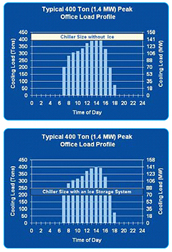
LOWEST FIRST COST
Systems with ice thermal storage can be installed at the same or lower first cost than traditional systems when designed with the colder supply water available from ice. The savings that result from the use of smaller chillers and cooling towers, reduced pump and pipe sizes, and less connected horsepower, offset the cost of the ice thermal storage equipment. Additional savings can be found when using lower temperature air distribution, which allows reduced ductwork and fan sizes.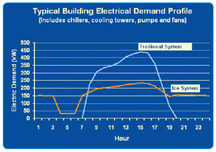
REDUCED ENERGY COST
An ice thermal storage system reduces peak demand, shifts energy usage to non-peak hours, saves energy, and reduces energy costs.1. Although making ice requires more energy than producing chilled water, the efficiency penalty is not as large since the ice is made at night when condensing temperatures are lower, increasing the efficiency of the chiller.
2. Ice systems typically operate the chiller at full load. Chillers are inefficient when run with low loads during the spring and fall. A typical chiller will operate at less than 30 percent capacity for half the year.
3. Reduced pumping horsepower.
4. Reduced fan horsepower due to lower air pressure drop across the cooling coil. A higher chilled water temperature differential across the cooling coil usually results in fewer rows and therefore a lower pressure drop.
5. The ability to recover waste heat from the chiller for heating water both night and day.
Additional kWh savings are possible if the air distribution is designed to take advantage of the low temperatures available from the ice storage system. As the electric industry continues to deregulate, and time-of-use rates, real-time pricing schedules, and negotiated power prices become standard, ice storage can provide even greater future savings in operating costs.
VARIABLE CAPACITY
The ice thermal storage system will maintain a constant supply temperature regardless of the variations in instantaneous cooling demand. The flow and entering water temperature set the instantaneous capacity.
IMPROVED SYSTEM RELIABILITY
Ice storage systems provide the reliability necessary to ensure air conditioning is available. With traditional systems, installing multiple chillers provides redundancy. In the event of a mechanical failure of one chiller, the second chiller provides limited cooling capacity. The maximum available cooling for the traditional system would only be 50 percent on a design day.Most ice storage systems utilize two chillers in addition to the ice storage equipment. Two chillers are designed to provide approximately 60 percent of the required cooling on a design day while the ice storage provides the remaining 40 percent of the cooling capacity. In the event only one chiller is available to provide cooling during the day, up to 70 percent of the cooling capacity is available. The one operable chiller provides 30 percent of the cooling requirement while the ice provides up to 40 percent. Based on typical HVAC load profiles and ASHRAE weather data, 70 percent of the cooling capacity would meet the total daily cooling requirements 85 percent of the time.
REDUCED MAINTENANCE
The ice thermal storage coils have no moving parts so very little maintenance is required. Because the chillers, pumps, and heat rejection equipment are smaller, ice storage systems will have less maintenance than a traditional system. The ice thermal storage system also allows a chiller to undergo routine maintenance during the day when the ice storage can handle the system load.ENVIRONMENTALLY FRIENDLY
Reducing energy consumption and using electricity at night helps reduce global warming. Electricity generated at night generally has a lower heat rate (lower fuel use per power output), and therefore lower carbon dioxide and greenhouse gas emissions resulting in less global warming. The California Energy Commission concluded that the use of electricity at night created a 31 percent reduction in air emissions over the use of electricity during the day.With smaller chillers, an ice thermal storage system reduces the amount of refrigerant in a system. Using smaller amounts of refrigerant also helps to reduce global warming.
PROVEN TECHNOLOGY
Ice thermal storage has been successfully applied to thousands of installations worldwide. For example, Baltimore Aircoil Company (BAC) has supplied its Ice Chiller® thermal storage products for projects that range in size from 90 to 125,000 ton-hours (0.3 to 441.3 MWh). Installations include office buildings, hospitals, manufacturing processes, schools, universities, sports arenas, produce storage facilities, hotels, and district cooling applications.Products include factory-assembled units. For large applications, where space is limited or factory-assembled units are not cost effective, thermal storage coils are available for installation in field-erected tanks. Ice can be built using various refrigerants or glycols on steel coils and is used to provide either chilled water or glycol to the cooling system. This flexibility allows a unit to be provided that meets the user's specific requirements.
Excerpted and reprinted from the Baltimore Aircoil Company (BAC) Product & Application Handbook. For more information, visit www.baltimoreaircoil.com.
Publication date: 09/18/2006
Report Abusive Comment