Last month's article described the history and fundamental physical characteristics of CO2 as a refrigerant, and presented some typical systems used in industrial applications. (See "CO2 in Refrigeration Applications," Oct. 6.)
It is now appropriate to discuss system compatibility considerations: oils, the effects of water, leak potential, and safety.
Oil In CO2 Systems
Either miscible or immiscible oils may be used in CO2 systems with traditional refrigeration compressors. In CO2 systems with immiscible oil such as PAO (polyalphaolefin), the oil management system is rather complicated. Oil filtration requirements are high, and the separation of oil from CO2 is complicated by the fact that the oil is less dense than CO2.In CO2 systems with miscible POE oil (polyolester), oil management system requirements are simple in comparison. The challenge in POE systems is the stability of the POE oil. A comparison for PAOs and POEs may be found in Table 1.
In CO2 "brine" systems, and in pump circulating systems with oil-free compressors, there is no oil present in the circulated CO2. From an efficiency point of view, this is an optimum solution because of good heat transfer coefficients in the evaporators. However, it requires that all valves, controls, and other components be able to operate "dry."

Component Size, Refrigerant Charge
Due to the thermodynamic properties of CO2, in particular the relatively high pressure level, compressor capacity is significantly higher for CO2 than it is for NH3. The pipe dimensions for the vapor lines are smaller, but are larger for the liquid lines.European standard EN 378 classifies CO2 as an L1 nontoxic, nonflammable refrigerant, while ammonia is classified as an L2 toxic refrigerant. Even though NH3 has been used for many years, requirements have become more restrictive in recent years, particularly in some European countries. There is, therefore, a great interest in minimizing the NH3 charge.
A CO2-NH3 cascade system is considered a perfect solution, with the NH3 used being limited to a small charge that can be contained in a special machinery room that meets the necessary safety requirements. The CO2 is then distributed to all coolers.
Materials Compatibility
Unlike NH3, CO2 is compatible with almost all common metallic materials. When using copper or brass, there are no restrictions from a compatibility point of view. The compatibility of CO2 with polymers is much more complex.Because CO2 is an inert and stable substance, chemical reactions with polymers are not a concern. Rather, physiochemical effects such as permeation, swelling, and the generation of cavities and internal fractures are the main issues. These effects are related to the solubility and diffusivity of CO2 in the actual material.
Danfoss laboratories have carried out a number of tests to ensure that components released for use with CO2 can withstand the effects of CO2 under all conditions. The tests have shown that for use with CO2, modifications have to be made on some products. The solubility of CO2 in some polymers must be taken into consideration. Some commonly used polymers are not compatible with CO2; others (such as sealing materials) re-quire different fixing methods.
When pressure is close to the critical pressure and the temperature is high, the impact of CO2 on polymers is much more pronounced. Those conditions, however, are not important in industrial refrigeration, where pressures and temperatures are lower.
Water
In NH3 systems, it is well known that there are reaction problems with oil, oxygen, water, and solid contaminants. These problems are all handled by frequent oil changes and air purges. Compared to NH3, CO2 is less sensitive, but problems may occur if water is present.CO2 system pressure is always greater than atmospheric pressure; therefore there are not the same risks of water and air penetration at a leak as there are, for example, in NH3 systems. However, permeation of water into the system is still possible.
Figures 1 and 2 compare water solubility for CO2 and R-134a.
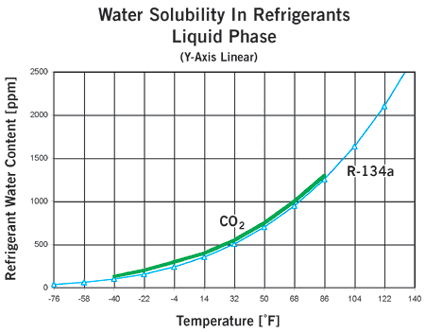
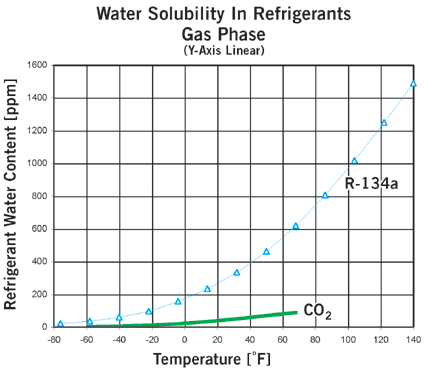
At the high pressures found in a CO2 system, how can water enter?
The amount of water that can be tolerated is much lower for CO2 systems than for systems with more common refrigerants. The curves in Figure 3 plot dewpoint versus refrigerant water content. If the water content exceeds that at the dewpoint (above the curve for a given refrigerant), and the temperature is lower than 0ÞC, the water will freeze, creating a risk of blocking control valves and other problems. The water can be removed very easily by mounting a drier in the system.
Driers are very efficient in CO2 systems, and are normally mounted in the liquid line to avoid creation of any unnecessary pressure drops.

Leaks, Safety Valves
The most critical leak location in a CO2-NH3 cascade system is in the heat exchangers between CO2 and NH3. The pressure of the CO2 will be higher than that of the NH3, so the leak will occur in the NH3 system, which will therefore become contaminated.Ammonium carbonate, a solid substance, forms immediately when CO2 is in contact with NH3. Ammonium carbonate is corrosive.
Because the triple point of CO2 is at a much higher pressure than for any other common refrigerant, the formation of solid CO2 can occur. If a safety valve is mounted in a CO2 system at (for example) 50 bar, the pressure in the downstream (outlet) line from the safety valve will pass the triple point at 5.2 bar. Below the triple point, CO2 will change from a mixture of liquid and vapor into a mixture of solid and vapor.
The formation of solid CO2 in the downstream line can, in the worst case, block the line. The most efficient solution to this problem is to mount the safety valve without an outlet line, thus blowing directly into the atmosphere. The phase change of the CO2 does not take place directly in the valve, but just after the valve, and in this case in the atmosphere.
Safety Concerns
As previously mentioned, CO2 is classified as a nontoxic refrigerant. Unlike NH3, CO2 has no distinctive odor.CO2 is denser than air (approximately twice as dense at atmospheric pressure). That means it will collect in low places, which can be dangerous, especially in pits or confined spaces. It displaces air, causing a lower concentration of oxygen.
Due to the acidic characteristics of CO2, local irritation of the mucous membranes of the nose, throat, and eyes may occur; coughing may be induced.
Symptoms associated with the inhalation of air containing carbon dioxide are listed below, with increasing carbon dioxide concentrations:
(Note: The data values are for adults in good health.)
The OSHA safety requirements specify a Threshold Limit Value (TLV) of 5,000 ppm for CO2 and a TLV of 25 ppm for NH3.
Conclusion
Availability is good for components of industrial CO2 refrigeration systems with pressures up to approximately 30 bar.Several equipment manufacturers of traditional refrigeration systems can also supply some components for CO2 systems.
Availability is limited for components for higher-pressure industrial CO2 refrigeration systems, and the availability of critical components is an important factor in the growth rate of CO2 applications.
In industrial refrigeration, CO2 will not replace ammonia. Industrial CO2 systems are all hybrid systems that require ammonia on the high-temperature side of the system, but with a smaller ammonia charge.
Vestergaard is R&D manager for Danfoss Industrial Refrigeration; Robinson is in technical communications in the Air-Conditioning & Refrigeration Division, Danfoss Inc.
Publication date: 11/03/2003
Report Abusive Comment