At One Stop Cooling, we study the readings that technicians record on service and maintenance calls. This allows us to look for technical oversights that technicians should have shared with customers. When we first started doing this, we were surprised with the mistakes that could be found if a weekly sampling of techs’ readings was performed.
Now, I’ll give a sort of spot-check quiz that demonstrates the value of studying your technicians’ readings. Here’s a scenario: A technician arrived at a home and found a bad capacitor. They did not see anything else wrong with this unit, as they only applied the “ballpark rule of thumb” that says a 15° to 20°F split was acceptable. They left the home.
But now, we’ll look at the screenshot the technician turned in and see if there's anything else begging for attention.
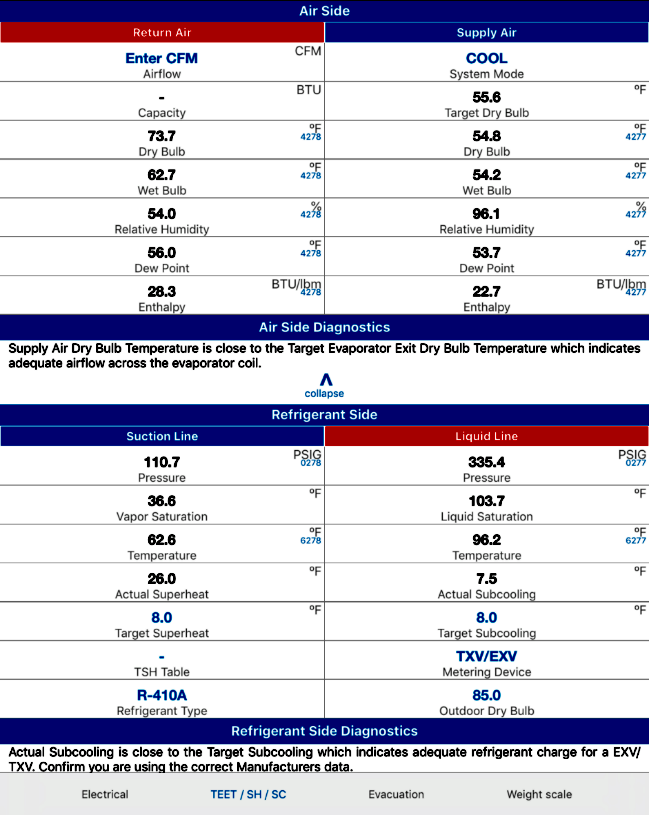
Air Side Report
Here’s what stands out on the air side report:
- The target dry bulb temperature and actual dry bulb are within the 3° differential. If exceeded, this will trigger an alert. However, it is within the differential, so it is okay.
- The wet bulb return and supply difference should be between 10 and 12 on a properly tuned system in Florida at 400 cfm per (actual) ton of performance. Here, it’s only 7.5, so the technician should have examined the wet bulb.
- Lastly, note the enthalpy. Subtract supply from return: a difference of 5.6. A properly charged, metering, and airflowing system in Florida will render an enthalpy difference of 6.7. at 400 cfm per ton. The enthalpy range we want is 5.96/350 cfm to 6.7/400 cfm per ton. The technician should have noticed this enthalpy range and acted accordingly.
This unit isn’t dehumidifying as well as it should. Upon seeing these readings, the technician should have investigated for the root cause. But in our situation, they did not. With an after-the-fact analysis of the technician’s readings, this oversight would have been caught and remedied.
Refrigerant Report
Now, we’ll study the refrigerant side. I immediately notice that the subcooling is adequate, but there is a high superheat. This thermostatic expansion valve (TXV) is rated for 7° to 9° superheat, but we are running at 26° superheat at the evaporator.
The tech should have verified actual/adequate cfm and adjusted the speed if necessary. If refrigerant readings were still out of tolerance, they should have documented the performance observations. They should have eliminated possibilities of a restricted drier or liquid line, and should have articulated the recommendation to replace the faulty TXV verbally and in writing.
Techs could have missed this if they weren’t equipped and trained by their supervisors. At One Stop, we require all of our techs to gather both the air and refrigeration side information on every call, especially since the wireless kit takes only five minutes to hook up. We use Fieldpiece’s Job Link Wireless Charge & Air kit to capture the readings that will be reviewed later.
If you assume your technicians know technical skills and hope they apply them with discipline in every customer’s home, you might be amazed how many deficiencies exist in some of your customers’ units if you analyzed technicians’ readings and invoices.
Publication date: 5/13/2019
Want more HVAC industry news and information? Join The NEWS on Facebook, Twitter, and LinkedIn today!
Report Abusive Comment