To complete a boathouse metal roof design in northern Wisconsin last summer, quality design, materials and craftsmanship came together to create an attractive, watertight system.
“We really wanted this structure to go away from a distance and be a pleasant surprise as you got closer,” says Douglas Kozel, AIA, founding partner at KEE Architecture of Madison, Wisconsin. “The color, texture and material helped with that. It’s supposed to be a modest structure despite the great amount of detail.”
Kozel selected metal roofing for this project to allow for the shedding of snow and other debris, like pine needles. The installation required a specialized crew in Lou Rondeau, owner of Natural Metal Associates of Mont Vernon, New Hampshire, along with team members Keith Rondeau and Mark Melone. They journeyed to Wisconsin and were on the job about six weeks, installing the roof.
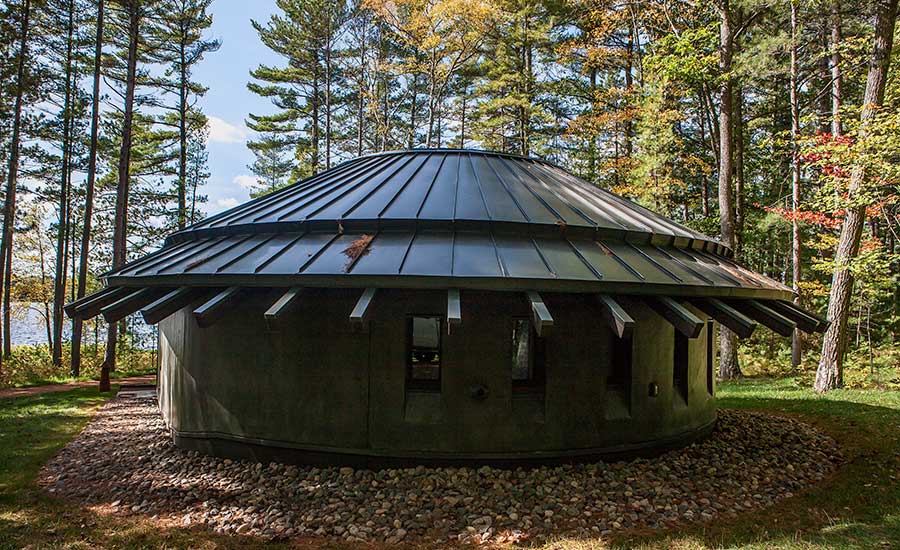
The zinc specified for the roofing panels and trim came in prePATINA Graphite-Grey from RHEINZINK, supplied and fabricated by Sheet Metal Supply of Mundelein, Illinois.
“As fabricators, we appreciate and enjoy a project with an exceptional mix of materials that combine for a most unique aesthetic,” says Ben Kweton, CSI-EP, of Sheet Metal Supply. “KEE knocked it out or the park and delivered a fabulous design. The material selections, in relation to that design intent for the building, blended perfectly into the environment. The craftsmanship of everyone onsite who was a part of the project ensured its success.”
Graphite-Grey is the only Type 2 zinc available to architects and installers. It’s an alloy that will generally weather darker than its peers, given the same environmental factors. RHEINZINK’s prePATINA line is durable, low-to-no maintenance and 100 percent recyclable.
Natural Metal Associates installed 2,282 square feet of mechanical lock standing seam, 773 square feet of radiused mechanical lock standing seam and 1,235 linear feet of flashing material.
The installation of RHEINZINK products started with the rafter tails at the eaves. They match the rafter tails on the residential garage on the property, and each wooden rafter tail was fitted with a single piece of Graphite Grey zinc that covers the top and sides.
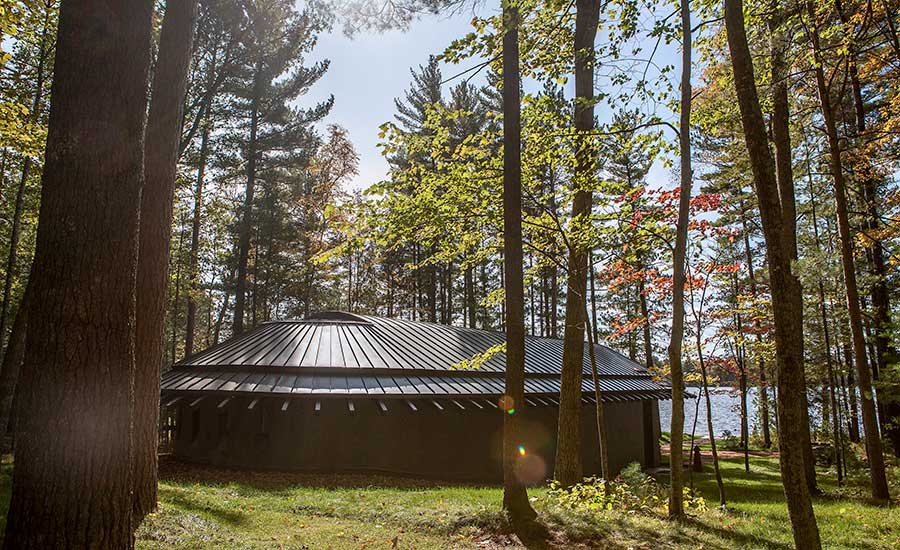
The roof features a step about three feet up from the eaves and curves over the top to the opposite side. The step allows for the adding of insulation under the roofing above the overhangs, where insulation is not needed.
Panels were installed starting in the front, working toward the rounded back of the building where panels were tapered to form a low-slope cone-shaped roof. Panels were formed and radiused at Sheet Metal Supply and delivered to the jobsite. Tapered panels were measured and cut to fit by Natural Metal Associates.
“We installed the bottom part of the step first and formed the top of the panel up the step,” Lou Rondeau says. “We married that panel into a panel at the top of the step for a watertight system; again, being careful to match up the seams.”
The final satisfying part of the project Rondeau says was its completion.
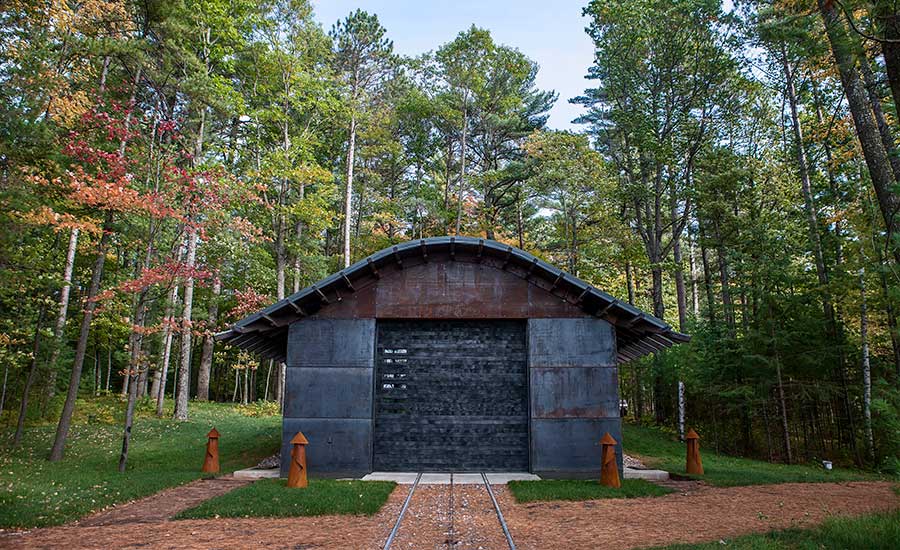
“We are a small company that loves to travel,” he says. “We want to do calendar-worthy projects. We love to do fun, unique jobs, to put our mark on the industry. When it’s all done and you get to see it, that’s when you realize all the time-consuming work was worth it.”
This story originally appeared in the February 2020 issue of SNIPS magazine.
Report Abusive Comment