THE CHALLENGE
Budget cuts and competitive pressures have reduced building maintenance staffs in many public and private enterprises. This frequently results in a reprioritization of activities, forcing concentration on addressing issues which are required to be fixed at the moment. Repair items such as an HVAC drive system operating in bypass mode may be considered only a nuisance, to be dealt with as time permits. And, of course, time seldom does so permit.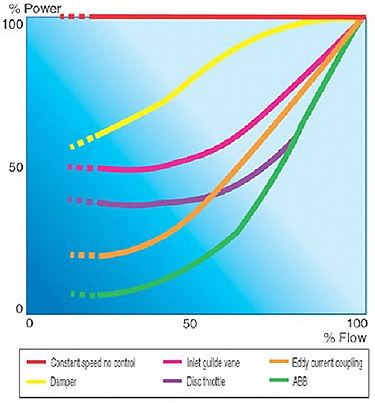
HISTORICAL PERSPECTIVE
Consider the rationale for installing HVAC variable frequency drives over the past 10-15 years to control the airflow in buildings. These drives were originally installed to replace the throttling systems designed to regulate flow of air in the system. While throttling reduced the flow, the motor still ran at nearly full load speed and in some cases worked even harder to overcome the added system restriction. By reducing the speed of the motor, the variable speed drive ensures no more energy than necessary is used to achieve the required flow.For example, in theory, a fan running at half speed consumes only one-eighth of the energy compared to one running at full speed. Field experience has shown that when the effect of static back pressure is factored in, the relationship is somewhere between 1/4 and 1/8 of the energy consumed at full speed depending on the application.
BYPASS FAILURES
Recent studies indicate that 8-12 percent of HVAC drive systems are running in a bypass mode due to a drive fault. The intent of a bypass contactor is for use in case of a drive failure for short-time emergency service. It was never intended to be a long-term solution to a drive malfunction. While the misapplication of long-term use is understandable due to increased pressures on typically under-manned building maintenance organizations, there are proven approaches to solving this pressing problem.Why worry about this now? Energy costs continue to soar. Between 1999 and 2004, electricity costs increased by nearly 15 percent (source: Department of Energy). When VFDs were purchased for the application, the additional costs were justified based on saving money and improving profitability by using less energy for HVAC air handling in the building. As an example of how long-term use of bypass contactors affects energy costs, if 10 percent of the drives are in bypass mode, up to 56 percent more energy can be consumed by the HVAC air handling system. This is based on the assumption of all motors being the same size and all HVAC systems operating on average at 50 percent flow.
NEXT STEPS
The path forward presents two clear choices. First, do nothing and continue to lose increasing amounts of money every day as additional VFD systems periodically fail and go into bypass operation. Second, develop a program which will change the way drives are proactively maintained.A typical preventative maintenance program is centered around the following activities:
1. Review your situation. Utilize either an outside or internal resource person to inventory the drives in the building or complex to gather the following information:
2. Replace or repair all of the drives operating in the bypass mode to begin realizing the original energy savings. It is important to work with a supplier that demonstrates the capability to easily replace or repair drives. Select one that will assist in the maintenance and support on an ongoing basis.
3. Create or contract a preventative maintenance program which focuses on the specific issues of drives and how to keep them up and running. These activities typically include, but are not limited to:
With the VFD deenergized
With the VFD reenergized
4. Replace older and highly critical drives before they fail. When a drive is over 10 years old and/or in a demanding and highly critical application, consideration should be given to replacing it before failure. Even with the cost of a new drive and installation, the benefits will include lower operating costs and improved client comfort. Simple payback, 10-year-life-cycle costing, or other financial analysis techniques may be performed to formally evaluate the economics for drive change out.
CONCLUSION
VFD systems installed in the facility have a proven track record of saving energy and improving client comfort. The ability to keep drives running as designed will assure continued savings and comfortable clients.A number of significant improvements have been made to present-day VFD systems compared to what was available 10 years ago. Drive size and parts count have been reduced along with cost, while increasing performance, quality, and warranty periods. Commonly available features include embedded PI control functions which eliminate the need for closed loop output signals from the building automation system (BAS). The PI controller typically includes feedback inverse, square root, and differential control functions on-board which lower costs of HVAC control systems installation and wiring.
VFD units now typically combine sophisticated IGBT power switching with advanced microprocessor logic to reduce audible motor noise and meet accepted power quality standards. A number of communication options are available which can be tailored to a wide variety of BAS data and control formats. On-board metering of electrical kW and kWh information provides data useful in efficiency and billing calculations.
Reprinted with permission from the ABB white paper "Four Steps to Reduce Your HVAC Energy Cost." For more information, visit www.abb.us.
Publication date: 03/06/2006
Report Abusive Comment