wichita, Kansas, have partnered with the distributor and contractor network.
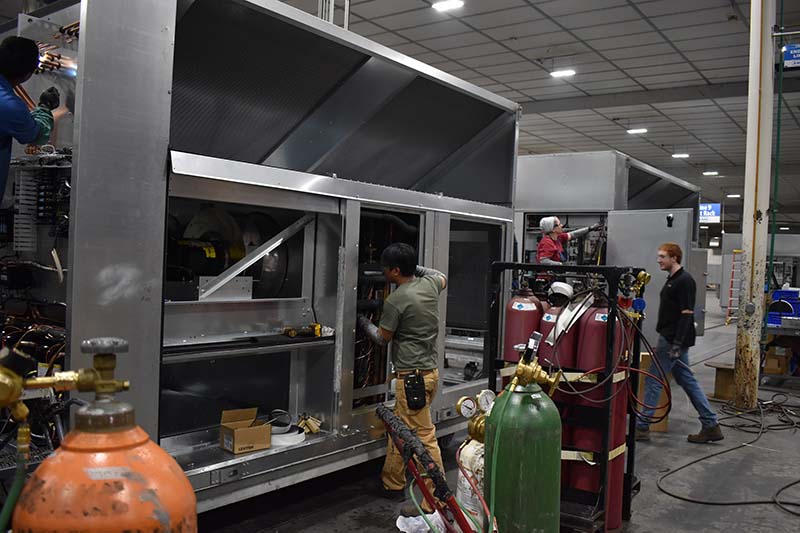
Aaon stepped up to build 2,200 tons of HVAC equipment for the Stony Brook temporary hospital in Stony Brook, New York.
“Our factory built 60 5-ton, 14 SEER packaged heating and cooling units for these field and pop-up hospitals around the world,” said Randy Wyngard, regional account manager, Johnson Controls. “It’s important that we pivot with our production schedule and ensure the people in need are getting great comfort and reliability coming from our manufacturing facility in Wichita. Our hearts and thoughts are with the healthcare workers on the front lines who are making adjustments around the country to fight COVID-19.”
The product orders were shipped to field hospitals across multiple channels in early April.
Aaon has done something similar in New York City, where they were asked to build 2,200 tons of HVAC equipment for the Stony Brook temporary hospital in Stony Brook, New York. This 2,200 tons of equipment equates to the cooling capacity of what would be required for over 700 single-family homes. After receiving the order for 44 50-ton job-customized Aaon HVAC units, the company went into immediate 24-hour production of the equipment in order to ensure shipment of these critical units arrived in New York in reasonable time.
HVAC Manufacturers and Reducing COVID-19 Transmissions
Other HVAC companies have responded to the COVID-19 crisis by making and/or donating masks to the hospitals that need them, as well as the creation of other hygienic equipment.
CoolSys, for example, has provided installation of plexi-glass protective panels, also known as sneeze guards, at checkout counters in grocery stores, restaurants, and other essential retail stores.
“During this challenging time, we are doing whatever we can to respond to the needs of our customers to prevent transmission of COVID-19,” said Adam Coffey, CEO at CoolSys. “By installing sneeze guard plexi-glass panels at the point of purchase, retail stores can add another layer of safety and peace of mind for customers and employees.”
While sneeze guards are already commonly used in grocery and food service locations at self-serve food bars and other areas that require a protective barrier, the installation at checkout counters represents a new measure in the effort to contain and prevent COVID-19 transmission.
“We are happy that our field crews are able to use their skills and experience to install sneeze guards at some of our most important customers’ locations to help keep their employees and their customers safer during this global crisis,” said Joe Roomsburg, general manager and former owner of Virginia-based BRR Refrigeration, a CoolSys company.
One company, Eaton, is leveraging expertise in additive manufacturing and its partnership with Cleveland’s Manufacturing Advocacy and Growth Network (MAGNET) to rapidly develop face shields for hospitals. The first batch of face shields made at Eaton’s Additive Manufacturing Center of Excellence in Southfield, Michigan, were donated to hospitals in Ohio, New York, New Jersey, and Michigan.
“What matters most is the ability for our healthcare system to respond to the crisis at hand, and Eaton can help,” said Michael Regelski, senior vice president and chief technology officer, electrical sector at Eaton. “From delivering critical supplies to ensuring always-on power for essential electrical systems, we’re supporting our communities and the healthcare industry during this crisis and in everyday circumstances.”
“We greatly appreciate Eaton’s donation of face shields, which will protect caregivers on the front lines and help reduce the spread of the coronavirus,” said MetroHealth president and CEO Akram Boutros, MD, FACHE. “It is inspiring to see the way our community has come together, including great partners like Eaton.”
By applying additive manufacturing capabilities, Eaton was able to quickly develop a face shield design that is comfortable for extended wear, maximizes facial protection, and can be sanitized and reused for a period of time. Eaton worked closely with MAGNET, MetroHealth System, university hospitals, and other healthcare providers to evaluate initial samples and refine the design. Eaton is rapidly scaling up production of face shields to more traditional manufacturing methods (e.g., injection molding) to deliver the volume of face shields needed to meet the demand of healthcare systems across the country.
Repurposing Patient Rooms for COVID-19
Another company, Clean Rooms International, has reconfigured its stock air filtration products to enable hospitals to convert standard patient rooms into negative pressure rooms for patient isolation.
“Healthcare systems are experiencing incredible pressure to accommodate growing numbers of patients impacted by the coronavirus,” said Tim Werkema, president and CEO of CRI. “Customers came to us seeking a new way to quickly convert standard hospital rooms into negative pressure rooms for quarantine. In less than a week, our team of engineers repurposed dozens of units. In less than a month, we’ve shipped more than 1,000 from coast to coast.”
Due to the nature of the COVID-19 disease, which can be transmitted through respiratory droplets in the air, CRI engineers looked at its HEPA air filtration product inventory. Standard HEPA fan filter units were inverted and paired with exhaust systems or mounted to a small cradle with castors to create mobile units. The products are highly efficient in filtering and evacuating contaminants from the air. This creates a negative pressure environment, minimizing airborne contagions from entering hallways and corridors in a health facility.
“As infection levels continue to rise, hospital systems will look for new and inventive ways to convert their facilities to meet patient needs,” said Bret Asper, chief operations officer at CRI. “We’re grateful our product engineers were able to come up with a quick and cost-effective solution and we can bring this to market as quickly as we did.”
Report Abusive Comment