
Figure 1. The Close on Rise of Outlet (CRO) valve is located between the compressor’s discharge line and the receiver inlet. (All artwork courtesy Sporlan Division, Parker Hannifin Corp.)
This column focuses on condenser splitting. But first, here’s a quick review of condenser flooding before covering condenser splitting to help all better understand both concepts and their advantages and disadvantages.
CONDENSER FLOODING
A pressure-actuated holdback valve is installed at the condenser outlet. This valve is often referred to as an ORI (Open on Rise of Inlet) valve. The valve will throttle shut when the condenser pressure reaches a preset minimum pressure in a cold ambient condition (Figure 1). This throttling action will back up liquid refrigerant in the bottom of the condenser, causing a flooded condition. The condenser now has a smaller internal volume, which is what is needed for a colder ambient condition. The condenser pressure will now rise, giving sufficient liquid line pressures to feed the expansion valve. Larger receivers are needed for these systems to hold the extra refrigerant for condenser flooding in the summer months.While the condenser is being flooded with liquid refrigerant, a CRO (Close on Rise of Outlet) valve, located between the compressor’s discharge line and the receiver inlet, will bypass hot compressor discharge gas to the receiver inlet when it senses a preset pressure difference between the discharge line and the receiver (Figure 1). The ‘T’ symbol means the valve comes with a built-in pressure tap for ease in taking a pressure reading for service purposes and for setting the valve. The pressure difference is created from the reduced flow of refrigerant to the receiver because of the throttling action of the ORI valve. The bypassed hot gas through the CRO valve serves to warm up any cold liquid coming from the ORI valve at the receiver’s inlet, and it will also increase the pressure of the receiver so metering devices will have the proper liquid line pressure feeding them.
One of the main advantages of condenser flooding is to keep consistent liquid pressure feeding the metering device in low ambient conditions. Manufacturers do supply technical information on how much extra refrigerant is needed for flooding a condenser for a certain low ambient condition. However, in extreme low ambient conditions, it may be necessary to flood 80 to 90 percent of the condenser. On larger systems, this could mean several hundred pounds of refrigerant. This is the main disadvantage of flooding a condenser for low ambient operations. With the rising price of refrigerant and the environmental concerns of global warming and ozone depletion, condenser flooding can become quite expensive and environmentally unsound if not managed and serviced properly.
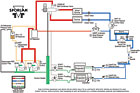
Figure
2. One way to reduce the amount of extra refrigerant charge needed for
condenser flooding is to split the condenser into separate and identical
condenser circuits.
CONDENSER SPLITTING
As mentioned above, the main disadvantage of condenser flooding is that larger refrigeration systems may hold hundreds of extra pounds of refrigerant needed to properly flood a condenser at extremely low ambient conditions. One way to reduce the amount of extra refrigerant charge needed for condenser flooding is to split the condenser into two separate and identical condenser circuits (Figure 2). This method is referred to as condenser splitting. The splitting of the condensers is done with the addition of a pilot-operated, three-way solenoid valve installed in the discharge line from the compressors (Figure 3). The splitting of the identical condensers is done in such a way where only one-half of the condenser is used for winter operation, and both halves are used for summer operation. The top half of the condenser is referred to as the summer-winter condenser, and the bottom half of the condenser is referred to as the summer condenser (Figure 2). The three-way solenoid valve controlling the splitting of the condensers can be energized and de-energized by a controller sensing outside ambient conditions, an outdoor thermostat, or a high-side pressure control.During summertime operations, the added surface area and volume of both condensers are needed to maintain a reasonable head pressure at higher ambient conditions. The pilot-operated, three-way solenoid valve is then de-energized. This positions the main piston inside the valve to let refrigerant flow from the compressor’s discharge line to the three-way valve’s inlet port, and then equally to the valve’s two outer ports. In other words, the flow of refrigerant will flow to both of the condenser halves equally.

Figure
3. The splitting of the condensers is done with the addition of a
pilot-operated, three-way solenoid valve installed in the discharge line from
the compressors.
In fact, during winter operations, the system’s head pressure is best maintained with a combination of condenser splitting, refrigerant-side head pressure controls, and air-side controls like fan cycling or fan variable-speed devices. This combination of refrigerant-side and air-side controls will minimize the refrigerant charge even more while splitting the condenser. These combinations will also maintain the correct head pressure for better system efficiencies.
The refrigerant that is trapped in the idle summer condenser during low-ambient conditions will flow back into the active system through a bleed hole in the piston of the three-way valve. This trapped refrigerant will flow through the piston’s bleed hole, into the valve’s pilot assembly, and back to the suction header through a small copper line which feeds all parallel compressors (Figure 2). Another scheme to rid the idle summer condenser of its refrigerant is to have a dedicated pump-out solenoid valve, which will open when energized and vent the trapped refrigerant to the common suction header through a capillary tube restriction. Both the bleed hole in the piston or the capillary tube ensure that the refrigerant experiences a restriction, and is mostly vaporized before reaching the common suction header which is under low side (common suction) pressure.
A check valve is located at the summer condenser’s out- let to prevent any refrigerant from entering it while it is idle and under a low pressure condition. While not needed for backflow prevention, a check valve is also located at the outlet of the summer/winter condenser simply to make the pressure drops equal in both halves of the condenser when both are being used simultaneously in summertime operations.
Publication date:05/02/2011
Report Abusive Comment