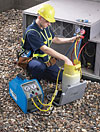
Changing laws are requiring technicians to update and educate themselves about the latest refrigerant recovery machines.
[Editor’s note: While this article discusses refrigerant recovery in general, it is based on procedures developed for the RG6000 refrigerant recovery machine from Promax.]
With each passing day, more laws around the world are prohibiting the venting of refrigerants during service work. This requires contractors and technicians to update and educate themselves about the latest refrigerant recovery machines, especially when planning to purchase one.
Recovery equipment has evolved from heavy, slow, and complex pieces of equipment, to products that are light, fast, and user friendly. Today most equipment uses oil-less compressors rather than the hermetic compressors of the past. Oil-less compressor technology has evolved over the last few years and offers many advantages: faster recovery rates, direct liquid recovery, elimination of oil maintenance, and the ability to handle multiple refrigerants.
Refrigerant recovery can take place at any one of three stages during the lifecycle of refrigeration equipment:
• During servicing, when a partial or complete refrigerant charge is removed from the system;
• When the system is converted to run with a new refrigerant; and
• Before the equipment is scrapped and disposed.
Of the three stages, conversion is rare in a system’s lifetime; the system can still operate even after a refrigerant becomes obsolete. The large refrigerant charges and climbing refrigerant costs have been the most positive incentives for recovery.
UNDERSTAND THE SYSTEM
Whether you’re working on a supermarket application with multiple compressors connected in parallel, or on an average-sized residential a/c system, the more you know about what it is you’ll be working on beforehand, the better prepared you’ll be for the job.Before getting started, first identify the refrigerant type and quantity in the system you are servicing. When recovering refrigerant from a system that has a burned-out compressor, you’ll need to use extra filtration prior to recovery to deal with any potential contamination in the oil.
However, if you know the gas in the system is relatively clean or new, you should use a new tank. This will make it easier if you plan to put the refrigerant back into the same system. It is recommended that you own at least one tank for each refrigerant type you service, plus extra tanks for burnouts and other unknowns.
Knowing the quantity of refrigerant is important for planning storage requirements, as well as planning for the actual recovery. A substantial amount of vapor can remain in the system after all the liquid is removed.
HOSES AND VALVES
Hoses and Schrader valves have a large impact on recovery speed. In general, the larger the hose, the less friction on the flow of refrigerant, and the quicker the recovery time. Many contractors and technicians are now using 3/8-inch lines for the input to the recovery machine, even if those lines originate out of 1/4-inch fittings.Another thing to remember is to use the shortest hose possible. The longer the suction hose and the smaller in diameter it is, the higher the pressure drop in the system and the longer it will take to recover the refrigerant.
Be sure to remove the Schrader valves and core depressors before every recovery job. Most wholesalers sell a tool for removing these cores while keeping the connections sealed.
One last hose consideration is the little rubber grommet at the end of the hose that makes a seal with the flare fitting. Over time these seals wear and become deformed - sometimes so worn and deformed that when the hose is connected to the flare fitting, the grommet virtually seals off the connection. This condition rarely gets noticed during charging because the pressure opens the grommet. But during recovery (or with suction), the deformed grommet severely restricts the flow of refrigerant.
Make the recovery machine’s job easier by using larger hoses with no restrictions. You will be rewarded with faster recovery rates and lower hours on your recovery unit.
KEEP THE DIRT OUT
During the recovery process, your recovery machine can be exposed to debris that can cause damage internally. This includes brazing spatter, copper/brass slivers, and acid contamination that may be in the system.To prolong the life of your machine, always use an inline filter at the inlet port. All manufacturers recommend using a new filter on every recovery job.
If you follow this simple practice and use the appropriate filter on every job, your refrigerant recovery unit should give you many years of trouble-free performance.
GETTING THE REFRIGERANT OUT
The key to a quick recovery procedure is to get the liquid out first, then get the remaining vapor out. There are three different ways to remove refrigerant from the system: push-pull recovery; liquid recovery; and vapor recovery (the most common).• Push-pull:This is a method of removing bulk liquid from a system using the pressure differential created by the recovery machine. It is commonly used on systems with a receiver tank; those with greater than 20 pounds of refrigerant; or when transferring refrigerant from one tank to another. Push-pull generally does not work on smaller systems, because there is no bulk liquid reservoir from which to create a siphon.
Before getting started using the push-pull recovery method, make sure the system doesn’t have a reversing valve that will not allow a solid column of liquid to form, and that it doesn’t have an accumulator. If either of these components exists within the system, the push-pull method cannot be used. You will need to use the liquid or vapor recovery method.
• Liquid recovery:With the advent of oil-less compressors and constant-pressure regulator valves, liquid recovery has become the preferred method, recommended by most recovery equipment manufacturers. Liquid recovery is performed the same way as standard vapor recovery. The only difference is that you connect to the high side of the system. Recovering liquid is ideal for recovering large amounts of refrigerant, such as when you transfer refrigerant, or if the system you are servicing allows you to recover liquid.
After completing the transfer of liquid refrigerant between a recovery unit and a refrigeration system, avoid trapping liquid refrigerant between the service valves.
• Vapor recovery:Vapor is drawn from the refrigeration unit into the recovery system. It passes through the compressor to the condenser, where cooling occurs. Once cooled to a sufficient temperature, the gas turns to liquid and proceeds into the storage tank. Refrigerant recovery systems operate on a temperature-pressure relationship. A lower temperature facilitates a lower pressure, therefore allowing for faster and more efficient operation.
Vapor recovery can be approximately 75-80 percent of the entire recovery process. So it’s important to use a recovery machine with a high vapor recovery rate, in addition to being good at recovering vapor at high temperatures.
RECOVERING REFRIGERANT
Before using a recovery unit, always:• Check the service valve positions.
• Purge and recover any remaining refrigerant from the unit.
• Evacuate an empty recovery cylinder before transferring refrigerant to the cylinder.
Many technicians prefer to have a digital refrigerant scale for keeping track of the refrigerant when recovering refrigerant. This is recommended for both your own service records, and for any Environmental Protection Agency audit requests.
Recovering large amounts of liquid refrigerant can sometimes involve large amounts of oil if the system lacks an adequate oil separator. If this recovered refrigerant is not going to be liquid-charged back into the same system, you might want to separate the refrigerant from the oil to measure the oil. That way, you’ll know how much oil to charge back into the system.
When working on a system that has parallel compressors, remember to isolate the parallel compressor system in order to recover refrigerant. Failure to do so will cause an open equalization connection that prevents refrigerant recovery.
Many times liquid can become trapped in the refrigeration system. A good indicator of trapped liquid in the system is frost or condensation forming on the components where the liquid is trapped. If you are unable to locate the trapped liquid, but you know it’s there because the recovery job is taking “forever,” turn on the system’s compressor (if it’s operable) for a few seconds. This will get the refrigerant moving to another part of the system, and in the process, pick up enough heat to boil off.
Another trick is to cool the tank, if it is partially filled, prior to or during recovery. This will lower the pressure in the storage tank and therefore speed up recovery. There must be a minimum of 5 pounds of liquid refrigerant in the tank you wish to chill.
There is no magic here - you are simply using your recovery machine to make a refrigerator where the tank is the evaporator. Five to 10 minutes of chilling produces some very dramatic tank cooling, depending on conditions. The greater the quantity of refrigerant in the tank, the longer the process will take.
FINISHING THE JOB
After the refrigerant has been removed, and before the system is ready to receive the new refrigerant, use a vacuum pump to remove moisture and air from the system. Systems today are built tighter, so accurate charges become critical. This means these systems have a greater sensitivity to moisture and other contaminants, making thorough evacuation very important.Most systems are not “recovery friendly.” Many lack access ports at their lowest points. Significant time can be saved, especially on maintenance contracts, by simply installing access ports at all of the lowest points in the system where liquid is likely to accumulate. Since most systems lack such ports, you need to be prepared to boil off the trapped liquid with a heat gun.
If you are using your recovery equipment to recover multiple refrigerants, remember to purge the recovery equipment. Most recovery equipment today comes with an automatic purge feature, which clears out the machine and gets the equipment ready for the next job.
Safety is always a concern when recovering refrigerant. Always wear safety glasses and gloves to keep debris from getting into your eyes and prevent frostbite on your hands. If you understand the system you’re working on and adequately prepare by using the right tools for the job, the recovery process will go much faster and problem free.
For additional refrigerant-related articles, visit The NEWS’ HVACR In-Depth page.
Publication date:05/17/2010
Report Abusive Comment