To finish the job they were working on last week (see "Btu Buddy 24: Looking At A Heat Pump Drawing A Lot Of Power"), Bob meets Btu Buddy at the jobsite to change the heat pump's four-way valve on a cool but dry day. It's a good day to work outside. Bob knows that it is best to only open a refrigeration system on a dry day, and it is much better when it is not too cold so that it is comfortable to work outside. Btu Buddy asks Bob what he thinks the best procedure would be to change the valve.
Bob says, "We will have to recover the refrigerant, then turn off and lock out the power supply, and then remove the top of the unit so we can get to the valve. We should then break the vacuum after recovery with dry nitrogen. Then I think we should use the multi-tip torch to remove the piping from the valve. We will have to do it one pipe at a time because there are four pipes. Then we can install the old piping to the new valve in reverse manner. Is that what you would do?"
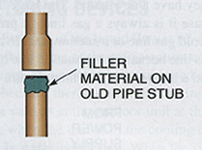
"There are two ways that technicians deal with this. One is to file the hard solder off of the ends and it is very hard to get this filing done all the way around the pipe. The pipe must be filed to the original size for it to fit the new valve. Another way that technicians handle this is to simply heat the pipe and the valve connection and slide them together. Often times this is very hard to do without overheating the valve. The valve has a fiber seat inside that can be ruined with excess heat. Melting the piping solder back into the valve is very hard to do and requires some real expertise. The third method, and I think the preferred method, is to cut the pipe back like I mentioned. Then put couplings in the pipe with short stubs of piping. There are more connections to solder, but you will be soldering fresh connections that are much easier to work with (Figure 2). You can do all of the fitting of the pieces outside of the unit. You can even solder in the stubs outside of the unit if you want. However, it is just as easy to do it all at once in the unit."

Btu Buddy then suggests, "You have had the piping open for a fairly long time. Don't you think you should install a two-way drier in the liquid line?"
Bob says, "Yes, I think you are right."
Btu Buddy then says, "It always pays to keep a system extremely clean. Especially since heat pumps operate below freezing, it pays to keep them dry. You have the valve ready to braze in place. Next, use dry nitrogen to flush out the system, then replace the liquid line drier and you will preserve the capacity of the drier."
Bob lets the nitrogen trickle slowly through the system and installs the flare connection drier. He could feel nitrogen puffing out both connections to the drier so he knows that the system is clean and dry. He is now ready to solder in the four-way valve and stubs.
Btu Buddy tells Bob, "Let's protect this four-way valve from heat using an old fashioned method. Get a small pan of water and some cloth strips from your service truck."
Bob asks, "What are we going to do?"

Bob then releases all nitrogen pressure on the system, opens it to atmospheric pressure, solders all of the connections, and immediately reconnects the nitrogen to prevent an intake of air as the piping cools and contracts the nitrogen in the system. He then raises the system pressure to 20 psig using R-22 (the approved trace refrigerant) and then raises the system pressure to 150 psig using nitrogen.
Btu Buddy then says, "This system had no sign of low refrigerant charge and has not had refrigerant added in a long time, so we can assume that it is leak free, except for the connections that you made. So leak checking will be easy."
Bob leak checks the system and then lets the nitrogen and trace refrigerant go to the atmosphere. He then connects the vacuum pump and starts it running. While it is running, he installs the valve coil. A low vacuum (300 microns) is obtained in about 30 minutes. Bob says, "That really was fast."
Btu Buddy explains, "You used good working habits with nitrogen and there was no moisture in the system. You also used large vacuum pump connections. These cost a little more, but really speed up the job and pay for themselves in time saved."
Bob then uses scales and measures the correct charge back into the unit. He starts the unit. He then uses the "O" wire that controls the four-way valve and causes the system to change back and forth from heating to cooling several times to make sure the valve is functioning properly. He then removes his gauges and replaces all the panels. He goes to the room thermostat and sets the system back to normal heat.
As they are riding away from the job, Btu Buddy asks, "What did you learn from this job?"
Bob says, "That there is more than one way to do a job. I liked using the stubs on the four-way valve to protect the valve body. The water and cloths were a great idea. I know there are other heat sink paste-type materials, but this proves that the job could be done correctly without them in case a technician didn't have them. I also learned that using nitrogen while making high temperature connections made a much cleaner job and protected the system."
Btu Buddy says, "These are old fashioned solutions that have worked for years. A technician should always treat every system like a low temperature refrigeration system and the system will have a long-term healthy life. Many technicians are careless with moisture and air in a system. The system will work above freezing but it will not provide a long life. It always pays to do your best work."
Bill Johnson has been active in the HVACR industry since the 1950s. He graduated in gas fuel technology and refrigeration from the Southern Technical Institute, a branch of Georgia Tech (now known as Southern Polytechnic Institute). He taught HVAC classes at Coosa Valley Vocational & Technical Institute for four years. He moved on to become service manager for Layne Trane, Charlotte, N.C. He taught for 15 years at Central Piedmont Community College, part of this time as program director. He had his own business for five years doing installation and service work. Now retired, he is the author of Practical Heating Technology and Practical Cooling Technology, and continues as a co-author of Refrigeration & Air Conditioning Technology, 5th Edition, all published by Delmar Publishers. For more information, he can be reached at 704-553-0087, 704-643-3928 (fax), or bmj@myexcel.com.
Publication date: 04/18/2005
Report Abusive Comment