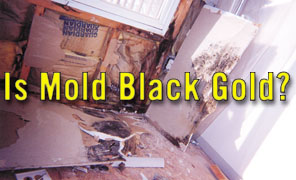
Why should HVACR contractors get into indoor air quality (IAQ) testing and mold remediation? A better question may be, why not? After all, poor IAQ can lead to mold and possibly “Sick Building Syndrome” (SBS) — and building mechanical systems are often targeted as playing a big role in mold growth and the possible damaging effects of SBS.
“As the industry watches the mold issue, I am convinced there will be multiple opportunities for businesses to find a niche for both testing and abatement,” said News’ contractor consultant Jeff Stewart of Quality Air Conditioning, Las Vegas, NV. “I certainly don’t think current indoor air quality processes — i.e., duct cleaning, duct sealing, and filtration — are sufficient for mold prevention. They can help, but it will take more detailed procedures, like dehumidification, UV lights, and such to really create a business plan that can enter into this area of expertise.”
IAQ testing and mold remediation opportunities are available in the residential markets, and also, it appears, in high-profile commercial markets. For instance, Claire L. Barnett noted one should not overlook schools.
“HVAC contractors should become more aware of children’s susceptibility to a wide variety of hazards in the school environment, as well as the alarming problems with asthma at school,” said Barnett, executive director of the Healthy Schools Network Inc., Albany, NY. “The recent Centers for Disease Control report on its investigation of the outbreak of school rashes indicates problems with chemical hazards, carpets, dusts, and molds.”
In the eyes of Todd Morgan Jr. of Comprehensive Energy Services Inc., Altamonte Springs, FL, a contractor’s continued success into the future depends on adding value to existing services and expanding into emerging markets.
“As individuals have begun to take note of how their environment affects their well being, a new market of consumers has arisen,” said the commercial contractor, noting that testing and remediation appear to be growth areas for contractors.
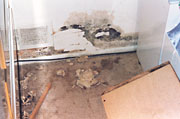
SYSTEM DESIGN
Most experts agree that the first logical step HVACR contractors can take is to design systems that minimize the opportunities for mold growth.“[Experts] have noted that the HVAC system is responsible for 50% to 60% of building-generated IAQ problems, and more importantly, capable of resolving up to 80% of IAQ problems,” said Morgan.
“HVACR contractors should do what they are trained to do in the most complete and professional manner possible — design, install, and maintain HVACR systems using the most recent accepted industry guidelines,” said Bob Baker of BBJ Environmental Solutions Inc., Tampa, FL. “In addition, I believe that if they pay special attention to system hygiene, including keeping all components clean and free from growth and installing new and proper filtration, they will do much to prevent or minimize mold problems in the buildings they serve.”
But most experts agree that system design can lose some of its effectiveness if the mold source — such as mold growing on water-damaged materials — is not found and controlled. Contractors can try a “reasonable” approach to such situations, trying to stop the source of water infiltration and then remediating the existing mold. The extent of the remediation depends on the extent of the mold growth. It can range from removing some damaged sheetrock to moving the people out and gutting the home.
“We have a three-step response to the issue,” said News’ contractor consultant Jim Hussey of Marina Mechanical, San Leandro, CA. “Education, first; testing and monitoring, second; and remediation, third.
“We educate through our newsletter and regular communication with our clients. Whenever our client or we suspect a problem, we test, using an independent lab for analysis. Test results dictate the response and level of remediation, which can be as simple as modifying maintenance procedures to a complete system retrofit.”
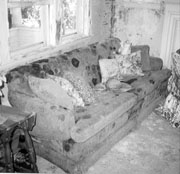
THIRD-PARTY HELP
If contractors don’t want to commit to mold testing and/or remediation training and education, they have the option of partnering with specially trained businesses.“If they [contractors] are going to sub out the remediation, they need to deal only with trained and certified contractors because that sub is now an extension of their company and they are still liable for problems that come up,” said Jerry Wolf of Air Purification Systems of Houston, TX. “As for the testing, I have always had the opinion that it should be done by a certified industrial hygienist and processed in a lab that can give accurate results and can write a detailed scope of work.”
Mike McGuinness of R.K. Occupational and Environmental, Phillipsburg, NJ, noted that contractors should learn to become educated consumers of these types of remediation services “and partner with experienced professionals in these fields, particularly the testing and engineering end of things.”
Added Morgan, “I think it is absolutely pertinent that the HVACR contractor partner with experienced laboratories and remediation companies. Every job has different levels of complexity, and it is important to have a qualified group of team players at your disposal.”
“We work with a couple of testing consultants who can pinpoint mold and other IAQ problems and then we can follow up,” said News’ contractor consultant Roger Grochmal of Atlas Air/ClimateCare, Mississauga, ON. “We do not do mold remediation on our own at this stage.
“We will advise homeowners to try to solve mold source issues, such as wet basements, as a primary strategy and then perform mechanical retrofits, such as ventilation and dehumidification, to get the relative humidity below 50%. We may then also use ultraviolet to ensure that spores are cleaned up.”
LIABILITY CONCERNS
In order to understand the entire mold issue and the liabilities that HVACR contractors face, a thorough understanding, via proper training and education, is the first step to take.“Whether or not a company likes it, they will be more involved in the effects of mold on indoor air quality,” said News’ contractor consultant Larry Taylor of Aire Rite Air Conditioning Co., Fort Worth, TX. “If for no other reason, the insurance cost will pull them into it. Contractors are now purchasing pollution coverage at a much greater pace that ever before.”
According to Taylor, pollution coverage is a separate insurance policy that covers a contractor that releases “pollution” into a customer’s home. He cites this situation as an example: If a contractor should a take a panel off an old air handler, and there is mold lurking behind the door, the mold spores could spread. “Pollution now occurs,” Taylor said.
Vikki Nicholas of Bay Temperature Control Inc., Baytown, TX, believes it would behoove the HVACR contractor to become as knowledgeable about mold issues as possible.
“I think they will be held to a level of accountability,” she said. “In order to have some input into that level of accountability, they need to be informed of the issues. Such things as what causes mold, what prevents it, and legal steps that need to be taken to protect one’s company, all need to be a part of the modern HVAC contractor’s business plan.”
EDUCATION
Wolf believes that anyone who does mold remediation should go to an accredited class — and that means classes held for more than one or two days — plus be taught by qualified instructors, who know how to safely and properly handle mold remediation.“They should then be required to pass a certification test before they do any remediation,” he said. “We rent negative air machines and air scrubbers to contractors. I’m constantly hearing contractors come in and ask, ‘What do I need and how do I do it?’ And for this ignorance they are making big dollars and doing sorry work. The problem is, they never learned to do it right.
“You need to stick to your guns about doing it right, because the homeowner — and especially the insurance company — may try to beat you down, price-wise. You have moral and ethical responsibility to that homeowner to remediate properly and you are increasing your liability if you don’t do it right.”
News’ contractor consultant Steve Miles of Jerry Kelly Heating & A/C, St. Charles, MO, described this potential profit center as a “niche.”
“Is it a niche? Yes. How big of a niche, who knows?” he asked. “Because of the ‘litigation factor,’ I don’t want to make promises unless I’m positive of the outcome. I do see the current awareness as an opportunity to educate the consumer about what can and can’t be done — and the maintenance required to keep the air they breathe as clean as possible.”
McGuiness concluded, “I believe [contractors] should learn how to remediate mold properly in HVAC systems. There is much work out there for HVACR contractors who can remediate moldy systems.”
Publication date: 07/08/2002
Report Abusive Comment