Bob has been on a job at a convention center with a 100-ton water cooled condenser. The owners are really anxious for Bob to get the air conditioning back on, but Bob said the tubes must be cleaned before the unit will run. He has called the shop and asked for a helper and a tube cleaning machine to help him get the unit running as fast as possible.
The maintenance man for the convention center, Ron, was looking on as the condenser was being prepared for cleaning. Ron had looked at the tubes with a very small flashlight and agreed that the tubes had a thin layer of scum on them. He couldn’t understand why because he said he kept the water tower very clean.
As they were setting up the equipment, Bob said to Ron, “I noticed that the tower was very clean. That has nothing to do with what is on the inside of these tubes. This is mineral residue.”
Ron asked, “Where does the residue come from?”
Bob explained, “The water in this area has minerals from the ground suspended in the water. You can hold a clear glass full of water up to the light and cannot see them, but they are there. You have probably noticed that when you boil the local water there is a residue left in the pan. When the water is boiled away, the minerals are left behind. If you read your wife’s steam iron directions, they will tell you to use distilled water. Not just filtered bottled water, but distilled water, because it is mineral free.”
Ron said, “I have seen that in the directions. Surely you aren’t going to tell me to use distilled water in the cooling tower system.”
Bob said, “No, that is not practical. There are other ways to deal with the minerals in cooling tower water. In addition to minerals, there will also be algae forming in the nice warm water in the tower. It is the green or black looking scum that you find clinging to the parts of the tower where the water stands. Algae is a low form of plant life that forms in old water.”
Ron said, “Yes, I have washed it out of the tower with detergent and a brush. It comes out very easily. I wash out the tower about once a month.”
Bob cautioned, “Be sure you wear rubber boots, gloves and goggles. That algae can contain some bad stuff, such as Legionella. It can really cause some bad respiratory problems. It has been fatal in some cases.”
Ron responded, “I have read the safety bulletins on that and take proper precautions.”
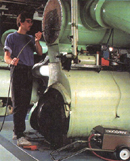
Figure 1. This is a machine that is set up to clean the tubes of a heat exchanger. The brush rotates and water is used to flush out the dirt from the tubes. (Figures are from Refrigeration & Air Conditioning Technology, 5th Edition, by William Whitman, William Johnson, and John Tomczyk, published by Delmar Cengage Learning.) (©Delmar Cengage Learning.) (Click on the image for an enlarged view.)
Bob then said to Ron, “Notice that we have removed the heads from both ends of the condenser. James set the machine up at one end and is starting to clean the tubes. Notice that he is using a nylon brush that turns and flushes water as he feeds the brush into the tubes. Let’s see what comes out the far end when the brush reaches the end of the tube.”
Ron said, “There is a residue coming out. I guess that is what was on the tubes.”
Bob said, “Yes, now let’s look at a clean tube and a dirty tube. Can you see the difference?”
Ron said, “Yes, I can see the copper better on the cleaned tube.”
Bob then said, “James and I are going to clean the remaining tubes as fast as we can and get the unit back on line.”
Ron said, “That is a good idea. I have noticed that you don’t waste time. Management likes to get their money’s worth.”
When the tubes were all cleaned and rinsed off, Bob and James washed down the floor and fastened the water box covers back on and turned the water back on for the condenser. Then they started the condenser water pump and started the chiller.

Figure 2. This figure shows the relationship of the condensing refrigerant to the leaving condenser water, called the approach. (©Delmar Cengage Learning.) (Click on the image for an enlarged view.)
“Sure”, said Bob. “I brought a picture in this book for us to examine. This is a drawing of a typical condenser and the temperatures that are affiliated with it. The refrigerant is different, but the temperatures are typical.
“Notice that the water in the cooling tower basin is 85°F. This is typical. The water returning from the condenser to the top of the tower is 95°. This condenser has a 10° rise in temperature which is heat that came from the refrigerant. Notice that the head pressure shows that the refrigerant is condensing at 105°. The difference in the condensing temperature and the leaving water temperature is 10° (105-95 = 10). This is called the approach temperature (Figure 2). That is a typical approach temperature for a reciprocating compressor and condenser. These are normal readings for a two-pass condenser. Notice that the water enters the condenser and goes to the far end and exits at the same end (Figure 3).”
Ron said, “There is a lot to this business. I think I may need to go to the local community college and get well grounded in this field.”

Figure 3. This illustration shows the various numbers of passes for a heat exchanger. This is an evaporator, but it is the same for condensers. (©Delmar Cengage Learning.) (Click on the image for an enlarged view.)
“How long will it operate like this?” asked Ron.
Bob replied, “That is a hard number to know. What we do know is that once minerals or algae start to build up on the tubes, it then has a base to build on and the film will begin to build faster. By watching the numbers - condenser inlet, condensing temperature, and condenser outlet - we can spot a problem coming up.”
Ron then said, “That is a big help. I will start recording these numbers about once a week and I can compare the numbers.”
“Now, let’s talk about how to get the most performance from the water and condenser,” said Bob. “It is just a fact that algae and minerals will begin to form in cooling tower water. Notice the waste water system on this cooling tower that allows a certain amount of water to waste to the drain any time the water is circulating. That waste water is necessary. It acts to partially dilute the circulating water so that the mineral concentration is at a minimum. When the waste water puts water down the drain, the water is made up through the float system with fresh water. That is part of the method to keep the water usable. The other part is a good water treatment system, using chemicals. You should contact a reliable water treatment company and let them test your water and set up a regular water treatment system that will control the algae and help keep the minerals in suspension until they go out with the waste water.”
Ron said, “I want to thank you for your help and sharing information with me.”
Bob then said, “There is plenty of room for informed technicians in this field. I hope you do go on and start going to school part-time in this field.”
Bob was loading his truck when Btu Buddy appeared. Bob said, “Well, it took you a long time to get here.”
Btu Buddy said, “I was looking in and didn’t see a need. You were doing great. Someday, and that won’t be long, you will be a Btu Buddy to someone else.”
Publication date:07/19/2010
Report Abusive Comment