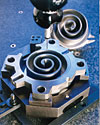
Admittedly, there were distinct issues that had to be resolved in order to introduce and bring the versatile Copeland Scroll design to the HVACR industry - including introducing it to new markets and achieving new levels of performance.
“I think, in hindsight, people don’t realize how difficult the task was,” stressed Matt Diggs, former Copeland Corporation president (1975-1981). “The stakes got higher once the opportunity got bigger.”
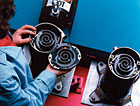
Significant investments in engineering and R&D were key
to the success of scroll technology.
HURDLE #1: DESIGN AND DEVELOPMENT
In the eyes of Robert J. Novello, the key to the evolution of scroll was in the company’s engineering department. To this day, the former chairman and CEO of Copeland Corporation (1987-1997) has nothing but glowing remarks regarding the company’s engineering team.“Our engineers kept us focused on the importance of scroll,” said Novello. “Our engineers were true believers. So, I’d say a lot of our confidence in moving forth with the technology was due to having terrific engineering people, who were totally committed and who were unbelievably creative.”
Novello had to chuckle before adding, “I used to call it ‘open-field running.’ When we got in trouble, we had a lot of open field runners that helped us through issues.”
In addition to competent engineers, all agreed that a cooperative management team was essential.
“The management involvement in this program across the entire organization - finance, operations, engineering, et al - was very high,” said Purvis. “There were 7:00 morning meetings every week, where we went through all the project details. Everyone asked a lot of tough questions, and I think it was essential to addressing the uncertainty around the project.”
HURDLE #2: HIGH PRODUCTION VOLUME AND MAINTAINING EFFICIENCY LEVELS
A just-as-demanding obstacle to overcome involved maintaining efficiency levels in the production of Copeland Scroll. Novello termed it “our most challenging job.”“We thought reliability was going to be an issue, but it wasn’t. The product was so robust, it amazed us,” he said. “In fact, shortly after we launched the first scrolls, our engineers told us that our scroll elements were designed to get better with use. They said they ‘wore in, not out’ and they proved this in the labs. And that was great news!”
Yet, keeping efficiency levels on an even keel at each facility was a different story. Novello recalled ramping up the product, but noted that minor changes needed to be made along the way.
“We’re talking about maintaining machining accuracy on the scroll elements to be within unheard of levels at the time,” he said.
Under the umbrella of manufacturing, Novello was responsible for pushing for the “franchise” concept.
“In one of our 7:00 meetings, Bob came in saying ‘We ought to have a scroll franchise factory,’ ” said Dean Ruwe, who joined Copeland in 1981 as vice president of operations and was also a former president and chief operating officer (1997–2003).
Though Ruwe gave credit to Novello for initiating the idea, Ruwe was responsible for making the idea become reality.
“Dean Ruwe came up with a program where he had a book for each one of the critical elements,” explained Novello. “When we started a plant, he had measurements in place. You had to cross these certain, specific paths within a certain amount of time. And, the plant could not go to the next step unless it did certain things. When we did this, we established a base for launching multiple plants around the world.”

The growth of Copeland Scroll led to the company opening
manufacturing facilities around the world. To date, there are 10 facilities,
globally, dedicated to the production of Copeland Scroll.
TAKING CARE OF (GROWING) BUSINESS
Late in 1987, Copeland began producing its new Copeland Scroll compressor at the facility in Sidney, Ohio. This event marked another milestone for Copeland, since it was the first American manufacturer to produce scroll compressors for the residential air conditioning and heat pump market.It wasn’t long before several large original equipment manufacturers (OEMs) adopted Copeland Scroll into their residential products – some of them even deciding to use scrolls in one hundred percent of their lines. Soon thereafter, most of the major OEMs recognized the benefits and bought into the technology.
“When Rheem made the decision to be a hundred percent with Copeland Scroll, it put us under a lot of pressure,” said Tom Bettcher, CEO, Emerson Climate Technologies. He quickly added, “It was always a challenge to get the capacity close to the demand - and that was a stress point. Once we got through those early unpredictable years, we were able to focus our investment on keeping capacity ahead of customer demand.”
In addition to raising compressor technology to new levels, Copeland simultaneously started two other strategic moves to prepare for the future. One concentration was its effort to create new manufacturing technology and develop focused facilities; the other task-at-hand was building on the company’s early and positive response to the developing global marketplace.
The versatility of the scroll design meant that it had limitless possibilities - and Emerson never tired in its quest to take Copeland Scroll to new markets and new levels of performance. Included in the mix were modulation; Copeland Scroll Digital and Copeland Scroll UltraTech; five generations of Copeland Scroll design improvements and new refrigerants. And the new markets included commercial air conditioning, refrigeration, transportation, industrial, and medical.
As an example, the introduction of the refrigeration line of Copeland Scroll compressors in 1994 provided the benefits of an advanced design and smooth compressor cycle for use in commercial refrigeration equipment for supermarkets, restaurants, convenience stores, hotels, and industrial applications. Today, the refrigeration Copeland Scroll line spans from two to 15 horsepower.
“There are new markets in refrigeration that we weren’t addressing with reciprocating technology,” Purvis said. “Now, because of the many scroll advantages for refrigeration, we can explore these new and emerging opportunities.”
Even though global expansion efforts began in the 1980s, Copeland’s growth in global markets grew at a rapid pace from 1994 through the end of the decade. Among other accomplishments, Emerson opened new manufacturing facilities in Welkenraedt, Belgium, in 1995; Rayong, Thailand, and Cookstown, Northern Ireland, in 1997; and another Asian facility - in Suzhou, China - began operations in 2000. End result: The company was able to quickly ramp-up these scroll facilities in key markets to meet the increasing demand for products all over the world.
“The financial impact was huge because if you go back to the first Sidney plant, it probably took us five to six years of losses before we became profitable,” said Bettcher, noting the Lebanon, Missouri, facility “was in the three-year range.”
In addition to capturing OEM approval, contractor preference for scroll technology today is almost undeniable.
“We did some research that showed two-thirds of the contractors preferred to install a scroll-bearing air conditioning or heat pump system,” said Scott Barbour, president of Emerson Climate Technologies Air Conditioning division. “We saw that they preferred to install a scroll-bearing unit because they had a better chance of getting it right the first time, with very few callbacks. It was very reliable.”
Reliability still plays a key role in driving contractor preference. At the same time, ever-changing energy and environmental regulations have made it vital that technologies like Copeland Scroll continue to innovate.
“Once again, there is an energy crisis that will drive demand for Emerson’s high-efficiency products,” summarized Ruwe.
Publication date:11/12/2007
Report Abusive Comment