CO2 refrigeration (R-744) systems operate at significantly higher pressures compared to legacy hydrofluorocarbon (HFC) systems. For example, on hot summer days, between its medium-temperature compressors and pressure-reducing valves, a rooftop system can reach pressures of 1,400 psig.
While pressurization is an important part of working with CO2 refrigeration systems, with the proper training and preparation, it’s just another consideration in the process.
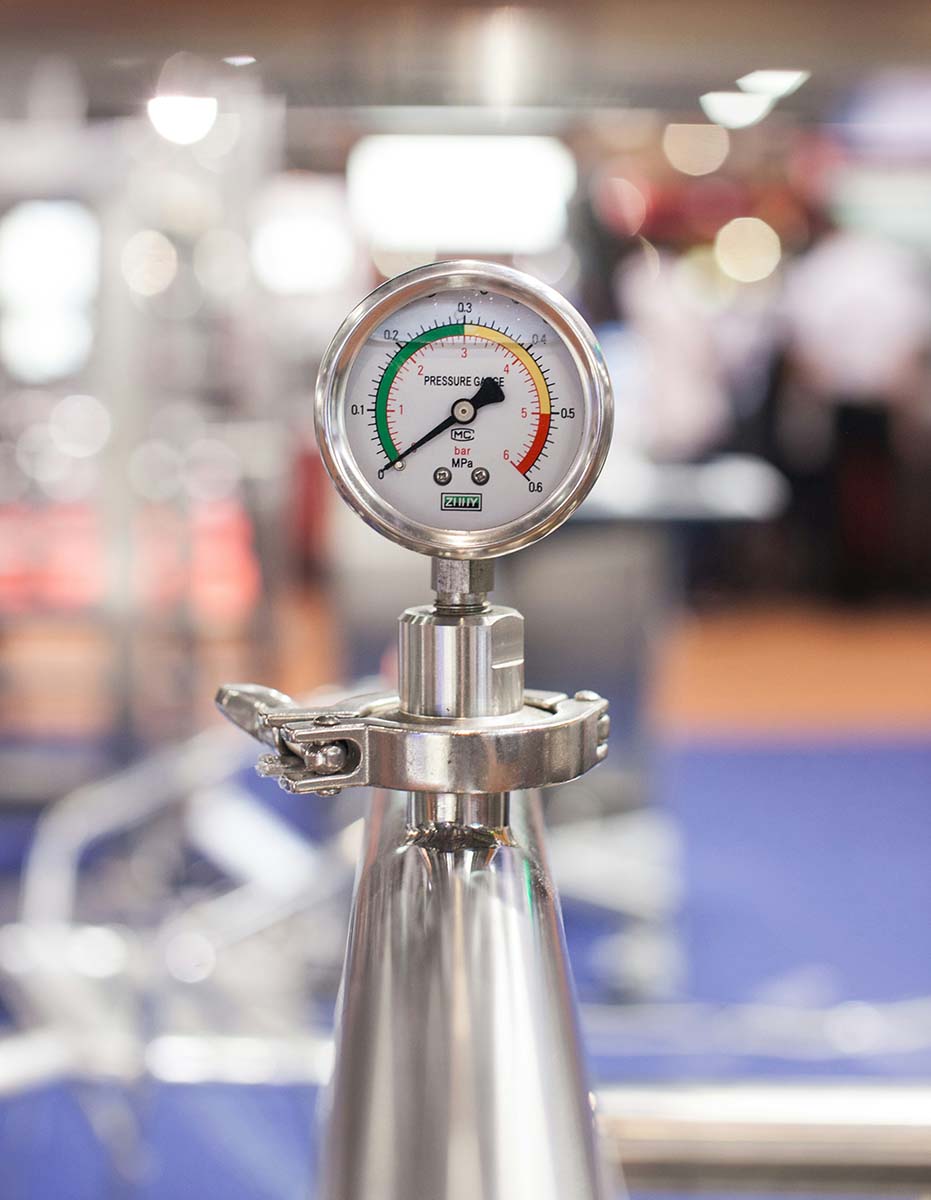
In an effort to handle such extreme pressures, R-744 systems are equipped with pressure relief valves (PRVs) — critical safety components designed to ensure the system is compliant and operating safely and reliably. (Courtesy of Crystal Kwok | Unsplash)
In an effort to handle such extreme pressures, R-744 systems are equipped with pressure relief valves (PRVs) — critical safety components designed to ensure the system is compliant and operating safely and reliably. The proper design, installation, and maintenance of these valves is vital for the safe operation of R-744 refrigeration systems, especially in industrial and commercial applications.
What Are Pressure Relief Valves?
PRVs are designed to protect systems from overpressure conditions. If the pressure within a system surpasses a predetermined pressure level, known as the PRV set point, the valve will open, relieving the pressure level.
These devices can be helpful in many scenarios, including:
- Abnormal Pressure Conditions: Sudden unexpected changes in operation, malfunctioning components, or other unforeseen circumstances may lead to an increase in system pressure beyond safe operating limits. When this occurs, a PRV can open, helping to alleviate some of the pressure from overworking the system.
- During Startup and Shutdown: PRVs can be used to protect piping and components, ensuring the system remains within the recommended operating range.
- Temperature Changes: As ambient conditions change, CO2 refrigeration systems’ temperatures may fluctuate in response when offline. As temperature affects pressure, a PRV can help ensure the system can accommodate these changes without exceeding safe pressure limits.
- System Design Changes: When modifying piping, ensure a check valve is allowing flow back to the rack when the circuit is isolated. It is uncustomary for piping to be added without a check valve or pressure relieving ball valve, but if it were to be done, a PRV would be necessary.
- Emergency Situations: If there is a sudden failure or malfunction within the CO2 refrigeration system that leads to a rapid increase in pressure, the PRV may activate to release pressure and prevent catastrophic damage.
- Compliance with Regulations: Many industrial and safety regulations mandate the use of PRVs in R-744 refrigeration systems. Ensuring compliance with these regulations is a key reason to use PRVs, as they can help maintain a safe working environment and prevent potential legal and regulatory issues.
Where Should They Go?
The placement of pressure relief valves in CO2 refrigeration systems is largely dictated by ASHRAE 15, “Safety Standards for Refrigeration Systems,” and IIAR CO2, “Safety Standard for Closed-Circuit Carbon Dioxide Refrigeration Systems.”
The latest version of ASHRAE 15 (2016) includes numerous updates regarding PRVs, including revisions to relief vent pipe discharge locations, design provisions for headered relief vent systems, and updated R-744 design pressure requirements.
“Typically, these valves are strategically positioned,” said Evan Aschow, lead engineer, Effecterra. “Specifically, they are commonly found on the low-temperature suction, medium-temperature suction, medium-temperature discharge, and the flash tank.”
In addition to these primary locations, PRVs may also be installed at other points, including the low-temperature discharge and oil reservoir, said Aschow.
“Adhering to these standardized placements ensures compliance with industry safety standards and helps mitigate potential risks associated with over-pressurization in the system,” he said.
Trevor Matthews, founder of Refrigerationmentor.com, said there are many factors to consider when utilizing PRVs on R-744 systems.
“There are numerous pressure zones operating within a system at any given time, and it’s important for a tech to monitor all of those locations,” he said. “Typically, when it comes to pressure relief valves, you should consider the transcritical side or high-pressure side, subcritical side, flash tank, medium-temperature suction, and low-temperature suction. Of course, it all depends on the manufacturer’s design, whether it’s a low or high pressure design, where you’re located, and what code you’re working under. Usually, this is all laid out by the manufacturer, so the technicians don’t have to worry about any of it.”
Travis Kisner, regional service sales director at JAX Refrigeration Inc., said pressure relief valves could potentially be put anywhere liquid can be trapped.
“Nobody wants a relief valve on an evaporator, but if there’s a chance liquid can get trapped in there, you absolutely need to consider putting one there,” he said. “I believe everything should be independent, and every piece of the system needs to be evaluated, all the way through.”
High Side Vs. Low Side
On a refrigeration system, the high side generally incorporates the evolution of a high-pressure gas to a high-pressure liquid. This occurs through the compression of the refrigerant and excess heat is released in the condenser. On the other hand, the low side includes the expansion of the refrigerant, absorption of heat in the evaporator, and transition from a low-pressure liquid to a low-pressure gas.
“Pressure relief valves positioned on either the suction or discharge sides are not notably distinct, aside from their designated pressure ratings,” said Aschow. “Currently, there exists a substantial pressure differential between the low-temperature suction [435 psi] and the medium-temperature discharge [1,740 psi]. However, in the forthcoming generation of systems presently undergoing design review in North America, there is a trend toward deploying higher pressure-rated systems. This shift aims to reduce or eliminate instances of systems venting and losing their charge. In contrast, Europe and Australia already implement systems with minimum pressure requirements of 870 psi, resulting in a greater ability to retain refrigerant within the system before any venting occurs. This strategic adoption of higher pressure ratings reflects a global effort to enhance safety and minimize environmental impact in refrigeration systems.”
As far as extreme pressures go, Kisner said techs need to be prepared to enter unchartered territory when working on R-744 systems.
“Your average HVAC refrigeration guy has likely never experienced pressure this high,” he said. “On the lower side, the pressures are much lower, around 500 psi, which is much more familiar. That ‘oh my God’ factor is fairly nonexistent on the low side.”
Kisner said techs should use all senses, including their hearing when seeking out CO2 pressure issues.
“CO2 is a much louder refrigerant than R-22 or R-410A,” he said. “At 1,200 psi, you can sort of hear a whistle when there is that much pressure behind a leak. You can almost walk to it and say, ‘There it is.’”
Have No Fear
Matthews said most CO2 refrigeration equipment manufacturers continue to build systems with pressure and the technician in mind, simplifying installation and maintenance procedures.
“The manufacturers in North America and Europe are putting all the right things in place, especially when it comes to pressure release valves,” he said. “They're very keen on ensuring technicians have all the right information. In fact, many CO2 manufacturers in North America will even send a technician out to the specific supermarket to help with startup. Simply put, the manufacturers are doing their best to support their equipment.”
When it comes to PRVs, Matthews encourages techs to learn as much as they can, equip themselves with the proper personal protective equipment, and proceed confidently and cautiously.
“Techs should wear glasses and gloves and, in a safe manner, open a bottle of CO2,” he said. “Encountering the gas at 800-900 psi will help familiarize them with the refrigerant and give them a good idea of what to expect if a PRV opens.
“Techs need to understand how pressure relief valves work, where they should be placed, and the purpose they serve,” he continued. “If and when they pop off, you’re going to get a shock, because they can be very loud. However, these systems are not much different than HFC systems.”
When finishing up, Kisner encouraged techs to employ the skills of a professional engineer.
“This final set of eyes will greatly improve site operation and ensure all system components are safely installed and protected,” he said. “All sequences of operation should be reviewed and checked out once the system is ready to be turned over to the customer.”
Aschow said CO2 refrigeration systems have arrived, and they have a bright future in the North American market.
“The versatility of CO2 as a natural refrigerant is a highly attractive trait for various applications, including refrigeration, air conditioning, and heating,” he said. “Its ability to serve multiple purposes makes it a well-rounded solution in the short- and long-term future.”