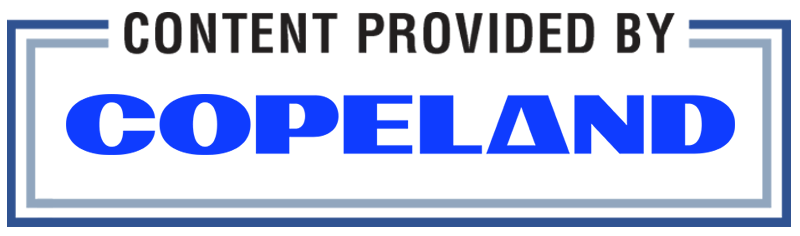
Adoption of CO2 transcritical booster (TCB) systems in supermarkets is approaching 50k installations worldwide and increasing rapidly in the U.S. Designed with a gas cooler (condenser) that’s typically located on the roof of a facility, CO2 TCB system efficiencies are impacted significantly by rising ambient temperatures. When ambient temperatures rise above 75 °F, systems with a dry gas cooler transition from subcritical to supercritical operation (aka transcritical mode) — decoupling pressures and temperatures and consuming more energy.
But climate is not the only factor in the total cost of ownership equation. Stakeholders should also evaluate the costs and availability of electric utilities and water. Recent technological advancements are helping to drive CO2 TCB system adoption by configuring design optimization strategies that maximize efficiencies in various climate and/or installation conditions.
Per the American Society of Heating, Refrigerating and Air-Conditioning Engineers (ASHRAE), the continental U.S. is made up of seven climate zones, cross-categorized by their relative humidity characteristics of marine, dry, moist and warm-humid. CO2 system designers and manufacturers must be aware of these ambient conditions to give end users options to maximize performance and efficiencies.
The base configuration of a CO2 TCB system is designed to perform well in a wide range of climate zones. Emerging design optimization strategies give manufacturers options to tailor each system per installation based on climate, utility costs and/or water availability.
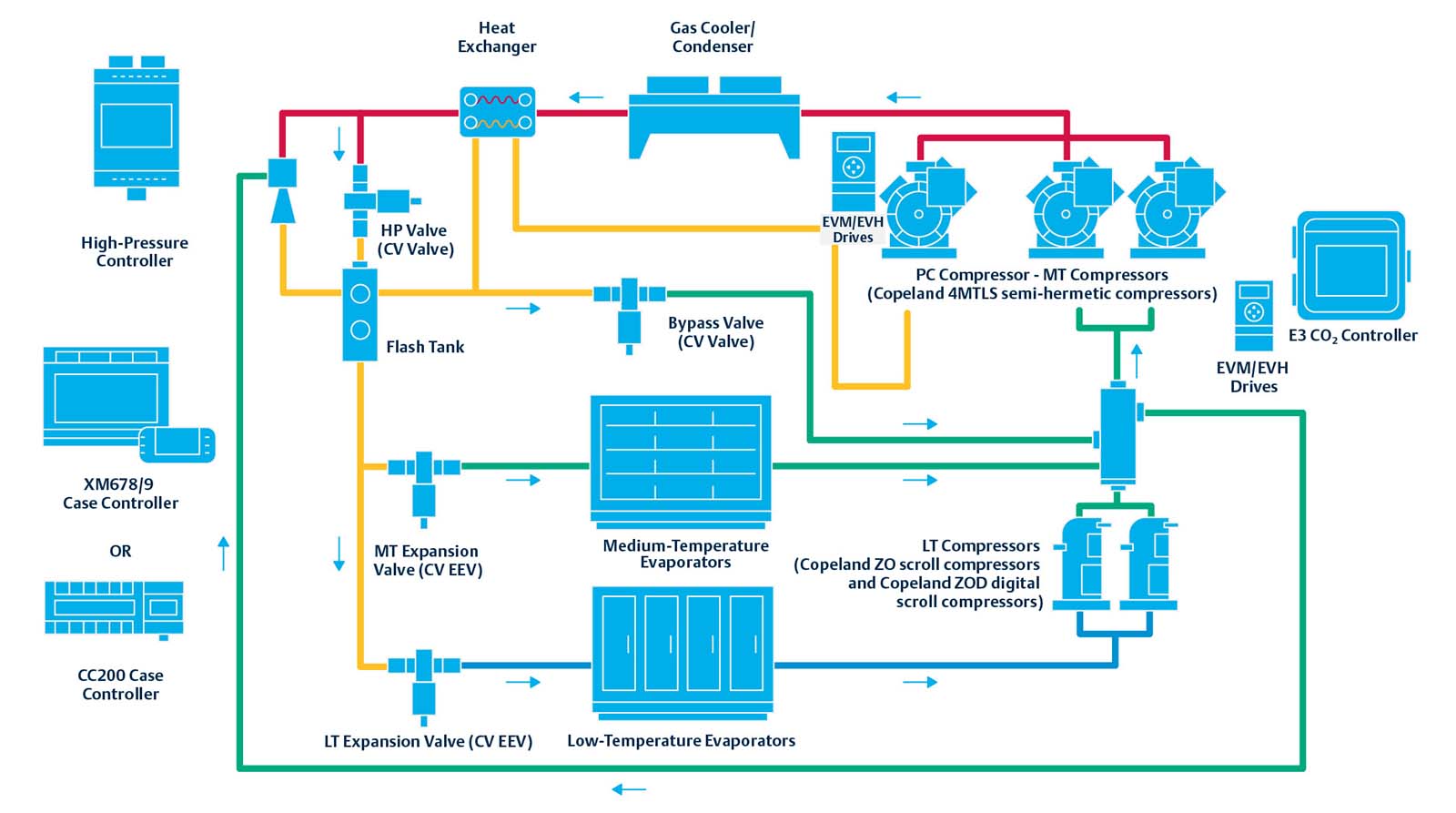
Click chart to enlarge
Parallel compression — Adds a supplemental “parallel” suction group to the medium-temperature (MT) compressors, enabling the parallel compressor to operate at a higher suction pressure and generate higher compressor capacity for less effort. Delivers 5–10 percent reductions in energy costs.
Adiabatic gas cooling — Adiabatic (wetted) pre-cooling pads are installed outside the gas cooler’s condenser coil. Air is cooled as it is pulled through these pads to delay the system from entering supercritical operation during seasonal warm periods. Delivers up to 25 percent energy reductions in warm, dry climates.
Mechanical sub-cooling — A small mechanical vapor-compression loop is coupled to the main cycle at the exit of the gas cooler, cooling the supercritical fluid exiting the outlet. This supplemental unit is activated only when the ambient temperature exceeds a specified setpoint to improve energy efficiency during warmer operating hours.
Gas ejectors — Gas ejectors are designed to increase the gas mass flow in the receiver/flash tank, divert vapor from the MT suction group, and enable the parallel compressor suction group to run more efficiently. The net result is achieving higher compressor capacity for less effort, which translates into a lower heat of compression and reduced energy consumption during warm periods.
Low to zero MT superheat (annualized energy optimization) — This technique is designed to deliver annualized energy savings that are not impacted by regional climate conditions. Instead of focusing on the high-side gas cooler, this low-side approach is designed to achieve low to near zero superheat by: flooding the MT evaporators; increasing suction pressure (PSI); and reducing compression ratios. When annualized, this strategy can deliver significant savings in energy costs.
Report Abusive Comment