Having the right tool policy is important not only to the success of an HVAC company, but also to the success of the technicians who work there. Some in the industry follow the policy of having technicians buy their own tools, while others invest in providing all the necessary tools for them.
Both policies bring different benefits. When technicians buy their own tools, they are likely to care for them better while also feeling like they have more of a stake in their career. When the company provides the tools for the technicians, inventory becomes easier and the chance of double-purchasing a tool becomes less likely.
chief operating officer
Golden Rule Plumbing, Heating, Cooling, & Electrical
Golden Rule
When Golden Rule Plumbing, Heating, Cooling, & Electrical in Des Moines, Iowa, first opened, president and owner Mark Paup bought everything that was needed for his technicians, like their tools.
“And when I would walk by their vans, they would be using them as stepstools,” Paup said.
Needless to say, the tool policy has changed since. Techs are now required to buy their own hand tools and battery drills.
“Now our policy is you provide your own tools,” Paup said.
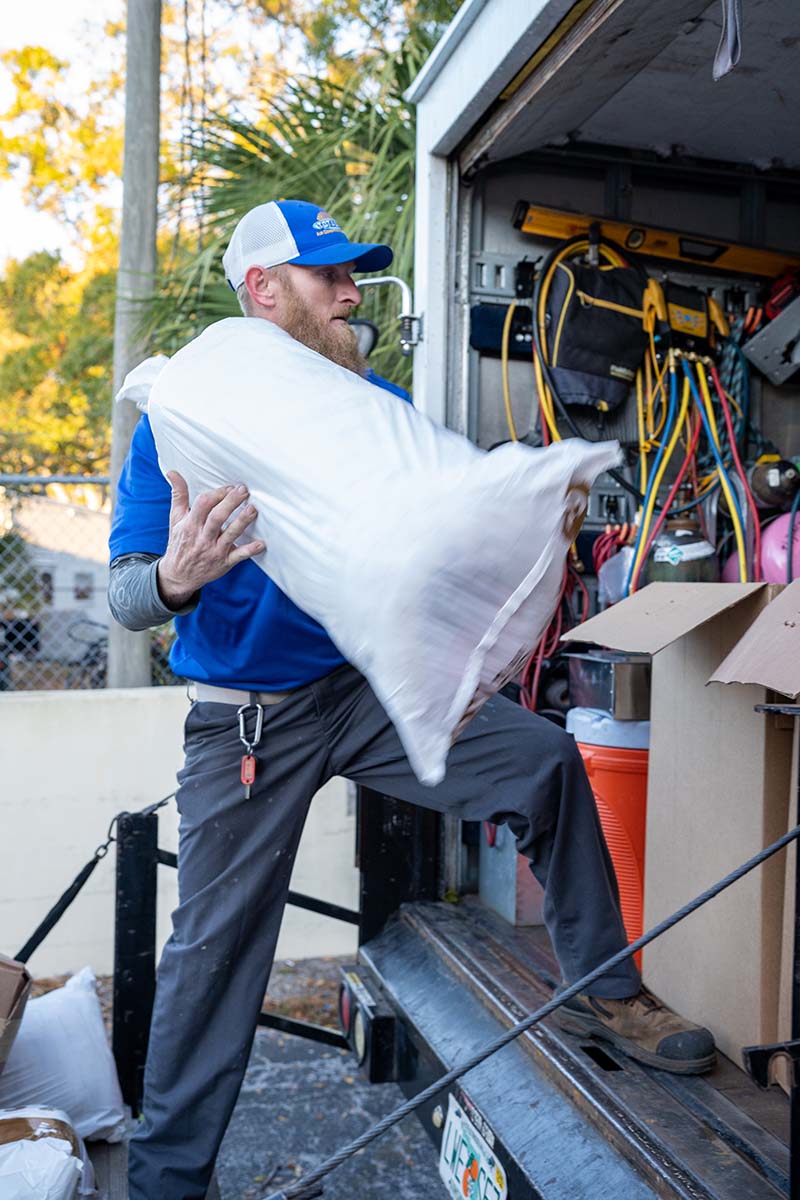
INVENTORY: Providing the necessary tools for technicians leads to an easier time taking inventory. (Courtesy of Total Air Inc.)
Golden Rule provides the technicians with the list of the needed tools, and provides a timeline in which the tools have to be purchased. If there happens to be a situation where a technician can’t afford a tool, Golden Rule will extend the time allotted for the purchase of the tool, and have a conversation with that technician regarding their bonuses or sales performance incentive fund (SPIFFs) and how they can be better utilized to purchase tools.
“Because typically, that tool will allow you to run different calls, and that gives you a better opportunity,” Paup said.
To aid the process, Golden Rule brings in suppliers to give the technicians deals and benefits towards buying the tools.
“And then we'll replace them as long as you work for us,” Paup said.
So if a technician happens to break a barrier drill on a Golden Rule job, that tool is replaced free of charge to the technician.
Since opening its Top Tech University in 2021, Golden Rule also gets tools donated, so sometimes technicians won’t have a cost associated with a tool. This is also true in the case of the large-expense tools such as vacuum machines, since the company provides those to all techs.
“All installers have it, and then we have a certain number of techs will house a certain number of those vacuum pumps for our technicians,” Paup said.
Brian Schwartze, chief operating officer at Golden Rule, said what he likes about this tool policy is that it fits really well with Paup’s philosophy of technicians investing in themselves.
“And our techs’ ability to run their own small business within a business,” Schwartze said. “And then it cuts down on the amount of tools that are left on a job site or missing.”
It removes an entire layer of red tape needed to keep track of tools.
“So it fits well, with [Paup’s] philosophy of, ‘Hey, we're going to pay you well for doing this job, and you go buy your own tools that you're going to need on a daily basis and make an investment in yourself,” Schwartze said. “So they've got some skin in the game … I thought it was a genius way to handle it.”
owner/president
High 5 Plumbing
High 5 Plumbing
For High 5 Plumbing in Denver, Colorado, the tool policy consists of the employees filling out a “Tool Program” form on their company-provided iPads, specifying what tools they think they’ll be needing. Following approval, payroll deduction options are discussed. There are a few options provided, depending on the cost of the tool(s): one scheduled paycheck, two scheduled paychecks, or three. To avoid the potential of irresponsible spending, the tool program account cannot go over a certain balance unless approved by the general manager.
“When it comes to pros, our tool program has allowed us to grow our apprenticeship program,” said Levi Torres, owner/president of High 5 Plumbing. “We also have been able to grow year-over-year in both revenue and employee size.”
The company is better able to recruit and train people in the industry because their technicians have all the tools they need to succeed.
“The only con is we wish we could equip our apprentices with a tool bag when they start,” Torres said. “Who knows, maybe there is a cool tool company out there who wants to partner with our rapidly growing apprentice program in Denver.”
If a technician were to leave the company, they would have the choice to either pay the tool off and take it home with them, or take advantage of the company’s buyback option for the tools.
“Our team is happy with this program, from our apprentices to our master plumbers who have collected tools for years,” Torres said,
Galgon HVAC
Galgon HVAC & Mechanical Service in Atlanta, Georgia, is a union outfit, and as such, it is the company’s responsibility to provide the tools for their technicians and pipefitters.
“Before a technician starts, we will tool their van with any tools we currently have in our shop,” said Brandon Galgon, project manager and executive director at Galgon HVAC. “Usually, we do not have all the necessary tools, so when a new technician starts, depending on their ability, we ask them to inform us of when they need a tool.”
If the technician is a third-year apprentice or above, all Galgon asks is that the tech take good care of the tools. If they fall below the three-year range, odds are they won’t need any tools, because the journeyman they are working with has everything they need.
The company inventories all the tools in the technician’s van on their first day on the job, and if they were to move on to another company or get fired, their van is inventoried again before they leave.
“After the ‘new’ technician has been with us for 10-12 months, they should have all the tools needed for their ability,” Galgon said. “Official policy is to notify the warehouse manager of any tool purchase to ensure we do not have it in the shop. If it not in the shop, the tool is allowed to be purchased, and the tool is assigned to their van.”
The pro of a tool policy like this is that Galgon has a chance to check that they have the tool in their shop so they aren’t double-purchasing.
Report Abusive Comment