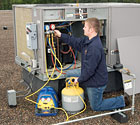
Newer recovery units are able to do far more than their predecessors. (Feature photos courtesy of Ritchie Engineering Co., Yellow Jacket Products Division.)
It has been more than two decades since the first refrigerant recovery unit came to the HVACR market and became part of the tool arsenal for service technicians.
Over that time, two things have become clear: Even a repairable unit doesn’t last forever and the newest units are able to do far more than their predecessors.
Said Tim Naylor, sales manager for RefTec International Systems, “Recovery equipment generally needs replacing/rebuilding when the recovery rate diminishes due to deterioration of the compressor seals.”
As noted by Mary Jo Gentry, marketing communications manager for Ritchie Engineering Co., Yellow Jacket Products Division, “Although most units now are field replaceable, technology changes pretty quickly. If you have your recovery unit for two to five years, you may want to consider replacing the equipment.”
While manufacturers say there is no “rule of thumb” when it is time to replace, they agree that after a couple of years, it would be good to make sure the unit is operating as close to optimum as possible. And if not, it is possible that, as Naylor noted, “Rebuilding may add some years to the unit.
“Over the last decade, units have been designed with higher quality components which lead to longer life.” He also noted, for example, that his company’s units “can be rebuilt down the road for a fraction of the price of buying new.”
Gentry did add that the life span of any recovery unit depends “on how hard you use them.”
WHAT'S OLD
Recovery units surfaced in our industry in the 1980s. They came about, recounted Don Bowman of the eHow.com website, “when it was discovered that chlorofluorocarbons were depleting the ozone layer. Once this was discovered, CFCs were taken off of the market and maintenance facilities were advised that they needed to have a way of capturing (refrigerant) when extracted. It became illegal to release it into the atmosphere. The recovery machine was quickly developed and certification course was necessary to own and operate one at a shop.”When recovery units were first introduced, they were new kids on the block subject to a bit of trial and error. In the early days, some contractors tried to build their own units in their backyards, some units came over from the automotive sector which had to recover refrigerant ahead of stationary mandates, and still others seemed to have been thrust onto the market just so a contractor could say they had a unit as mandated by the U.S. Environmental Protection Agency (EPA).
Over the years, reputable and established companies, such as those quoted in this article, have developed units that do what the manufacturers say they do - and those manufacturers stand behind their products.
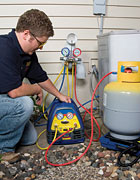
With rising costs of refrigerants and ever more cost-conscious customers, being able to reuse recovered refrigerant is especially important.
WHAT'S NEW
Changes have come as the result of newer and better ways to do recovery and to deal with new refrigerants such as HFCs and new lubricants such as POEs.“The newer equipment allows you to do some of the higher pressure refrigerants like HFC-410A,” said Gentry. “Equipment manufacturers have come a long way in making R-410A and other refrigerants easier to deal with.”
Noted Naylor, “Newer recovery equipment should be able to recover a wide range of refrigerants such as R-410A, HCFC-22, and HFC-134a. They should be lightweight, quiet, and durable. Newer recovery equipment should also be offered with low pressure shut-off switches and float cables to add an extra layer of safety.”
Gentry agreed with the need for such newer elements as part of a recovery unit. “Automatic shut-off and restart will allow the technician to do other work on the property to not have to babysit the unit. The automatic shut off and restart will extend the life of the compressor since it is not running any longer than it needs to.”
A PRACTICAL REALITY
The early days of recovery came about as a way to avoid venting refrigerant to the atmosphere and avoid fines levied by the EPA.Now with the rising cost of refrigerants, cost consciousness is paramount especially since recovered refrigerant can be reused over and over again - and more than likely that refrigerant is the least expensive a contractor has in his inventory.
Publication date:03/07/2011
Report Abusive Comment