ERV AND HOW IT WORKS
According to the Air-Conditioning and Refrigeration Institute (ARI), there are three different methods to precondition outdoor air: heat pipe heat exchangers, plate heat exchangers, and rotary heat exchangers.Rotary heat exchangers, often the common choice of manufacturers, are enthalpy wheels consisting of sections of an energy transfer matrix coated with a desiccant, usually silica gel. The wheel rotates between the incoming outdoor supply air and the building’s exhaust air. It is positioned so the outdoor supply air and exhaust air from the building travel through it in opposite directions through separate isolated ducts.

Rotary heat exchangers are enthalpy wheels consisting of sections of an energy transfer matrix coated with a desiccant that rotates between the incoming outdoor supply air and the building’s exhaust air.
In the winter, the process reverses with the matrix warming and humidifying the supply air. (See Fig. 2) The result is preconditioned air that is cooled and dehumidified in the summer, and warmed and humidified in the winter. The wheel generally recovers 70 percent of the difference between the incoming and outgoing airstreams.
This highly efficient preconditioning essentially eliminates the burden of conditioning outdoor air from the DX system.
Accordingly, the ERV system is performing work that is no longer required by the mechanical system and performs that work more efficiently. According to ARI, DX/ERV systems are up to 40 percent more energy efficient. Additionally, a DX/ERV system requires less mechanical capacity, lowering DX system cost that offsets most, if not all, of the ERV system cost.

Figure 1. Preconditioned air in the summer is cooled and dehumidified. (Click on the illustration for an enlarged view.)
ERV'S NEW POPULARITY
So given these benefits, why hasn’t ERV technology been a bigger success in the past and why has it become so popular lately?“When ERVs were originally released on the market, they were not reliable,” said Joe Finkham, general manager of ERV, Micrometl, the company that assembles ERV units for major DX manufacturers.
“Installations were generally done as retrofits and the science of matching an ERV with a DX system was far from precise. One could easily miscalculate and lose control over building space temperature, and many installations did.”
Ted Cherubin is Carrier’s marketing manager for package rooftops and he agrees with Finkham.
“Reception for ERV was poor for many years,” he said. “Engineers did not understand the technology and perceived it to be ‘black art,’ even when it was successful. Originally, all we had were paper simulations that weren’t very credible, whereas now we have sophisticated software-modeling tools. ERV was also sold as a separate unit and engineers don’t usually like to take one unit, combine it with another, and hope it gets assembled correctly on the job. We’ve now pre-engineered much of the DX/ERV system, which greatly simplifies the engineer’s job and increases the reliability.”
Technology on the component itself has also improved increasing the reliability of the system. According to Randy Steele, general manager, Airxchange, energy recovery wheel manufacturer, “The original ‘heat wheels’ were almost impossible to maintain leading to a large number of failures in the field. If there was ever a problem with those wheels, you couldn’t clean them or fix them. We’ve worked to improve reliability by creating a segmented design that enables easy removal of the energy transfer matrix for replacement or cleaning. We’ve also vastly improved bearing life and added low maintenance stretch belts to improve reliability.”
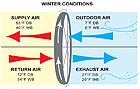
Figure 2. Preconditioned air in the winter is warmed and humidified. (Click on the illustration for an enlarged view.)
INCENTIVES FOR USING ERV
New standards from the American Society of Heating, Refrigerating and Air-Conditioning Engineers (ASHRAE) and from local communities for higher percentages of outside air in commercial buildings have provided a big motivation for engineers to look more closely at ERV.“You have to provide 15 to 20 cubic feet per minute per person,” said Finkham. “So in a school classroom of 30 students, the standards would dictate a minimum of 450 cubic feet of outside air per minute. However, the outdoor air can’t be dumped into the space without conditioning. By preconditioning the supply air, you are effectively increasing the capacity of the DX system to meet the increased requirement for outdoor air. This capability has made a lot of engineers and contractors consider ERV technology as an easy and cost-effective way to increase capacity to meet new standards.”
Then there are the financial incentives. The most obvious one is rising energy costs.
“Because the ERV wheel takes load off the DX system and uses very little energy, it significantly increases system efficiency, as much as 40 percent. The size of the DX system is then reduced because of the work the ERV is performing,” said Cherubin.
“That means less cost up front and lower energy bills instantly. Depending on the climate, the payback period can be very rapid. If you’re in an ideal climate like San Diego, it could take several years. But if you’re in Mississippi, payback should be almost instantaneous.”
“One financial incentive was the Energy Policy Act of 2005,” said Walt Jacobe, commercial marketing manager for York® Unitary Products of Johnson Controls. “It set up tax credits for energy savings. If you can show you have reduced energy consumption, you are entitled to an IRS tax credit. Then there are the utilities. Many of them offer tax rebates when you can show increased efficiency.”
There are also environmental reasons for including ERV with a DX rooftop system to aid in achieving Leadership in Energy and Environmental Design (LEED).
“More and more engineers and architects are trying to achieve LEED certification, and using rooftops packaged with ERV makes an important contribution towards that goal by increasing ventilation and improving energy efficiency,” said Jacobe.
STATE OF ERV TODAY
ERV systems are now recommended by the Department of Energy and by the Environmental Protection Agency. The General Services Administration mandates the use of ERV in their building through their standard P100.ARI implemented standard 1060, which verifies the effectiveness of the wheels, eliminating many unknowns. The association has also published Guideline V which demonstrates the impact of ERV on EER as well as the work performed by an ERV in a DX system.
“In the last five years, the new ARI standards and recommendations by the government have vastly improved the credibility of the technology,” said Steele. “The technology has been endorsed and performance verified by respected agencies for the contributions it can make to energy efficiency and IAQ,” said Randy Steele of Airxchange.
“Now that the DX manufacturers are offering ERV as a standard option in a single package, many of the reliability issues are no longer an issue,” said Cherubin. “Our computer programs combined with those provided by Airxchange enable us to quickly and easily properly size a system to fit a space.”
THE END USERS
Doug Cepuran is an energy management specialist for Florida Power and Light. He counts ERV as one of his primary tools in making Florida businesses more energy efficient.“One of the biggest reasons for our success is the way we help our customers achieve greater energy efficiency,” he said. “We call it Demand Side Management and ERV is a big part of our efficiency program.”
“We’ve done our Demand Side Management program with our customers for a long time. It’s especially effective in new stores. Not only does ERV precondition the air and filter out pollen and molds because the preconditioning takes a load off their air conditioning units, they are able to use smaller systems to accomplish the same job. Many tell us that the payback on their ERV installations is instantaneous,” said Cepuran.
With more and more government agencies and communities mandating ERV usage and with higher demand for outdoor air, it looks like the time for DX-ERV systems has arrived.
Publication date:03/19/2007
Report Abusive Comment