Originally offered solely as a wall-mounted indoor unit solution in system capacities of 7,000 Btuh to about 12,000 Btuh, the ductless system delivered improved performance with greater efficiency (EER) and the beginnings of comfort “you control,” zone-by-zone. The ability to remotely locate the condensing section of the system, and thus remove the sound-bearing components from the occupied space, was a big positive in freeing up window space, and all units were provided with a user-friendly operation interface.
One of the key factors to the early success of the ductless system was the fact that with piping allowances of up to 15 feet, the small, compact condensing units could be sited in varied locations in keeping with the space-restricted Asian construction methods.
To this day, the global “staple” ductless product is a wall-mounted indoor unit, estimated at 75 percent of total global mini-split sales. Many manufacturers have seen opportunities, introducing alternative ductless indoor units, including floor console and ceiling-suspended models. Concealed ducted-style and concealed ceiling cassette units have also been introduced, giving the ductless a crossover application in the commercial world as well.
ADVANCES IN TECHNOLOGY
From a service and maintenance perspective, the ductless products established a reputation of reliability. This reputation has been further enhanced by technology today, with installations seldom having callbacks. The systems, as contractors discovered, are extremely maintenance friendly, only requiring simple filter maintenance and condenser coil cleaning each quarter, whether it is a small system or a large modular, multizone system.As the Asian solution has gradually been introduced around the world, the demands each region created - both from a sales and design standpoint - have further evolved the concept, allowing the ductless to become the mainstay of many countries’ HVAC markets. Such advances included:
All of these features led to perhaps the biggest evolution of the mini-split, with the advent of multi-split and then the more sophisticated variable refrigerant volume (VRV) zone systems, which when broken down to its core elements, are just big mini-split systems. These developments established a ductless option to serve whole-house residential applications with multi-split systems for up to five zones. On the commercial front, offering VRV systems with its modular approach can serve large-scale applications, sometimes with hundreds of zones.
CONTINUALLY EVOLVING
In a business sector where it is renowned that things have been done the same way for generations, the rate at which the ductless system concept has grown due to the nature of applications they now serve has ensured technology included in the systems has been continually evolving. It is commonly at the forefront of component and electronics development around the world, especially in the HVAC industry.While a ductless system is just a common DX system encompassing the basic compressor, condenser, expansion device, and evaporator configuration, opening up a ductless condensing unit today commonly reveals a piping system that many HVAC contractors tag as a “spaghetti western.” This includes a multitude of other components, such as solenoid valves, capillary tubes, bypass circuits, etc. However, all of this technology, coupled with detailed electronic algorithms, has allowed the envelope of the ductless system to be stretched to serve the vast applications they do today and continue to develop.
With the original target to serve as a realistic alternative to window units, the technology included was sparse, ensuring any premium could be justified with some key features as previously highlighted. Systems were built on an R-22 platform and generally included effective rotary-style “standard” compressors, direct-drive fan motors, standard heat exchangers, and little “razzamatazz.”
As the acceptance and volume grew, the means were present to take the technology to the next level. Technology upgrades are normally considered for the whole system, as performance and efficiency gains in single components are seldom worthwhile. Over a period of about 15 years, some key developments took place, including:

Single-split and multi-split (one condenser for multiple evaporators) are now available from several manufacturers.
TWO KEY CHANGES
The key technology developments of the past 20 years in ductless have been inverter technology and, more recently, the switch to R-410A and growing trends with IAQ.With inverter technology, ductless products are able to optimize energy consumption in accordance with the changing ambient temperature, ensuring comfort in the occupied space but ultimately saving energy at the same time. The technology works by varying the rotational speed of the compressor as the load fluctuates to deliver only the optimum amount of refrigerant to the connected load to serve the cooling or heating requirements.
The technology commonly re- sults in superior energy performance compared to alternative systems employing fixed “on-off” compressors. Inverter-based systems are optimized for the complete annual operation envelope, instead of a few key temperature conditions.
With the advent of R-410A, the impact to ductless technology has been great. The systems have become, on average, 40 percent smaller, yet around 30 percent more efficient. At the same time, they are quieter, with more features, and significant advances in application allowances (pipe length, ambient temperature range, etc).
One of the key features of R-410A is an excellent heat transfer coefficient, especially at low ambient temperatures. As such, it has helped ductless systems shake off the negative image associated with heat pump systems of old, by delivering effective and efficient heating performance in ambient conditions as low as 15° and guaranteed operability down to -4°.
R-410A is also seen as the long-term refrigerant choice and, as such, system specifications are sure to continue to improve as new technologies are developed to work specifically with this refrigerant.
IAQ concerns, elevated during the SARS situation experienced in Asia during 2004, opened up a new target for ductless systems to satisfy. Systems have been introduced that not only “filter” the air, but remove harmful germs and viruses, and act as purifiers. Many ductless systems now employ an onboard mechanism to “self-clean,” removing the reliance on regular maintenance being completed. In the United States, as IAQ is at the forefront of the industry at this time, one can already see various ductless products, designed with SARS in mind, enter the market place as a local IAQ solution.
APPLICATIONS GROW, TOO
From a legacy of solving single-zone applications as an alternative to using a window unit, the applications for ductless products around the world cover the full scope of the HVAC industry. The most common application remains a single zone “spot cooling” solution, such as individual bedrooms and bonus rooms, etc. However, as you dig a little deeper, you will commonly find ductless systems installed in commercial business-es (chain-stores, mom-and-pop stores, etc.); whole-house residential applications; communication rooms and elevator rooms; offices; churches; hotels; condominiums; health care facilities; restaurants; schools; and storage facilities.Some out-of-the-ordinary ex-amples of how ductless technology has been applied as the main solution to HVAC needs, specifically the commercial sector, include airport terminals, multiplex theaters, Grand Prix circuit, and an Olympic horse riding center, to name a few.
As the technology continues to evolve, new application challenges are arising everyday, further developing the scope of the ductless product.
ANYTHING IS POSSIBLE
In the market today, the face of the ductless mini-split industry is different from its early days with a diversity of product offerings from manufacturer to manufacturer and country to country. Today’s market is extremely competitive, yet buoyant with growth and innovation, while introducing customer-focused solutions as market demands and consumer habits change. Where ductless mini-split technology is established with widespread acceptance and recognition of the technology, you will find the equipment almost everywhere.The ductless systems available today come equipped with fully functional control systems, allowing the customer to select between cooling, heating, ventilation (fan), and, in many instances, dry mode of operation. Dry mode is a function that takes full advantage of inverter technology by draining moisture from the occupied space while only resulting in a very small temperature change.
Today’s ductless units incorporate a whole host of features, such as setback (temperature and sound), occupancy sensors, and powerful “rapid” cooling and/or heating modes. They can be interlocked to a host of third-party control options, or be controlled via the Internet. They are very quiet in operation, at the top end of the efficiency market, and are commonly backed up with some of the best warranties in the HVAC industry.
The nature of ductless technology is always changing and being updated. The ductless system manufacturers listen to customers and develop new products to meet market de-mands accordingly.
Also, these manufacturers work very closely with industry organizations and governmental bodies to contribute and be alert to the continually changing face of the HVAC industry worldwide.
Around the world, product development remains ahead of the curve. Ductless systems begin to change again with the development of systems capable of controlling both temperature and humidity, wall-mounted indoor unit systems capable of introducing ventilation (outside) air to the occupied space, the growing amount of CO2-based systems, and even a shift towards solar (photovoltaic) cells included on condensing units.
Whatever the future brings, it’s sure that ductless technology will continue to be at the forefront of innovation and deliver customer-driven solutions, satisfying the demands of the market.
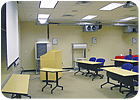
Sidebar: Sanyo Opens a Living Model
Sanyo is going out of its way to prove its point. It recently opened a new HVAC applied products sales, service, and training office in a suburb of Atlanta. In the new facility, Sanyo variable refrigerant flow (VRF) systems are in place, both ducted and ductless. There are a total of six ductless units in the building: two in the lunchroom, two in the conference room, one in the warehouse, and one in the reception room. The condenser is on the roof and the units are all linked in a daisy-chain manner.The units were installed not only to condition the air, but also to showcase a living model. “When HVAC technicians come in for training, they can see right away how unobtrusive the units look in the room,” said Watkins. “The ceiling units fit very nicely into the drop ceiling and the wall units blend in with the room décor.”
The training room includes a fully operational 8-ton commercial condenser. The condenser is made of see-through material so that technicians and instructors can see the operation of the unit and have a clear idea of how the refrigerant flows through the system.
“This gives the opportunity of true hands-on training,” explained Watkins. “Once having completed the training, the technicians and systems designers/installers have a better idea of the types of systems they can offer their customers, thus providing better solutions to demanding requirements.”
Sidebar: Double Efficiency, Not Size
The fact mini-splits have doubled in efficiency, but not in size, is something John Miles is proud of. The director of engineering and technical support for Samsung/Quietside points to inverter compressors and R-410A for making this feat possible.“An inverter compressor is an intelligent compressor, as it can alter the frequency of the motor to control the speed and capacity produced,” explained Miles. “These units now communicate at all times with the indoor unit and several of the sensors in the outdoor unit to control the speed of the compressor and the position of the electronic expansion valve - mounted in the outdoor unit to reduce indoor noise levels - to provide the capacity required inside the home or office to cool or heat to the desired temperature.”
This means that several major benefits occur over units with conventional “on and off” control of the compressor, he explained. The first one is a rapid cool down, or heat up, to the set temperature, he said.
Imagine for a moment that it is the middle of summer, 90°F with humidity that you can cut with a knife. Your inverter drive mini-split in your house has been off all day, so on your return you want cooling and fast.
“Once the unit is turned on and set to the temperature required, it will quickly measure the return air temperature and determine that the differential between set temperature and room temperature is large, therefore more capacity is needed,” explained Miles. “The unit will then start the compressor and, recognizing that a higher capacity is needed, increase the frequency of the compressor motor, ultimately increasing the capacity of the system.”
With a conventional-style unit, as the room temperature approaches the set point, the compressor will cycle off once the thermostat indicates it has satisfied stopping refrigerant flow to the indoor coil, he said. “With an inverter-drive compressor, this does not happen,” said Miles. “As the room temperature approaches set point, the indoor unit tells the compressor to reduce capacity. We can reduce the 9,000 Btuh unit capacity down to 3,000 Btuh.” This will have two beneficial effects, he explained.
1. The room temperature can be much more tightly controlled, as the compressor is no longer stopping and starting, but just modulating.
2. When the conventional system is off, no dehumidification is being performed, as the coil has no refrigerant flowing through it. However, with the inverter system, the coil remains active and the system continues to remove humidity without overcooling the room, he explained.
“Obviously as the inverter compressor is modulating, the input power required by the unit is being reduced,” he said. “This is the premise behind being able to have a 20 SEER rating, due to the unit operating at a lower frequency or capacity when either the room temperature is approaching set point or when cooling is required at lower ambient temperatures.”
The electronic expansion valve also assists in this by delivering “precisely the refrigerant flow required in the system and maintaining the optimum suction and discharge superheats needed to run the compressor at its optimum,” he said. Another benefit to the compressor modulation is a reduction in the outdoor noise levels for all of the inverter drive models, he added.
“As the compressor modulates down in capacity, so does the noise level reduce, making these units a lot nicer to your neighbors’ ears,” said Miles.
Publication date: 04/30/2007